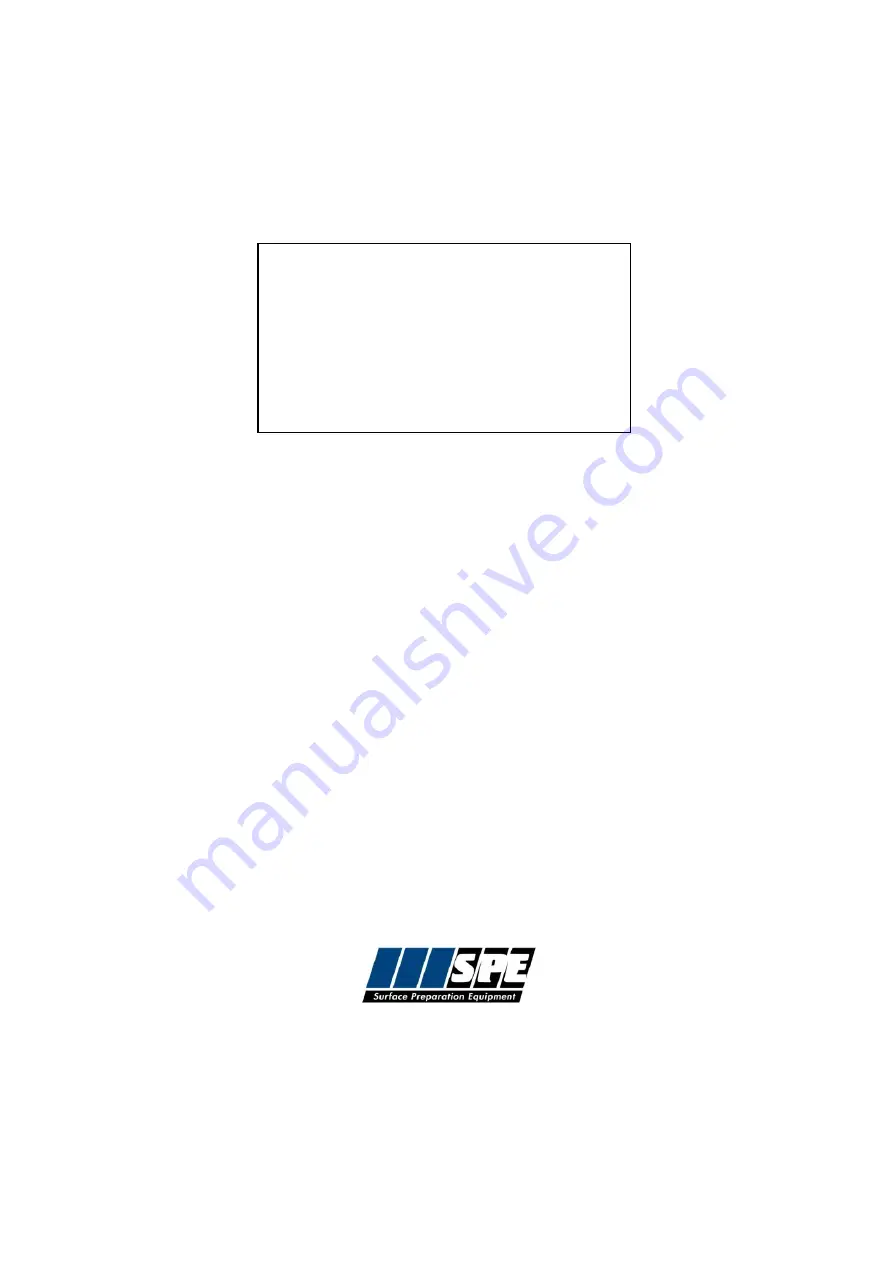
BEF200-1
& BEF60 Edger
Operating Manual
This manual is provided to persons purchasing an
SPE machine and may not be reproduced in part or full
without written permission of
SPE International Ltd.
This manual provides the basic information required
and is only to be used as a guideline.
The SPE machines are manufactured and covered by
SPE design registrations granted and pending.
SPE International Ltd reserves the right to alter the
equipment design and specification as required
without notice.
The SPE product range is subject to amendment and
improvement as a result of on going research
Honeyholes Lane, Dunholme, Lincoln LN2 3SU, England
Tel: +44 (0) 1673 860709 Fax: +44 (0) 1673 861119
Email: [email protected]
Summary of Contents for BEF200-1
Page 2: ......
Page 15: ......
Page 16: ......
Page 17: ...BEF200 1 Operating Manual 13 ...
Page 18: ......
Page 19: ......
Page 20: ......
Page 23: ...BEF200 1 Operating Manual 19 ...
Page 24: ......