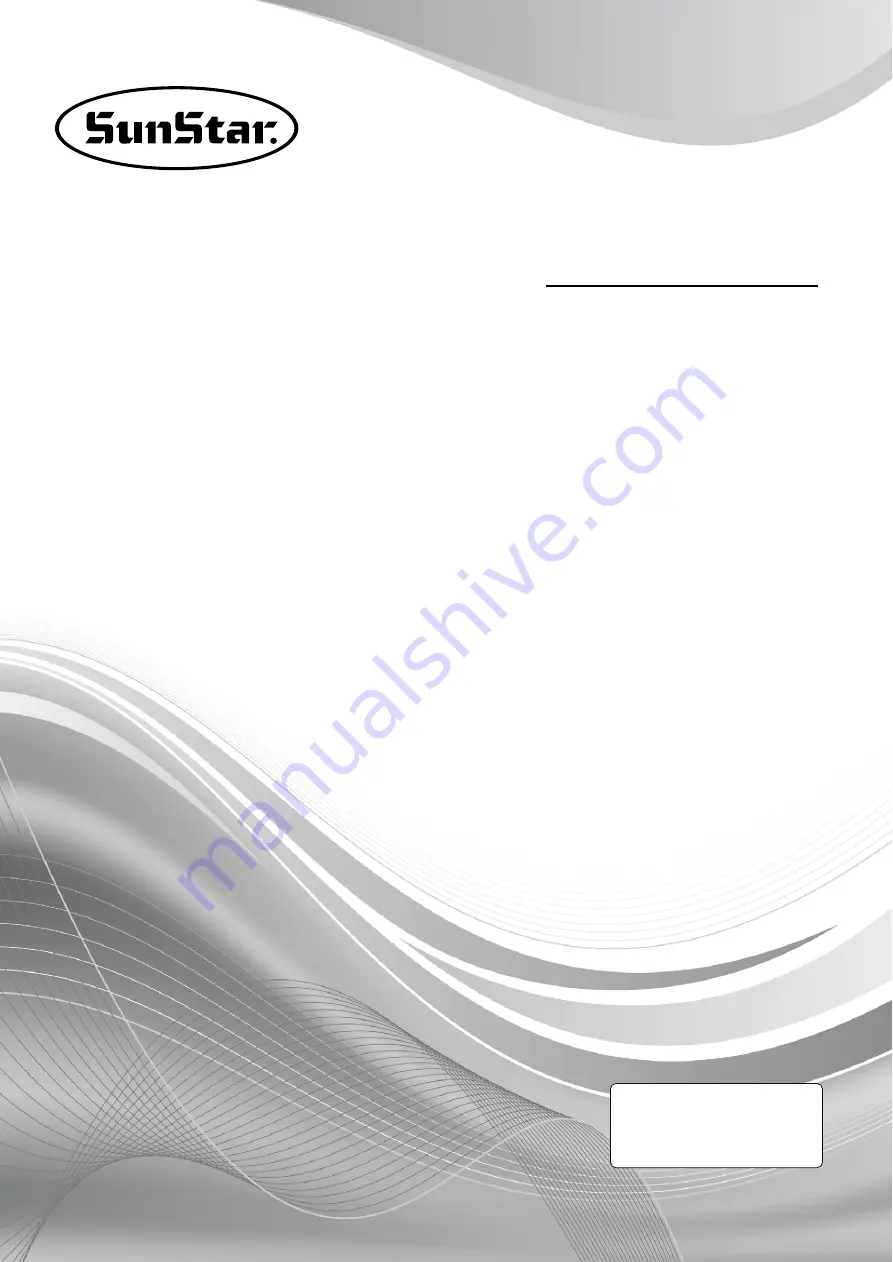
1) FOR AT MOST USE WITH EASINESS,
PLEASE CERTAINLY READ THIS MANUAL
BEFORE STARTING USE.
2) KEEP THIS MANUAL IN SAFE PLACE
FOR REFERENCE WHEN THE MACHINE
BREAKS DOWN.
M
MM
ME
E--0
09
90
09
92
29
9
USER
’
’
S MANUAL
R
S
Su
un
nS
Sttaarr C
CO
O..,, L
LT
TD
D..
SS-7350 Series
Small cylinder bed interlock
sewing machine