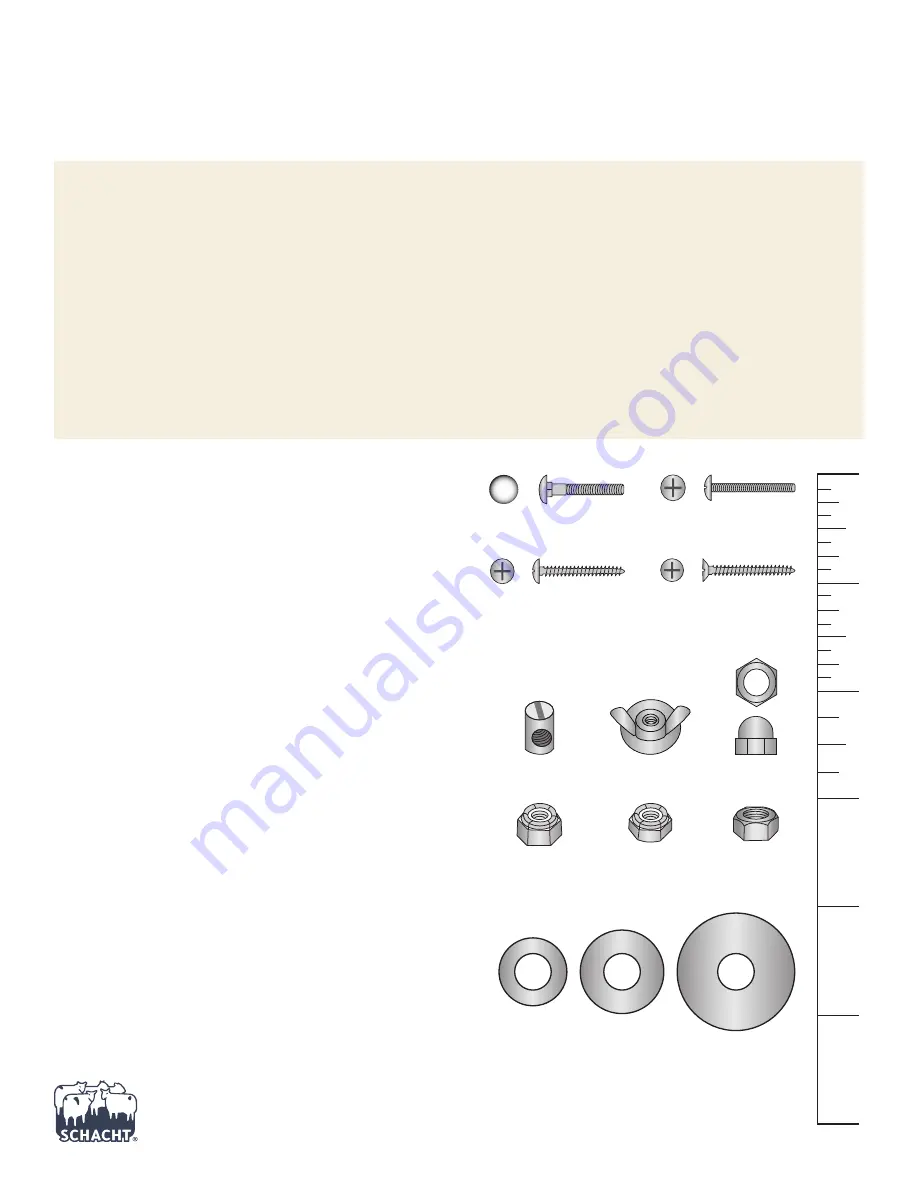
- 1 -
MIGHTY WOLF LOOM
TM
A
ssembly
I
nstructIons
for
D
IsAssembleD
l
ooms
FL3002E
FL3004E
FL3012E
FL3014E
FL3022E
FL3024E
02.20
Find out more at
schachtspindle.com
Schacht Spindle Company 6101 Ben Place Boulder, CO 80301
p. 303.442.3212 f. 303.447.9273
© 2020 Schacht Spindle Company, Inc.
0
1
2
3
4
5
6
TOOLS REQUIRED
#2 Phillips screwdriver
slotted (flat) screwdriver
adjustable wrench or wrenches in the following sizes:
5/16", 7/16", 3/8", 1/2"
COMMON HARDWARE
These drawings are not to scale and hardware is not shown in
every size listed.
■
Screws and bolts
are sized in inches, measured by
shaft
length
. Measure the shafts of screws and bolts with a metal tape
measure or the ruler on this page. First identify all the screws and
bolts in a bag; then it will be easier to identify any nuts.
■
Nuts
attach to bolts and machine screws. They have to match
the bolt or machine screw in
diameter
and
thread size
. Match
the numbers at the beginning of the description (for instance, 10-
24 or 1/4-20) to the corresponding bolt or machine screw.
■
Washer
sizes refer to the
diameter of the hole
; measure the
hole with a metal tape measure or the ruler on this page. Different
types of washers, all the same size, are shown at right. SAE
washers have the smallest outside diameter, fender washers have
the largest outside diameter, and USS washers are in the middle.
For more help identifying hardware, see our guide at
www.schachtspindle.com/pdfs/schacht-hardware-guide.
pdf.
barrel nut
washer wing nut
cap nut
hex nut
slim lock nut
lock nut
IDENTIFYING NUTS
SAE washer
USS washer
fender washer
IDENTIFYING WASHERS
IDENTIFYING SCREWS AND BOLTS
carriage bolt
Phillips truss head
machine screw
Phillips pan head
sheet metal screw
Phillips truss head
sheet metal screw
BEFORE YOU BEGIN
■
Read through the directions before starting to assemble your
loom.
■
You’ll find a complete labelled diagram of the Wolf loom in your
Maintenance and Warranty manual and at schachtspindle.com.
■
Wolf loom legs are called out by where they cross each other.
The legs that touch the ground at the front of the loom are called
“inside” legs because they are covered by the “outside” legs when
they cross at the loom center.
■
The beater is at the front of the loom. The brake is on the right
side of loom.
■
All wooden parts of the loom have been finely sanded and
finished with hand-rubbed Danish oil. If at any time you wish
to apply more finish to the loom, use a Danish oil (tung oil and
polyurethane mixture) and hand-rub the wood with a soft lint-free
cloth.
Be sure to follow the finish manufacturer’s instructions.
■
Unpack the loom parts carefully and compare them to the
drawings on pages 4 and 5. Do not throw away the carton or any of
the packing material until you have checked to see that all of the
parts and hardware bags have been included.
■
Hardware for your loom has been packed into bags for different
steps in the assembly process.
Open each bag only when you
reach those steps, then identify the pieces included in that bag.
■
Follow the exact order of assembly. Take care and work slowly. It
will be easier to assemble your loom with a helper. Some steps may
require two people.
■
When you finish assembling the loom, go back over all of the
screws and bolts to make sure they are tight. For screws on parts
that need to pivot, tighten the screw firmly, then unscrew just
enough to allow free movement. It is a good idea to re-tighten all
screws on your loom every few months.