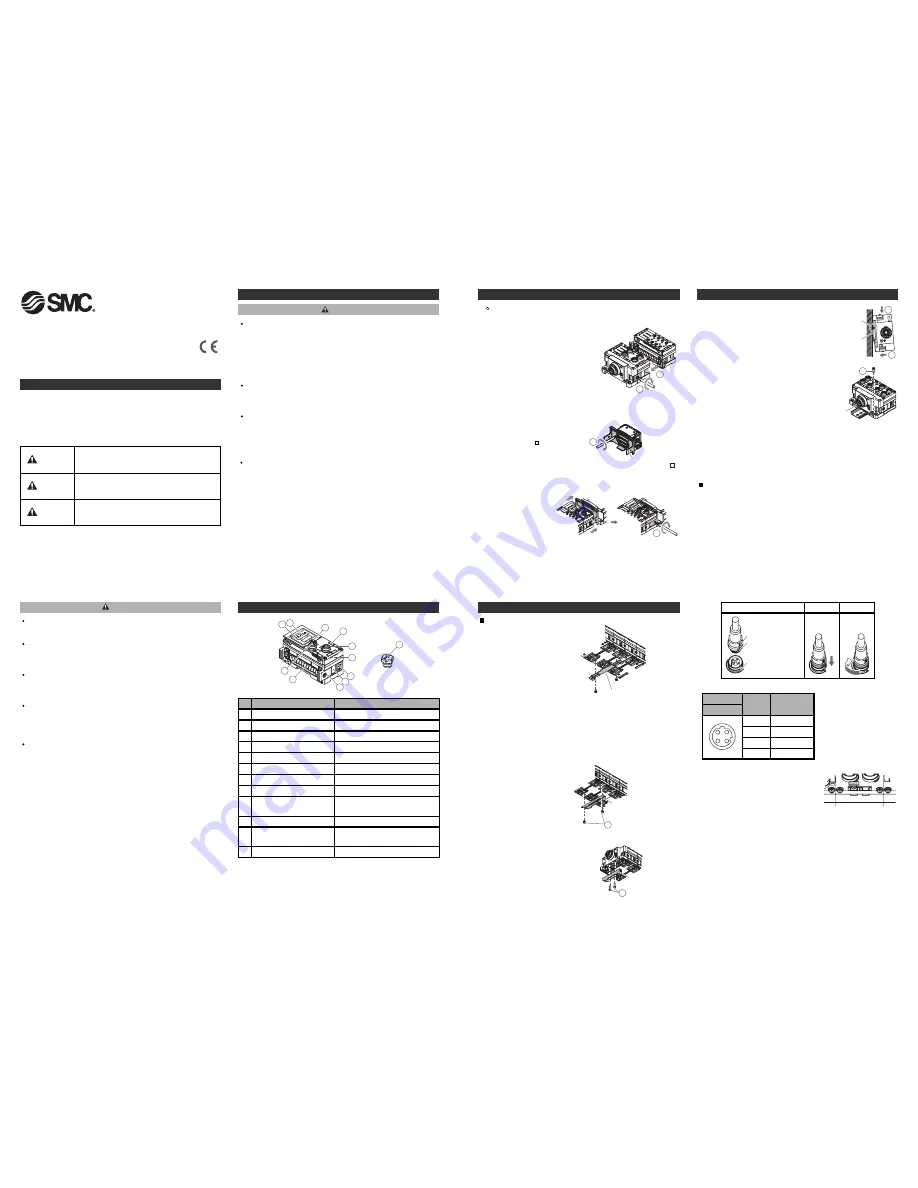
Installation & Maintenance Manual
Fieldbus system - SI unit
Type EX600-SEN1 / EX600-SEN2
Status display LED
Description
Function
Displays the status of the unit.
Display cover
Open to access the setting switches.
Display cover screw
Screw to open the display cover.
Marker groove
Groove for an identification marker.
Connector (PCI)
Connector for handheld terminal.
8
7
6
9
10
2
4
3
5
11
1
12
1
No.
2
3
4
5
Valve plate mounting hole
Holes for fixing the valve plate.
Valve plate mounting groove Groove for mounting the valve plate.
Joint bracket
Bracket for joining adjacent units.
6
7
8
Unit connector (Plug)
Connector for signals and power
supplies to adjacent units.
Connector (BUS IN)
Connector for Fieldbus inputs.
MAC address label
Displays the 12 digit MAC address
which is different for each SI unit.
9
10
11
Seal cap (1 pc.)
Fitted to unused connectors. (PCI)
12
Do not disassemble, modify (including changing the printed
circuit board) or repair.
An injury or failure can result.
Do not operate the product outside of the specifications.
Do not use for flammable or harmful fluids.
Fire, malfunction, or damage to the product can result.
Verify the specifications before use.
Do not operate in an atmosphere containing flammable or
explosive gases.
Fire or an explosion can result.
This product is not designed to be explosion proof.
If using the product in an interlocking circuit:
•Provide a double interlocking system, for example a mechanical
system.
•Check the product regularly for proper operation.
Otherwise malfunction can result, causing an accident.
The following instructions must be followed during maintenance:
•Turn off the power supply.
•Stop the air supply, exhaust the residual pressure and verify that the
air is released before performing maintenance.
Otherwise an injury can result.
