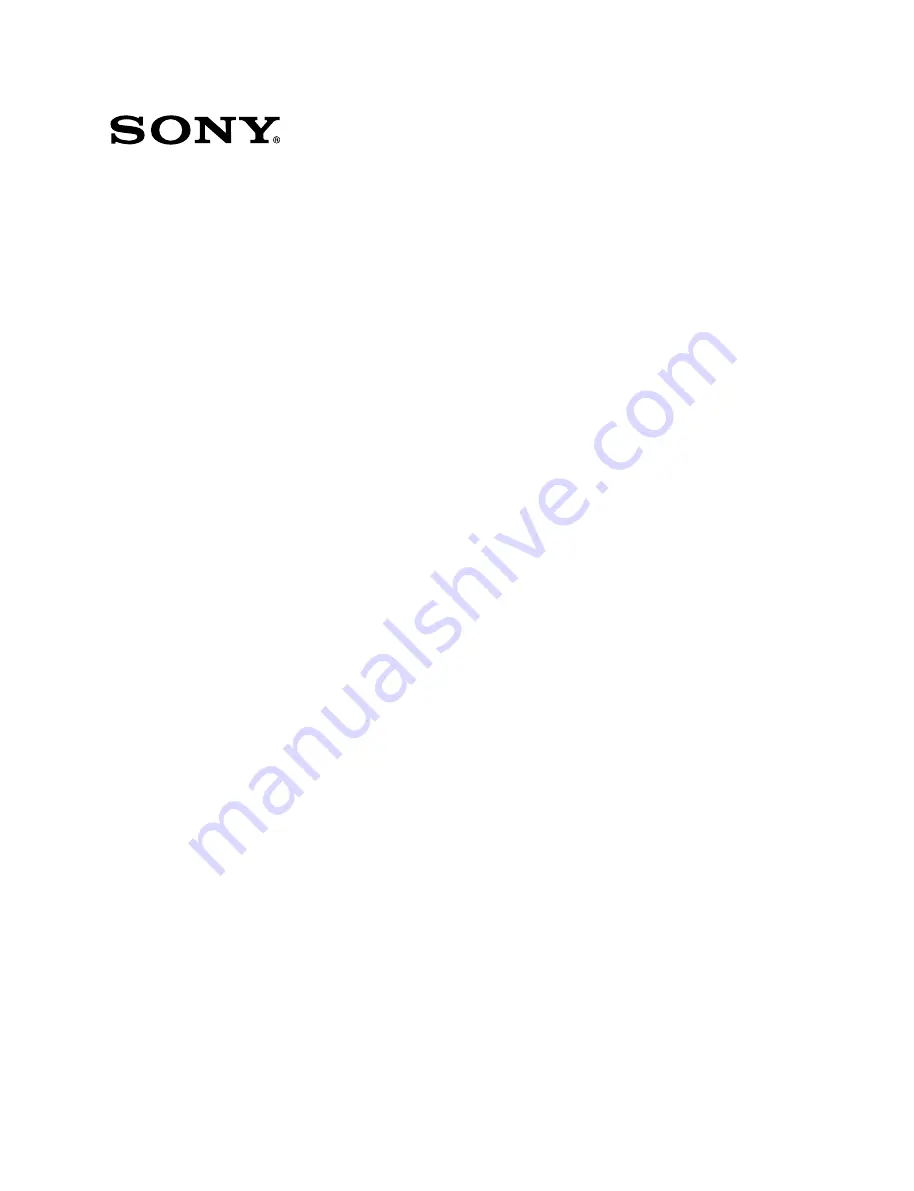
MAINTENANCE MANUAL
Part 1
1st Edition (Revised 3)
MULTI RESOLUTION FILM SCANNER
FVS-1000 System
FVS-T1000
TELECINE PROCESSOR
FVS-P1000
MULTI RESOLUTION TELECINE
BKFV-100/1
TELECINE HDTV PROCESSING BOARDS
TELECINE SDTV PROCESSING BOARDS
BKFV-200
TELECINE OPTICAL KIT
BKFV-410
TELECINE LOG DATA PROCESSOR
BKFV-300
TELECINE 16 mm FILM ADAPTOR KIT
BKFV-400/1
TELECINE MOUNTED SLIDE KIT
BKFV-420
TELECINE FILM SOUND PROCESSOR
BKFV-500