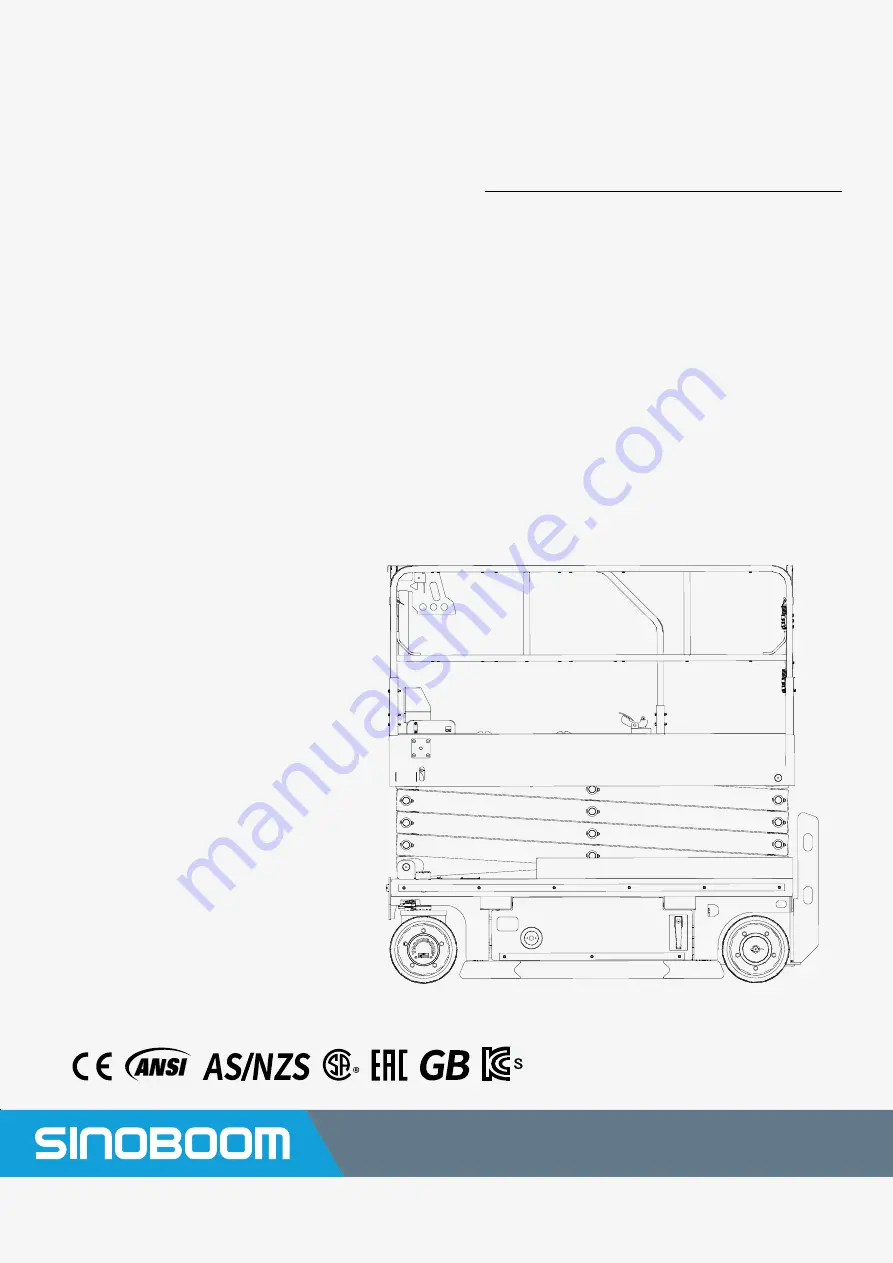
GTJZ0612E/0612E/2146E
GTJZ0812E/0812E/2746E
GTJZ1012E/1012E/3346E
GTJZ1212E/1212E/4047E
Maintenance
Manual
Part No.501048110002
Rev: A
Jul.2020
GTJZ
0608E (2132E)
GTJZ
0808E (2732E)
GTJZ
0808E (2732E)
GTJZ
0808E (2732E)
长沙市宁乡高新技术产业园区金洲大道东
128 号
0731-87116111 hr@sinoboom
. com. cn ww
w.sinoboom. com. cn
Always For B et t er A ccess Solution s
我们一直在追求新的高 度
尺寸:
210×285mm
20mm
20mm
产品说明书
PRODU
CT MAN
UAL
Summary of Contents for GTJZ0612E
Page 2: ......
Page 6: ...This Page Intentionally Left Blank...
Page 8: ...This Page Intentionally Left Blank...
Page 12: ...Jul 2020 iv GTJZ0612E 0812E 1012E 1212E Maintenance Manual This Page Intentionally Left Blank...
Page 86: ...Jul 2020 5 28 GTJZ0612E 0812E 1012E 1212E Maintenance Manual MAINTENANCE PROCEDURES...