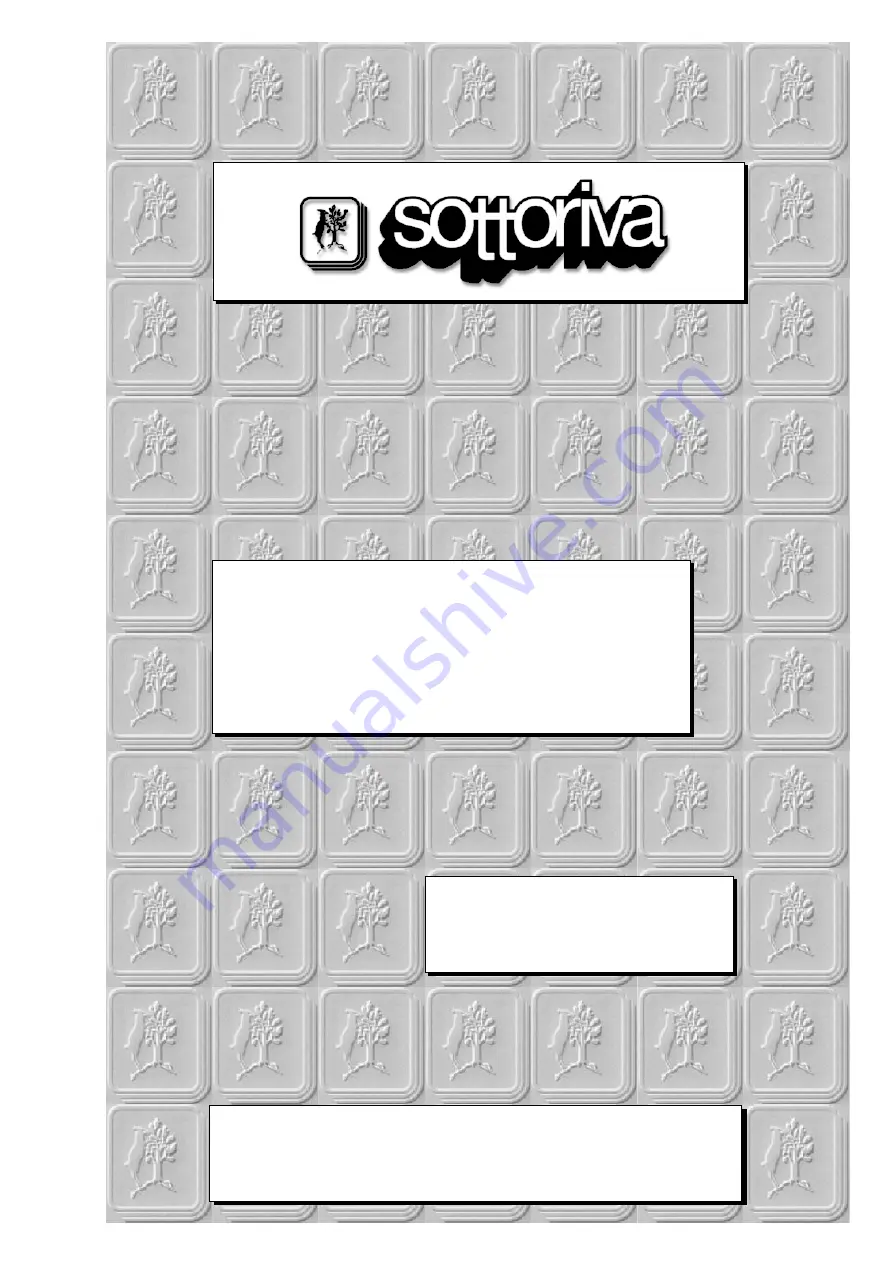
INSTRUCTIONS MANUAL
Piston type automatic divider
mod.
SVP 0/1/2/3-E
Version: ENGLISH - Arc. 16
Code: 3529.0091.01
Revision: n° 0 dated 19/06/2001
Costruzioni Meccaniche SOTTORIVA S.p.A.
Via Vittorio Veneto, 63 - 36035 MARANO VICENTINO (VI) ITALY
Phone (+39) 0445.595.111 - Fax (+39) 0445.595.155
Internet: http://www.sottoriva.com - E-mail: [email protected]