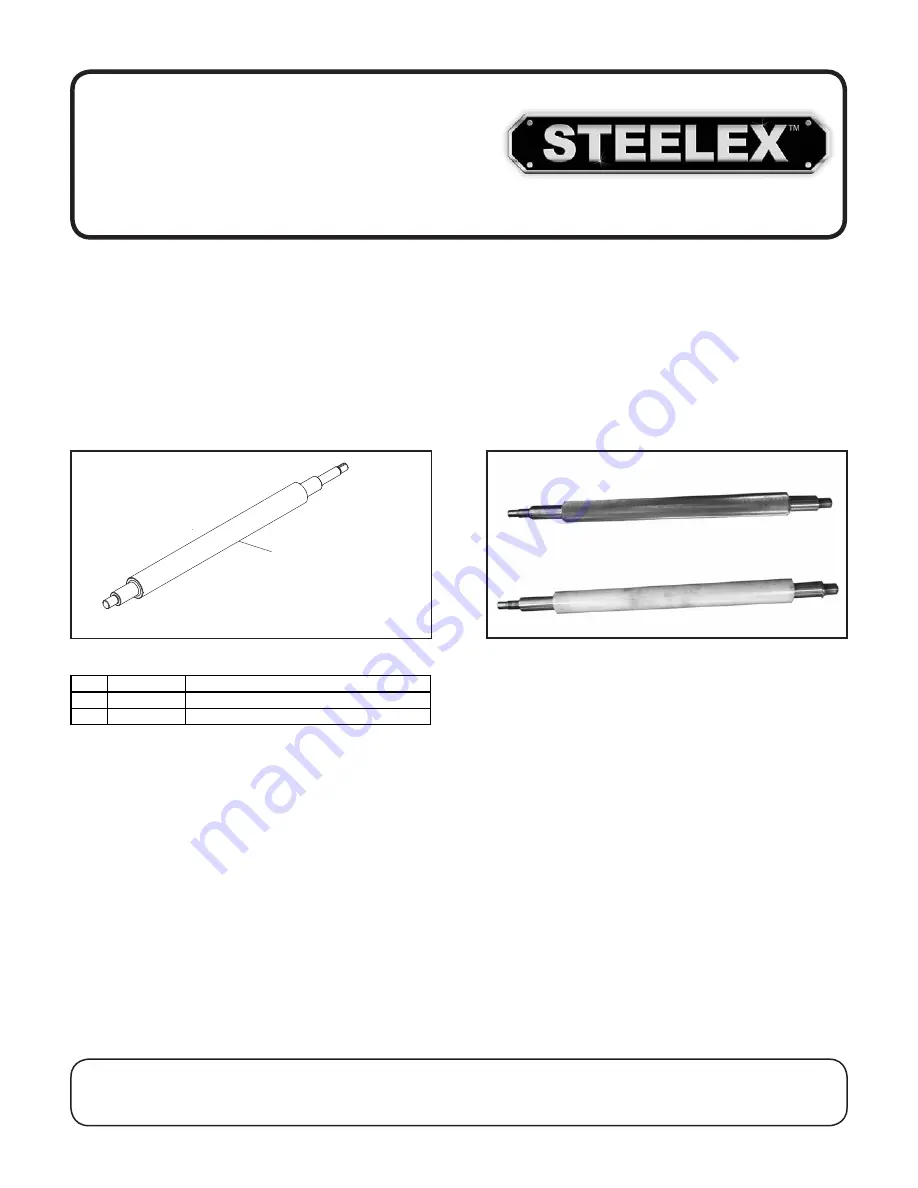
Model ST1007/ST1012/ST1014
***IMPORTANT UPDATE***
Applies to Models Mfd. Since 09/17
and Owner's Manual Printed 04/16
Phone: (800) 840-8420 • Tech Support: [email protected] • Web: www.woodstockint.com
The following change was recently made to these machines since the owner's manuals were printed:
•
Changed outfeed roller from serrated steel to rubber.
Aside from the information contained in this update, all other content in the owner's manual applies and MUST be
read and understood for your own safety. IMPORTANT: Keep this update with the owner's manual for future
reference.
If you have any further questions, contact our Technical Support.
COPYRIGHT © AUGUST, 2017 BY WOODSTOCK INTERNATIONAL, INC.
WARNING: NO PORTION OF THIS MANUAL MAY BE REPRODUCED IN ANY SHAPE OR FORM WITHOUT
THE WRITTEN APPROVAL OF WOODSTOCK INTERNATIONAL, INC.
Printed in China
READ THIS FIRST
#19144BL
163V2
(ST1007, ST1012)
68V2
(ST1014)
V2 Outfeed Roller
REF PART #
DESCRIPTION
163V2 XST1007163V2 OUTFEED ROLLER (RUBBER) V2.09.17 (ST1007)
163V2 XST1012163V2 OUTFEED ROLLER (RUBBER) V2.09.17 (ST1012)
68V2 XST1014068V2 OUTFEED ROLLER (RUBBER) V2.09.17 (ST1014)
V1 & V2 Outfeed Roller Photos
V2
V1