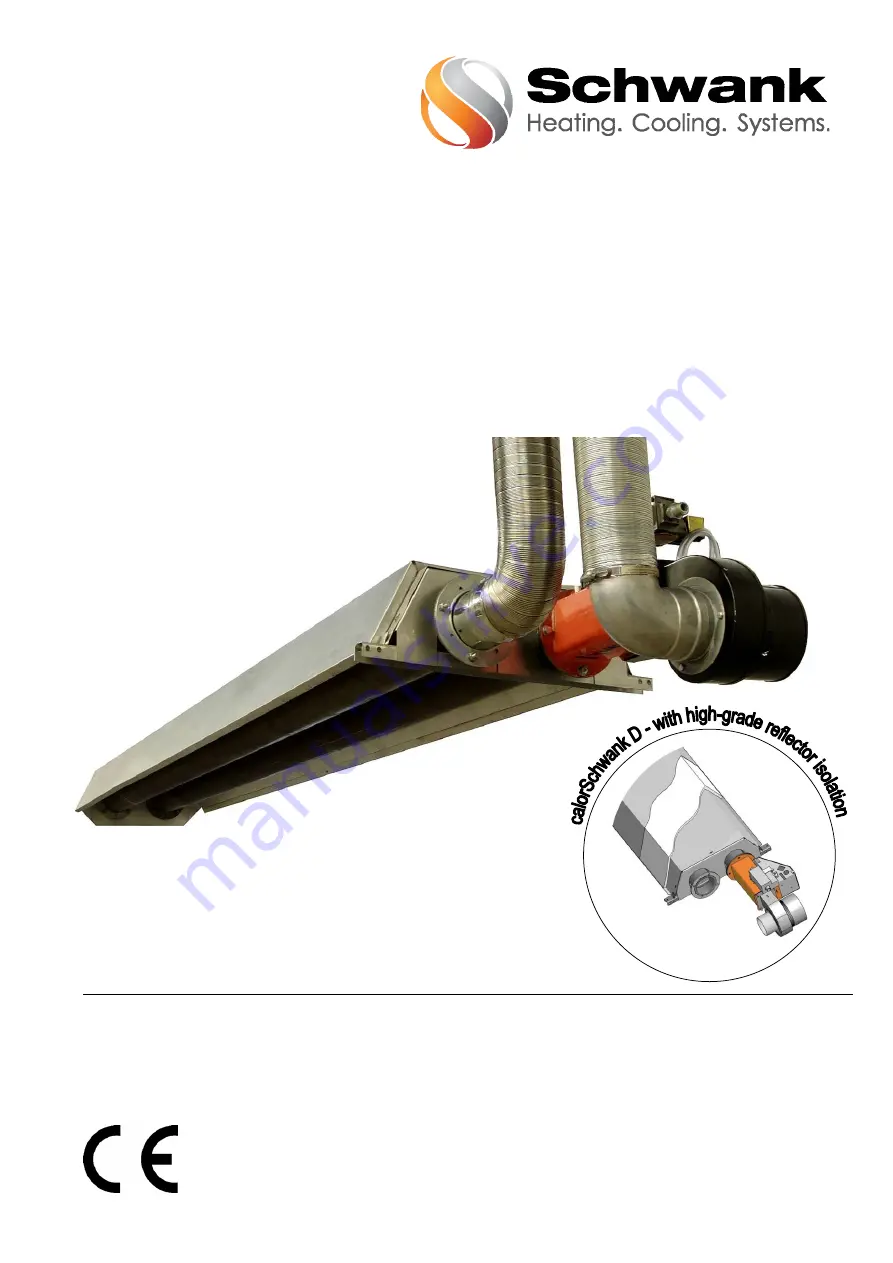
infraSchwank D / calorSchwank D
Radiant Tube Heater
15 U / 20 U / 30 U / 40 U / 50 U / 60 U
1-stage / modulating lambdaPlus
single heater and flue gas collection system [herringbone] type F
Technical Manual
Technical Instructions
Operating Instructions
Legal Requirements
Assembly Instructions
Installation Instructions
Commissioning
Service Guide
0085BO0037
Version
021
infr
a D U-Form
16
/19
Techni
sche
Ä
nd
eru
ngen
vorbeha
lten