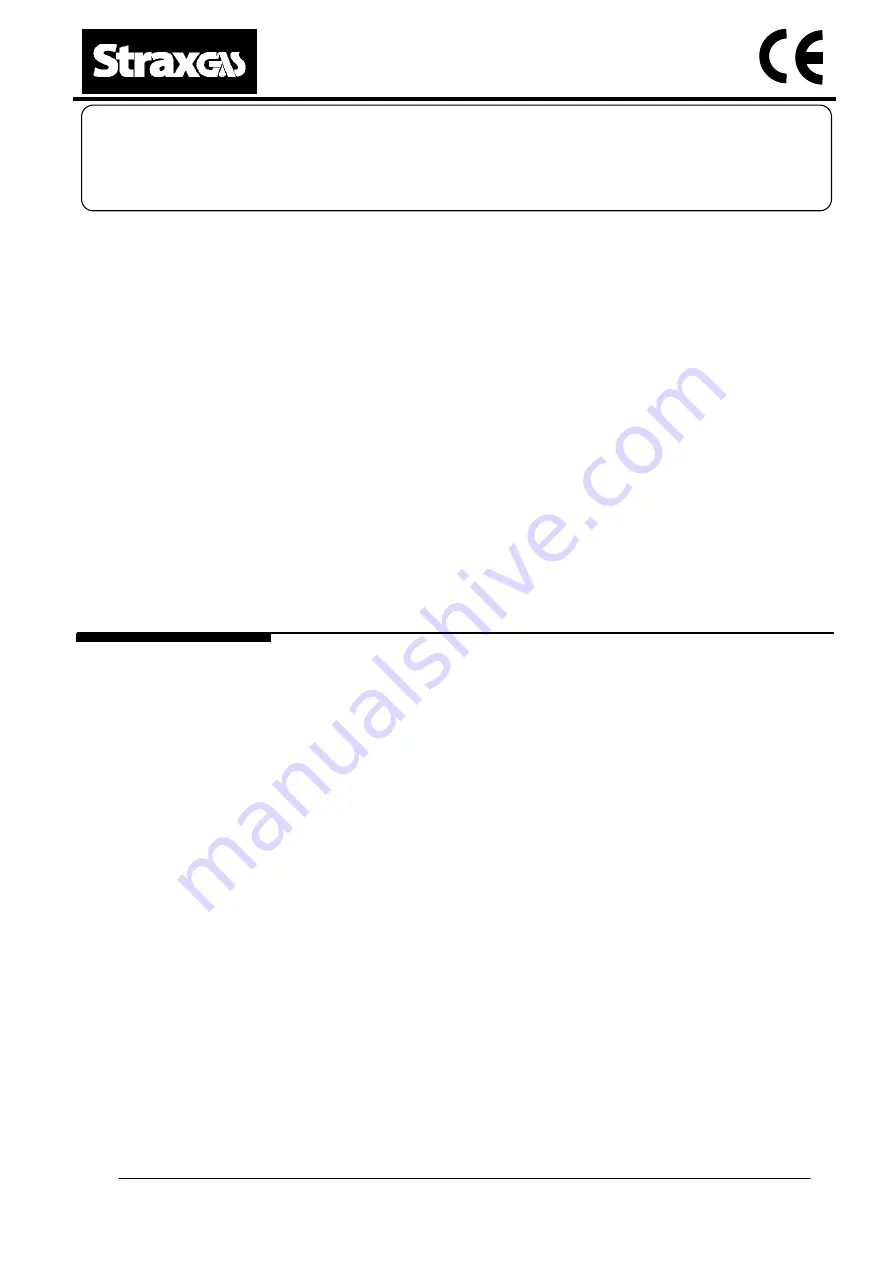
Flaire Issue 1.3 29/06/01
Page 1 of 11
Appliance data:
Type of gas
:
Natural gas (G20) Cat. I2H
Injector size
:
3 x 1.0 multihole
Injector marking
:
100
Gross heat input (high setting)
:
5.0kW (17,000Btu/h)
Gross heat input (low setting)
:
2.5kW (8,500Btu/h)
Supply pressure
:
20mbar (8in.w.g.)
Appliance test point pressure (cold)
:
19.5mbar (± 1.0mbar)
Type of flue
:
Class 1 (7in. dia.), Class 2 (5in. dia.) or precast block flue
Minimum effective height of chimney :
3m (10ft.)
Ignition
:
Piezo
Spark gap
:
3.0mm min., 4.5mm max.
Dimensions:
Width over frame excluding trims
:
484mm
Height including frame
:
583mm
Depth
:
102mm
Shipping weight
:
20kg
Country of destination
:
GB & IE
This appliance has been assessed by a Government appointed Notified Body and shown to
meet the 'Essential Requirements' of the European Gas Appliance Directive.
The Directive lays down requirements for the safety of the appliance, together with its design,
construction, and use of materials. It also requires the production process to be covered by an
approved and monitored system of quality assurance.
Mandatory requirements
Straxgas fires must be installed with due regard to the following
mandatory
regulations:
The relevant British Standard installation specifications and codes of practice, and Building
Regulations issued by the Department of the Environment, and Building Standards (Scotland)
Consolidated Regulations issued by the Scottish Development Board.
Current Gas Safety (Installation and Use) Regulations.
Failure to install this appliance correctly could lead to prosecution and render the guarantee
invalid.
Attention is drawn to the latest edition of the following standards:
BS1251, Specifications of open-fireplace components.
BS5440, Part 1 Specification for installation of flues.
BS5440, Part 2 Specification for installation of ventilation for gas appliances.
BS5871, Part 2 Installation of decorative fuel effect gas appliances.
BS6891, Specification of low pressure gas pipework
BS8303, Replacing CP403.
BS1289
This Straxgas appliance is an inset live fuel effect gas fire and must only be installed by a
competent person (e.g. a C.O.R.G.I. member) in accordance with these installation instructions.
This appliance must be installed in accordance with the rules in force, and used only in a
sufficiently ventilated space. Consult these instructions before installation and use of this
appliance.
Additional purpose made air ventilation is not normally required.
Ventilation must be provided in accordance with the rules in force.
INSTALLATION AND SERVICING INSTRUCTIONS
FOR THE STRAXGAS FLAIRE
(To be left with the appliance)
Division of Legge Fabheat Ltd.
Longfield Road, Leamington Spa, Warks. CV31 1XB
Tel. (01926) 882233 Fax. (01926) 450846 Email: [email protected]
Registered in England No 500091
IE & Northern Ireland
GB