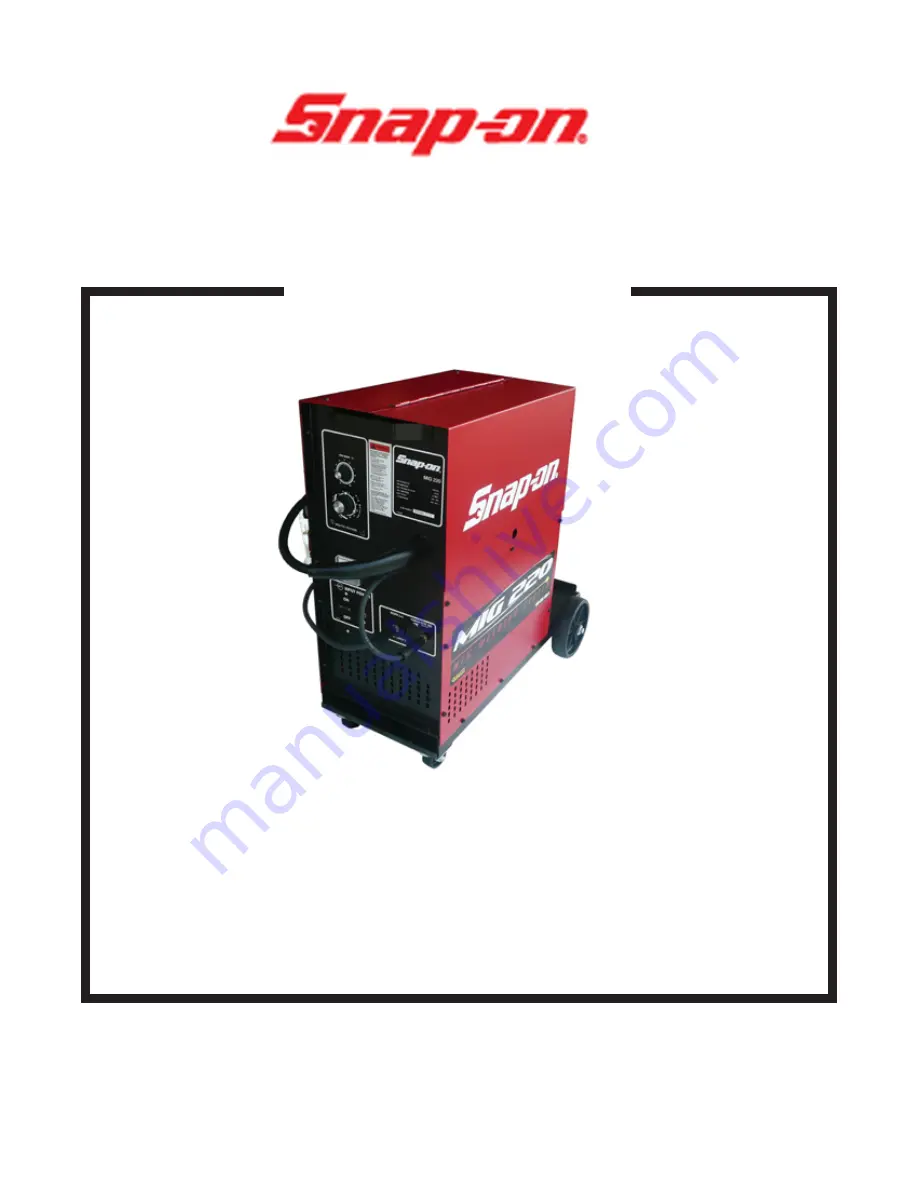
7/10/2009
OWNER'S MANUAL
THE MIG220 REPRESENTS THE LATEST TECHNOLOGY
IN MIG COMBINATION UNITS. THE MIG220 OPERATES ON
SINGLE PHASE CURRENT, AND FEATURES "SMOOTH ARC"
TRANSFORMER DESIGN CONCEPT.
MIG220
MIG COMBINATION UNIT
FOR TECH. SERVICE, CALL
Or
WWW.800ABCWELD.COM
At
Web
The
On
Us
Visit
Toll-Free 1-800-222-9353
FORM
INSTALLATION
OPERATION
MAINTENANCE