Safety Instructions
These safety instructions are intended to prevent hazardous situations
and/or equipment damage.
These instructions indicate the level of potential hazard with the labels of
"Caution", "Warning" or "Danger". They are all important notes for safety
and must be followed in addition to International standards (ISO/IEC),
Japan Industrial Standards (JIS) and other safety regulations.
Warning
CAUTION indicates a hazard with a low level of risk
which, if not avoided, could result in minor or
moderate injury.
Caution
Warning
Danger
WARNING indicates a hazard with a medium level
of risk which, if not avoided, could result in death or
serious injury.
DANGER indicates a hazard with a high level of risk
which, if not avoided, will result in death or serious
injury.
Summary of Product parts
Mounting and Installation
EX600-TFN25
This product is class A equipment that is intended for use in an industrial
environment.
There may be potential difficulties in ensuring electromagnetic
compatibility in other environments due to conducted as well as radiated
disturbances.
(1)
Mark A
Mark B
Mark C on the
u
nit
(2)
(3)
•Connector pin assignment
TX+
Signal name
RX+
TX-
RX-
1
Pin
number
2
3
1
2
3
4
BUS IN
Configuration
4
Mounting and Installation (Continued)
NOTE
The direct current power supply to combine should be UL1310 Class2
power supply when conformity to UL is necessary.
Caution
When handling, assembling or replacing the unit:
•Avoid touching any sharp metal parts of the connectors for connecting
units.
•When assembling units, take care not to get any fingers caught
between units. Injury can result.
•When disassembling units, take care to avoid excessive force.
The connection parts of the unit are firmly joined with seals and injury
can result.
After maintenance is complete, perform appropriate functional
inspections.
Stop operation if the equipment does not function properly.
Safety cannot be assured in the case of unexpected malfunction.
Provide grounding to assure the safety and noise resistance of
the Fieldbus system.
Individual grounding should be provided close to the product with a
short cable.
Safety Instructions (Continued)
Assembly
Assembling the unit as a manifold
(1) Connect a unit to the end plate.
Digital and Analogue I/O units can
be connected in any order.
Tighten the joint brackets to a
torque of 1.5 to 1.6 Nm.
(2) Add more I/O units.
Up to 10 units (including the SI unit)
can be connected to one manifold.
(3) Connecting the SI unit.
After connecting the required I/O
units, connect the SI unit.
The method is as above in (1), (2).
(4) Mounting the valve plate.
Mount the valve plate
(EX600-ZMV ) to the valve
manifold using the valve set
screws. (M3x
8
)
Apply 0.6 to 0.7 Nm tightening
torque to the screws.
(5) Connect the SI unit to the valve manifold.
Insert the valve
plate into the valve
plate mounting
groove on the side
of the SI unit.
Fix using the valve
plate screws
(M4x6) supplied, to a torque of 0.7 to 0.
8
Nm.
1
2
4
Valve plate
(EX600-ZMV )
5
Installation
•Direct mounting
(1) When joining six or more
units, fix the middle part of
the complete EX600 unit with
an intermediate reinforcing
brace (EX600-ZMB1) before
mounting, using 2-M4x5
screws.
Tightening torque:
0.7 to 0.
8
Nm.
(2) Mount and tighten the end
plate at one end of the unit. (M4)
Tightening torque: 0.7 to 0.
8
Nm.
Fix the end plate at the valve side while referring to the operation
manual of the corresponding valve manifold.
Intermediate reinforcing
brace
(EX600-ZMB1)
•DIN rail mounting
(Not available for SY series
valves. Refer to the SY
catalogue.)
(1) When joining six or more
units, fix the middle part of
the complete EX600 unit
with an intermediate
reinforcing brace
(EX600-ZMB2) before
mounting, using 2-M4x6 screws.
Tightening torque: 0.7 to 0.
8
Nm.
(2) Mount the end plate bracket
(EX600-ZMA2) to the end plate at
the opposite end to the valves, using
2-M4x14 screws.
Tightening torque: 0.7 to 0.
8
Nm.
Intermediate reinforcing
brace
(EX600-ZMB2)
1
End plate bracket
(EX600-ZMA2)
2
(3) Hook the DIN rail mounting
groove on to the DIN rail.
(4) Press the manifold using its
side hooked to the DIN rail
as a fulcrum until the
manifold is locked.
3
4
DIN rail
DIN rail mounting groove
End plate bracket
(EX600-ZMA2)
5
(5) Fix the manifold by tightening
the DIN rail fixing screws
of the EX600-ZMA2. (M4x20)
Tightening torque:
0.7 to 0.
8
Nm.
The tightening torque at the
valve side depends on the
valve type.
Refer to the operation manual of
the corresponding valve manifold.
Wiring
•Connect the M12 connector cable.
The M12 SPEEDCON connector connection method is explained
below.
(1) Align mark B on the metal bracket of the cable connector
(plug/socket) with mark A.
(2) Align with mark C on the unit and insert the connector vertically.
If they are not aligned, the connector cannot be connected
correctly.
(3) When mark B has been turned 1
8
0 degrees (1/2 turn), wiring is
complete. Confirm that the connection is not loose. If turned too
far, it will become difficult to remove the connector.
•Identification marker
The signal name of the input or output
devices and unit address can be written
on the marker, and can be installed on
each unit.
Mount the marker (EX600-ZT1) into the
marker groove as required.