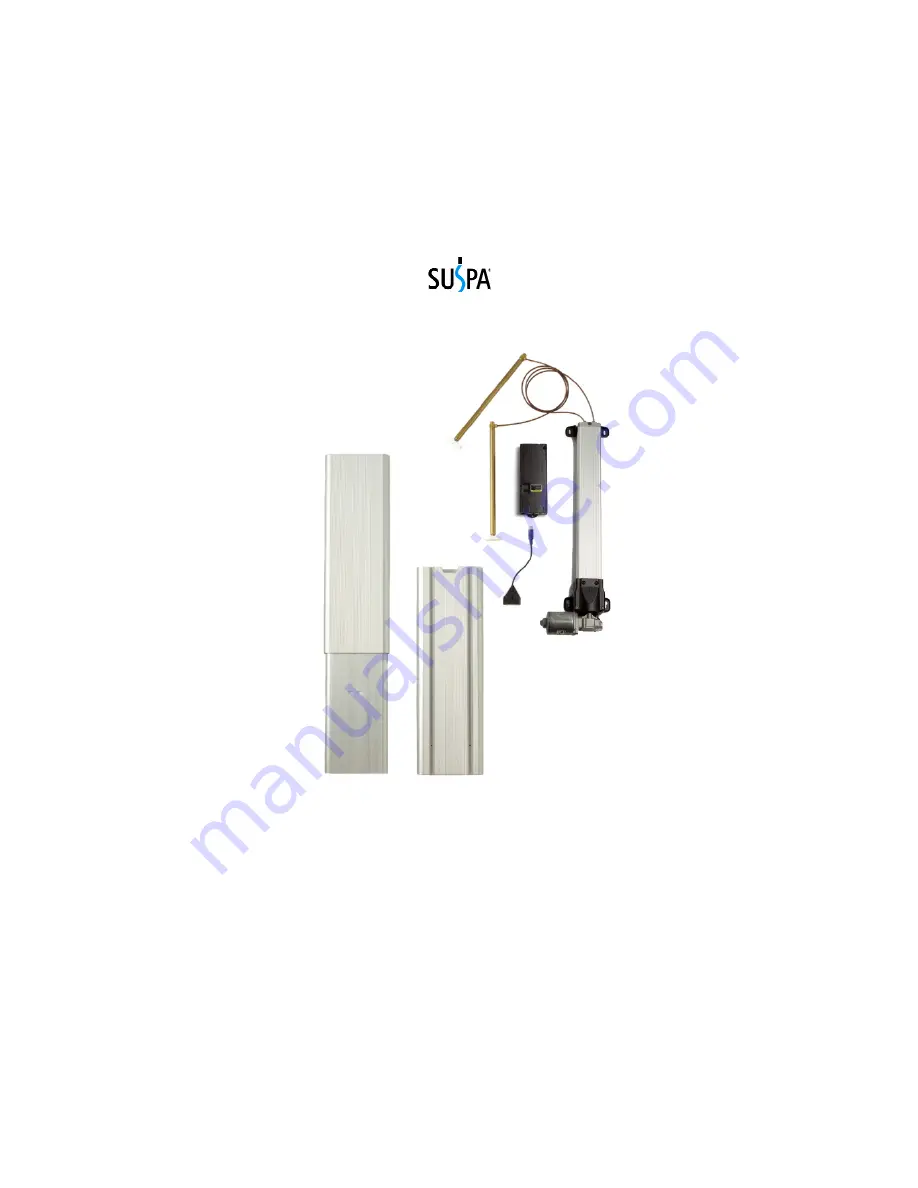
MOVOTEC
®
Q-Drive ATU
Lift System Manual
by
Copyright © 2012 by
Suspa
®
Incorporated
All rights reserved. No part of this manual may be reproduced or transmitted
in any form or by any means, electronic or mechanical, including photocopying,
recording, or by any information storage and retrieval system
without permission in writing from Suspa
®
Incorporated.