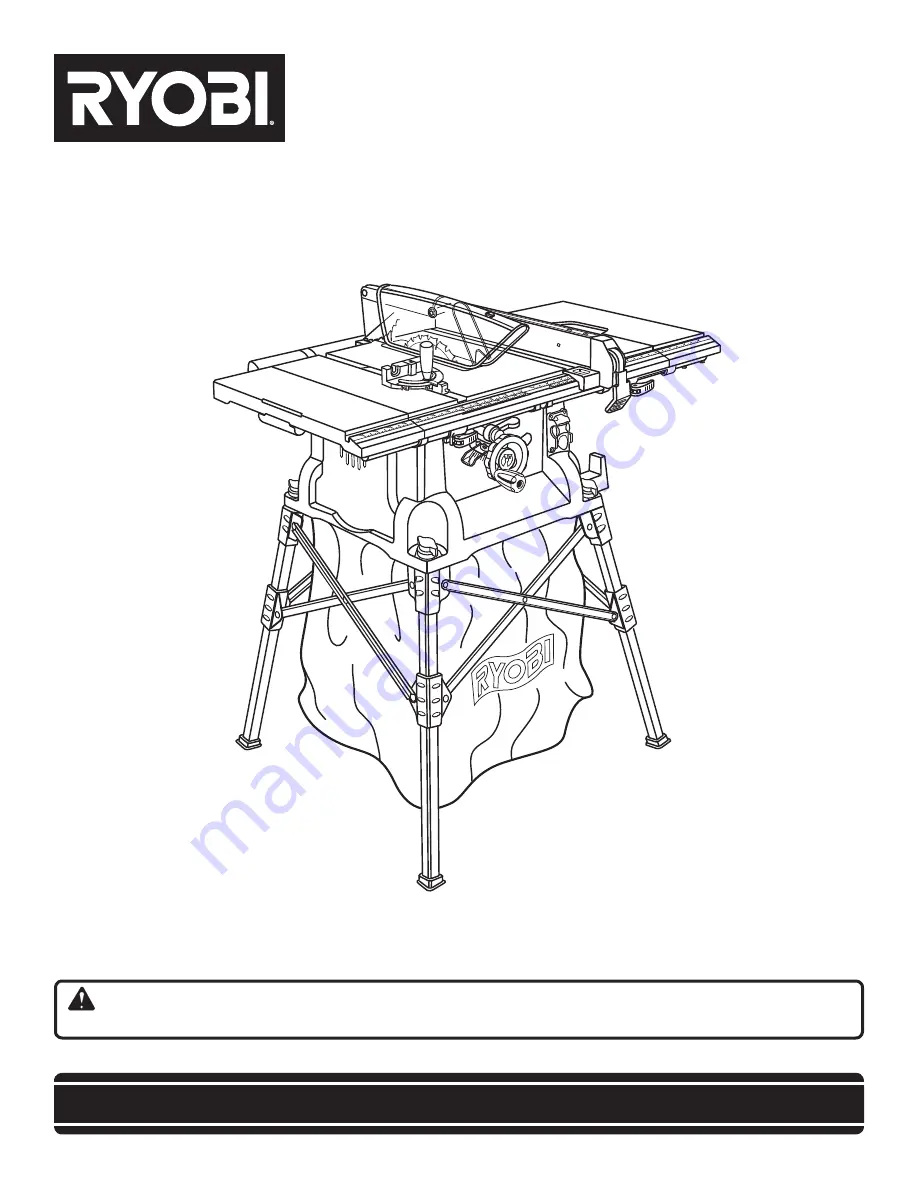
OPERATOR’S MANUAL
10 in. TAbLE SAw
bTS16
SAVE THIS MANUAL FOR FUTURE REFERENCE
You
r table saw h
as been engineered and manufactured to our high standard for dependability, ease of operation, and
operator safety. When properly cared for, it will give you years of rugged, trouble-free performance.
wARNING:
To reduce the risk of injury, the user must read and understand the operator's manual before using
this product.
Thank you for your purchase.