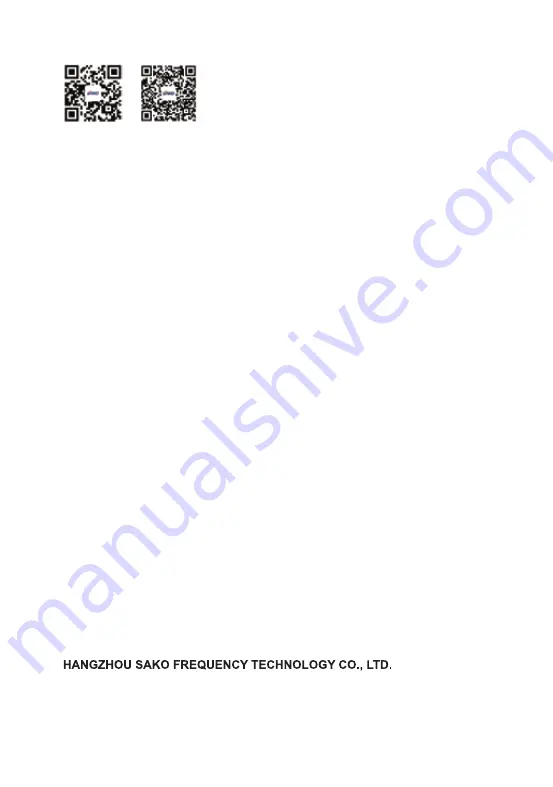
V1.0
SKI600
High-performance
Vector Inverter
Please read this manual carefully before use and keep it for future reference
MANUAL
Add: No. 5, Yaojia Road, Yuhang District, Hangzhou, Zhejiang, China
Tel: 0086-571-88183319
Email: [email protected]
8FDIBU
8FCTJUF
Summary of Contents for SKI600
Page 3: ......
Page 4: ...88888 Operating Instruction Manual High performance Vector Inverter ...
Page 179: ......
Page 180: ......