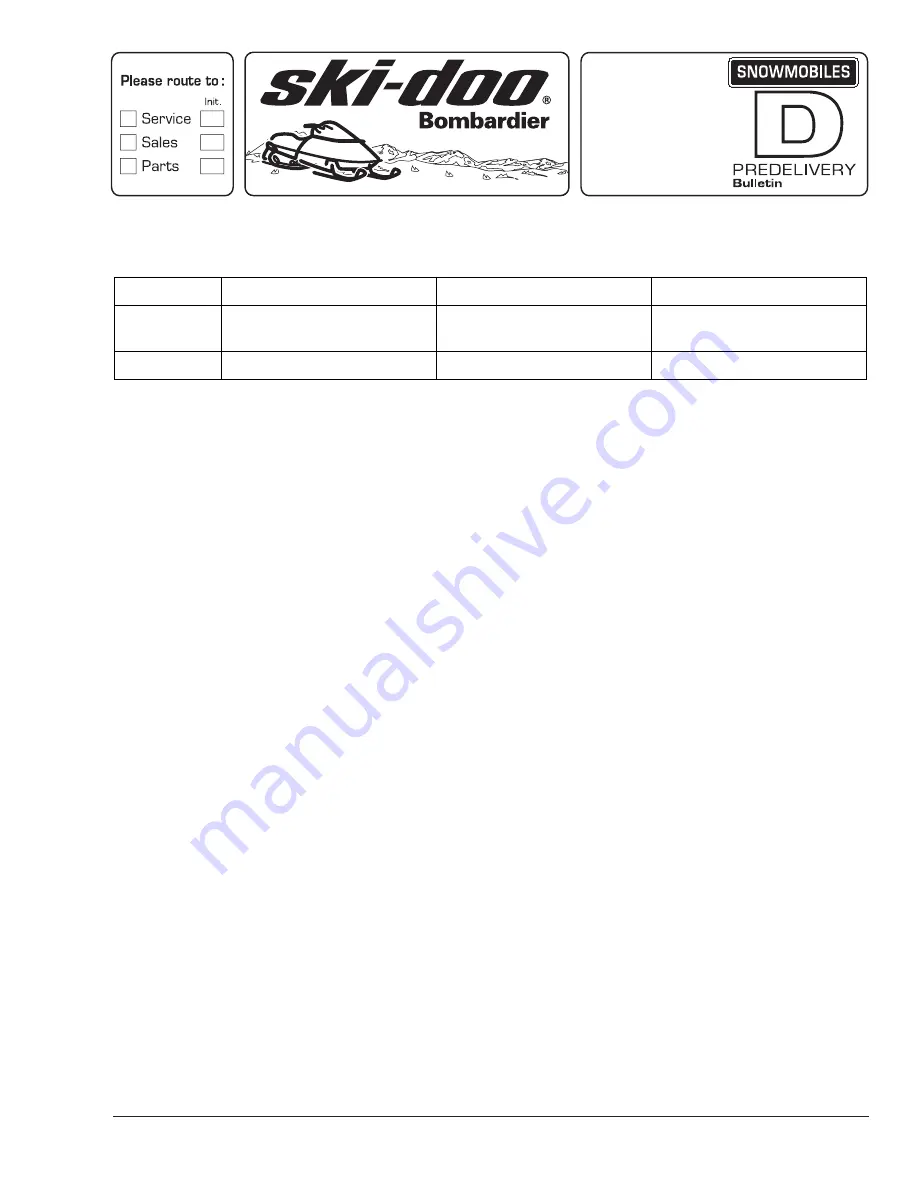
97-1
Page 1 of 10
No.
97-1
Revision 1
Date : March 18, 1996
Litho’d in Canada (MBL-9702 GM)
®* Trademarks of Bombardier Inc.
All rights reserved © Bombardier Inc. 1996
Campaign no. 00000
YEAR
MODEL NAME
MODEL NUMBER
SERIAL NUMBER
1997
Tundra II LT
(Canada and United States)
3266
All
1997
Tundra II LT (Europe)
3267
All
This bulletin must be used in conjunction with the check list enclosed in Operator's Guide bag. Make sure
that predelivery check list is completed and signed.
◆
WARNING : To obtain warranty coverage, predelivery procedures must be performed by an
authorized Bombardier snowmobile dealer. Apply all necessary torques as indicated.
O
NOTE :
The Information and components / system descriptions contained in this document are
correct at the time of publication. Bombardier Inc. however, maintains a policy of continuous
improvement of its products without imposing upon itself any obligation to install them on products
previously manufactured. Due to late changes, it may have some differences between the manufactured
product and the descriptions and / or specifications in this document. Bombardier Inc. reserves the right
at any time to discontinue or change specifications, designs, features, models or equipment without
incurring obligation.
The illustrations in this document show the typical construction of the different assemblies and may not
reproduce the full detail or exact shape of the parts. However, they represent parts that have the same or
similar function.
The content of this bulletin is designed as a guideline only. All mechanics performing predelivery
procedures should have attended the current model year service training. Further information or
inquires should be directed to your distributor service representative and / or specific
Shop
Manual sections.
Please complete the Predelivery Check List for each snowmobile and return a customer signed
copy. Make sure the customer receives the
Operator’s Guide, Safety Handbook and video.
SUBJECT : Predelivery Procedures