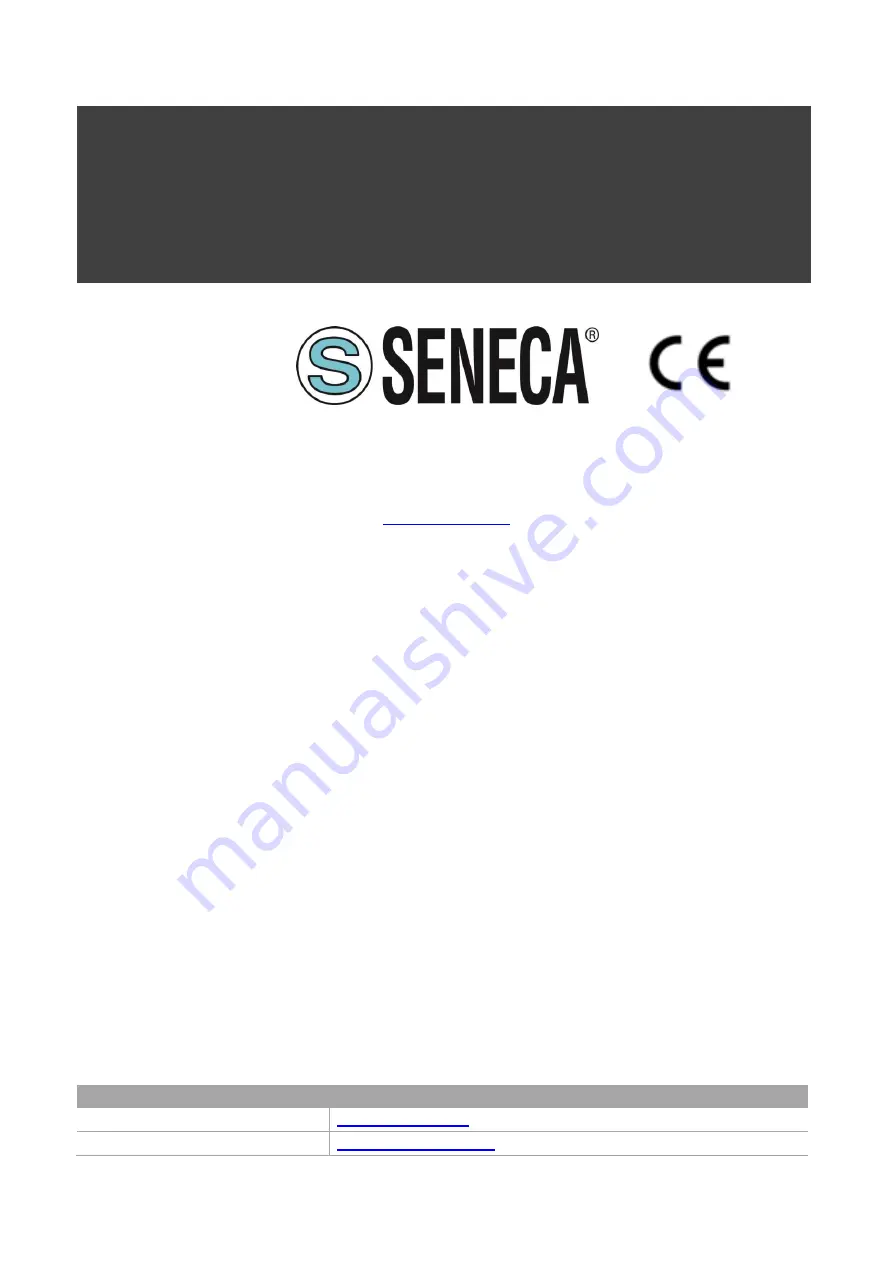
USER MANUAL
Z-KEY-P
MODBUS TO PROFINET IO GATEWAY
SENECA S.r.l.
Via Austria 26 – 35127 – Z.I. - PADOVA (PD) - ITALY
Tel. +39.049.8705355 – 8705355 Fax +39 049.8706287
Introduction
The content of this documentation refers to products and technologies described in it.
All technical data contained in the document may be changed without notice.
The content of this documentation is subject to periodic review.
To use the product safely and effectively, read the following instructions carefully before use.
The product must be used only for the use for which it was designed and manufactured: any other use is
under the full responsibility of the user.
Installation, programming and set-up are allowed only to authorized, physically and intellectually suitable
operators.
Set-up must be performed only after correct installation and the user must follow all the operations described
in the installation manual carefully.
Seneca is not responsible for failures, breakages and accidents caused by ignorance or failure to apply the
stated requirements.
Seneca is not responsible for any unauthorized modifications.
Seneca reserves the right to modify the device, for any commercial or construction requirement, without the
obligation to promptly update the reference manuals.
No liability for the contents of this document can be accepted.
Use the concepts, examples and other content at your own risk.
There may be errors and inaccuracies in this document that could damage your system, so proceed with
caution, the author(s) will not take responsibility for it.
Technical specifications are subject to change without notice.
CONTACT US
Technical support
Product information