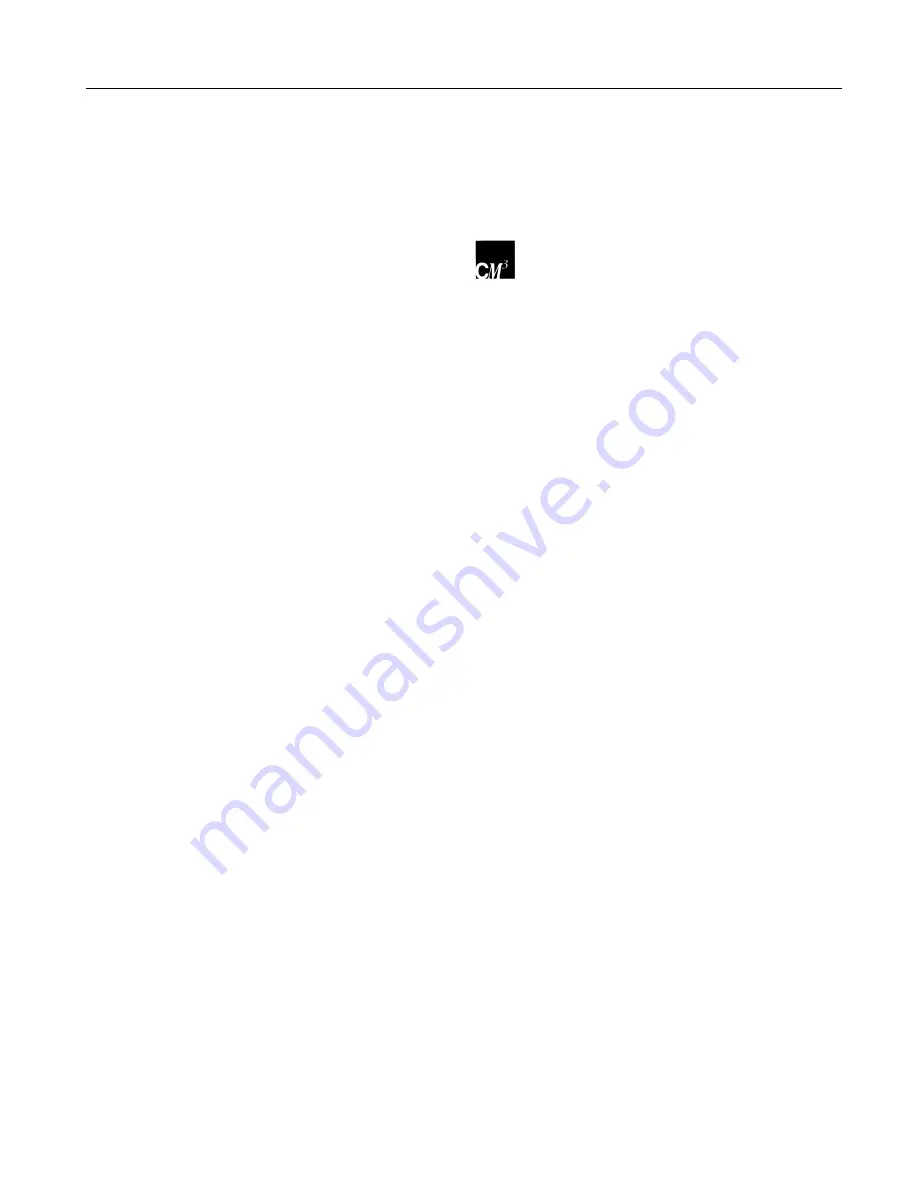
INTRODUCTION
This product manual contains the information
needed for the setup, installation, initial start up,
sanitation and maintenance of this ice machine.
Keep it for future reference.
Be certain that the information applies to the
model in question. If no model is listed, the
information applies to all models.
This manual is organized in the same way as the
expected use of the machine, it begins with
specifications, goes thru unpacking and setup,
shows where everything is; continues with initial
start up, then describes how it works. After that is
the sanitation section, followed by service diagnosis
and repair.
CME1056
May 2000
Page 1
TABLE OF CONTENTS
Specifications , , , , , , , , , , , , , PAGE 2
Air Cooled Layout , , , , , , , , , , , PAGE 3
Water Cooled Layout , , , , , , , , , PAGE 4
Pre-Installation , , , , , , , , , , , , , PAGE 5
Location & Assembly , , , , , , , , , PAGE 6
Cabinet Panel Removal: , , , , , , , , PAGE 7
Stacking: Requires Kit , , , , , , , , , PAGE 8
Stacking , , , , , , , , , , , , , , , , PAGE 9
Bin Thermostat: Installation , , , , , , PAGE 10
Plumbing - Air Cooled , , , , , , , , , PAGE 11
Plumbing - Water Cooled , , , , , , , PAGE 12
Electrical , , , , , , , , , , , , , , , , PAGE 13
After Utility Connections , , , , , , , , PAGE 14
Component Description and Function , PAGE 15
AutoIQ Controller , , , , , , , , , , , PAGE 16
How To Operate The Controller , , , , PAGE 17
Initial Start Up , , , , , , , , , , , , , PAGE 18
Adjustments , , , , , , , , , , , , , , PAGE 19
How This Machine Works , , , , , , , PAGE 20
How This Machine Works , , , , , , , PAGE 21
Technicians Only: Freeze Cycle Operational
Sequence , , , , , , , , , , , , , , , PAGE 22
Technicians Only: Harvest Cycle Operational
Sequence , , , , , , , , , , , , , , , PAGE 23
Sanitation and Cleaning , , , , , , , , PAGE 24
Additional Maintenance , , , , , , , , PAGE 25
Additional Maintenance: Ice Sensors and Water
Level Sensor , , , , , , , , , , , , , , PAGE 26
Additional Maintenance: Air Filter Replacement
, , , , , , , , , , , , , , , , , , , , , PAGE 27
Additional Maintenance: Condenser , , PAGE 28
Service Diagnosis: Controller Diagnostic Light
Analysis , , , , , , , , , , , , , , , , PAGE 29
Service Diagnosis , , , , , , , , , , , PAGE 30
Service Diagnosis: Components, , , , PAGE 31
PTCR Diagnosis , , , , , , , , , , , , PAGE 32
Operational Characteristics:
CME1056
PAGE 33
Removal and Replacement: Water Level Sensor
, , , , , , , , , , , , , , , , , , , , , PAGE 34
Removal and Replacement: Fan Blade and/or Fan
Motor, , , , , , , , , , , , , , , , , , PAGE 35
Access Valves , , , , , , , , , , , , , PAGE 36
Before Calling for Service , , , , , , , PAGE 37
Parts Lists and Wiring Diagrams are Located in the Center of this Manual
™
CM Cubed™ Cuber Performance Raised
to a Higher Power.™