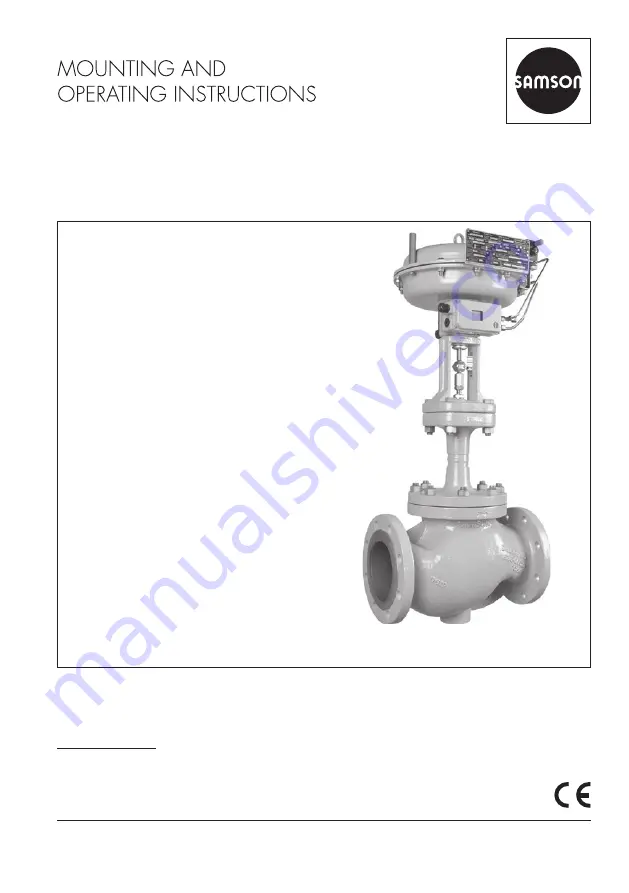
Translation of original instructions
EB 8020-1 EN
Edition February 2020
Type 3241-1-Gas and Type 3241-7-Gas
Automatic Shut-off Valves for Gases
Valve class D
and valve class E
Type 3241‑7‑Gas with Type 3963 Solenoid Valve and Type 3730 Positioner
NOTICE on the scope of this document
These mounting and operating instructions
only apply to valves already in use.
For control valves of the valve class D, refer
to the updated mounting and operating
instructions
u
They can be downloaded from our website
at
u
Summary of Contents for 3241-1-Gas
Page 11: ...EB 8020 1 EN 11...
Page 15: ...EB 8020 1 EN 15...
Page 42: ...42 EB 8020 1 EN Servicing Tools See document u AB 0100 for details on suitable tools...
Page 49: ...EB 8020 1 EN 49...
Page 50: ...50 EB 8020 1 EN...
Page 51: ...EB 8020 1 EN 51...
Page 52: ...52 EB 8020 1 EN...
Page 55: ...EB 8020 1 EN 55...