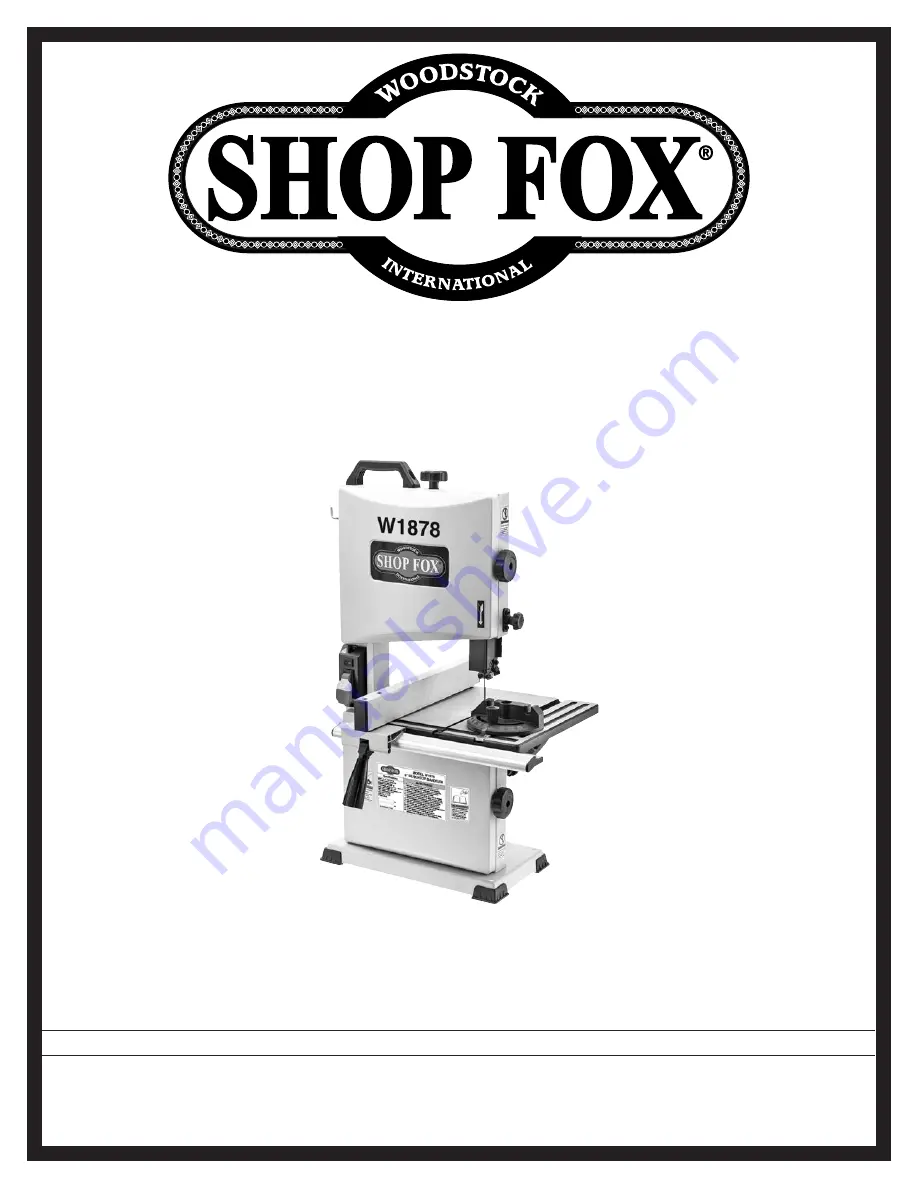
OWNER'S MANUAL
(FOR MODELS MANUFACTURED SINCE 4/21)
MODEL W1878
9" BENCHTOP BANDSAW
Phone: (360) 734-3482 • Online Technical Support: [email protected]
COPYRIGHT © MAY, 2021 BY WOODSTOCK INTERNATIONAL, INC.
WARNING: NO PORTION OF THIS MANUAL MAY BE REPRODUCED IN ANY SHAPE OR FORM WITHOUT
THE WRITTEN APPROVAL OF WOODSTOCK INTERNATIONAL, INC.
#21815MN Printed in China
Summary of Contents for W1878
Page 60: ......