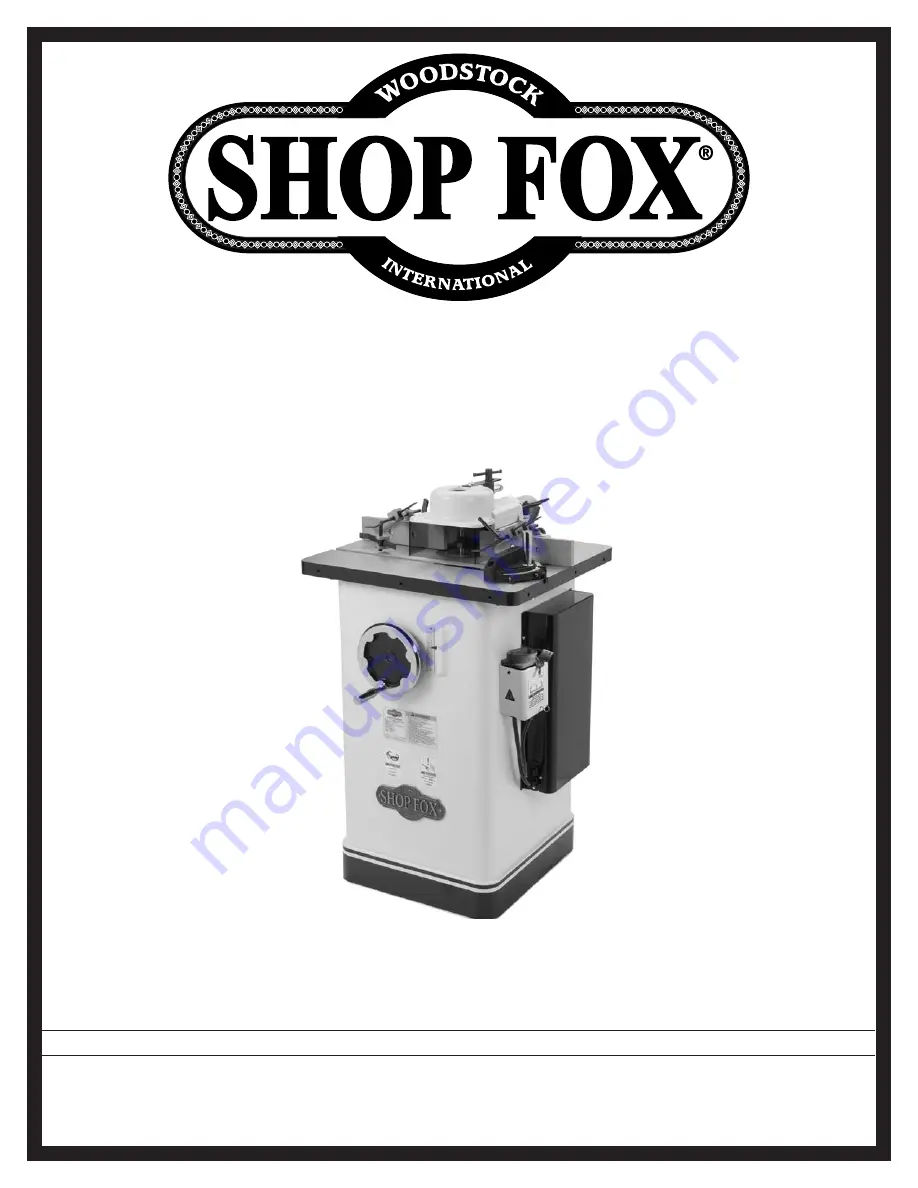
OWNER'S MANUAL
(FOR MODELS MANUFACTURED SINCE 9/10)
MODEL W1674
2 HP SHAPER
Phone: (360) 734-3482 • Online Technical Support: [email protected]
COPYRIGHT © FEBRUARY, 2004 BY WOODSTOCK INTERNATIONAL, INC., REVISED OCTOBER, 2010 (TR)
WARNING: NO PORTION OF THIS MANUAL MAY BE REPRODUCED IN ANY SHAPE OR FORM WITHOUT
THE WRITTEN APPROVAL OF WOODSTOCK INTERNATIONAL, INC.
Printed in Taiwan
#11875TS