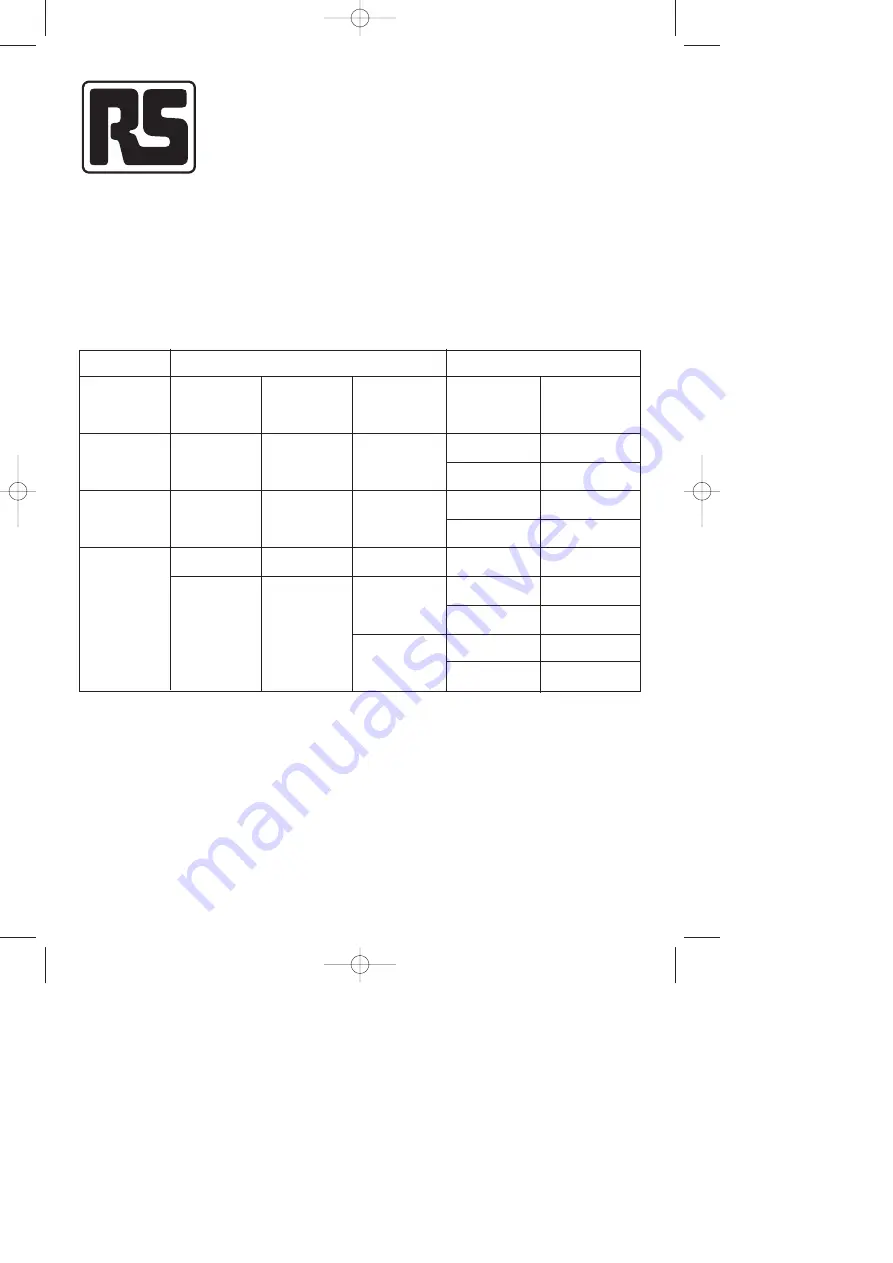
1
5.25" Floppy Disk Drive
Stock No. 237-088
1.0
Introduction
1.1
General description
This drive is a high-density, dual speed, double-sided 5.25" mini-floppy disk drive.
The speed is controlled by Pin #2 of the interface connector. Normally, when this pin
is at logical low, the transfer rate is low and when at logical high, the transfer rate is
high. This drive can be used as a high-density 1.6Mb drive. When at logical low,
this drive can be used as a standard 1.0Mb drive.
Table 1-1. Compatibility with other model drives
Read by this drive
Double-sided
48 t.p.i.
Double-sided
96 t.p.i.
Dual-speed
0.5Mb
1.0Mb
1.6Mb
1.0Mb
300 r.p.m.
300 r.p.m.
300 r.p.m.
360 r.p.m.
MD
MD
HD
MD
FDD used
Diskette
Capacity
360 r.p.m.
300 r.p.m.
360 r.p.m.
300 r.p.m.
360 r.p.m.
360 r.p.m.
360 r.p.m.
300 r.p.m.
360 r.p.m.
360 r.p.m.
Rotational
speed
Rotational
speed
Transfer rate
300Kbits/sec
250Kbits/sec
300Kbits/sec
250Kbits/sec
500Kbits/sec
300Kbits/sec
250Kbits/sec
300Kbits/sec
250Kbits/sec
Diskette written
Leaflet No. 9419 26/4/97 6:09 pm Page 1