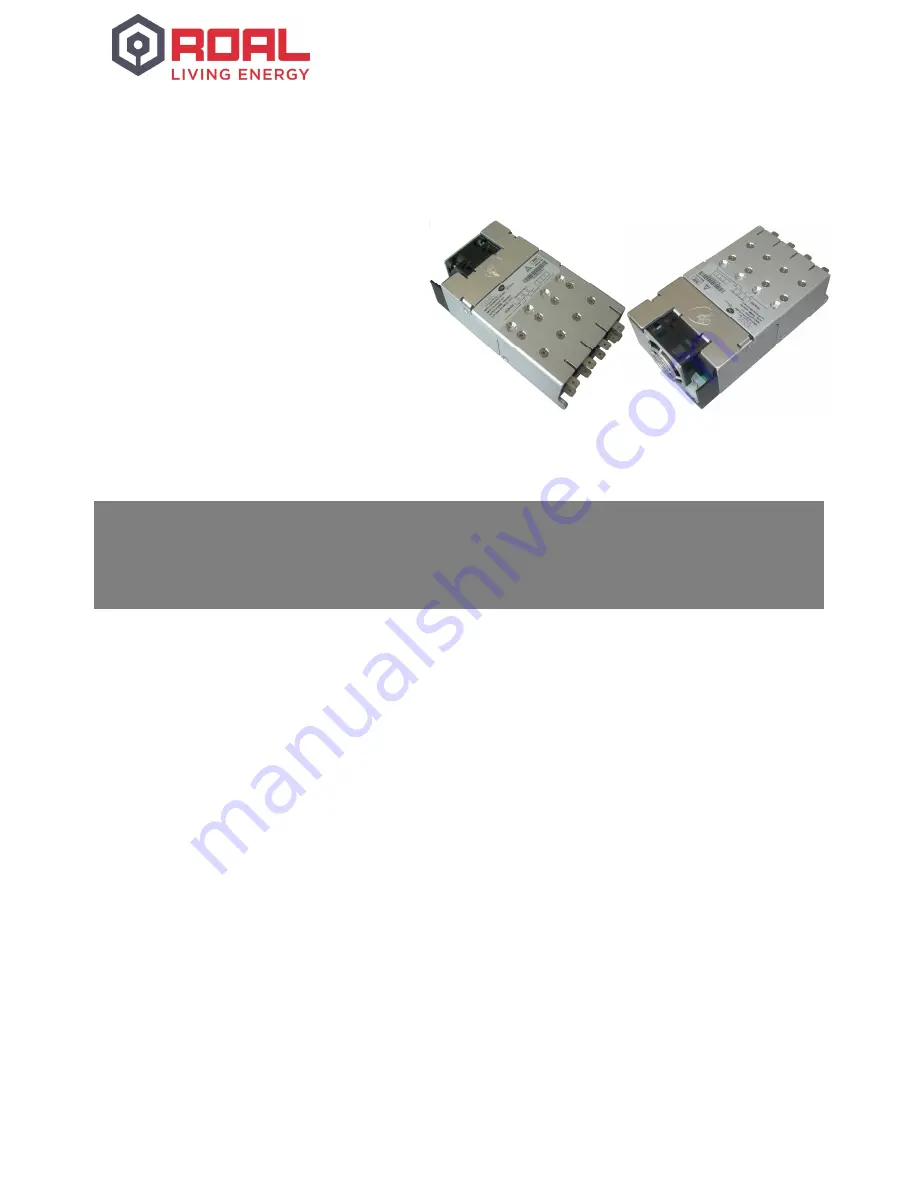
The RCB and MCB series user manual has been prepared
by the Roal Electronics design team to assist qualified engineers
in correctly implementing the products and to achieve the best reliability and performance.
At time of print, the information contained in this document is believed to be correct and accurate. However, specifications are subject to change
without prior notice and Roal Electronics will not be liable for any damage caused as a result of the information within this document. For
continued product improvement, please report any errors contained in the document to Roal Electronics SpA.
RCB600 and MCB600 series overview
The RCB600 and MCB600 switch mode power supply series offers truly unrivalled power density, providing 600 W at 25 W/in
3
in a 5” x 3”x 1U package. They are the ultimate power solutions for system designers as they address the pressing demands
for more power within less space. Providing multiple isolated outputs, the series carry full UL60601 (MCB600) and UL60950 2
nd
edition (RCB600) safety approvals.
The basic system consists of an input module together with up to four fully isolated output modules, all supplied with advanced
remote voltage and current programming functionality as standard.
The input module delivers up to 600 W of output power and has 4 slots, each capable of separately delivering up to 150 W. A
5 V, 200 mA medically isolated bias supply together with an AC mains signal (AC_OK) and a global inhibit signal (GINH) that
can disable all outputs simultaneously, comes as standard on all models.
A built in fan, which speed is automatically controlled, ensures the unit proper cooling in any operating condition maintaining
at minimum fan RPM and, in turn, acoustic noise.
Output modules are currently available in single output types with models covering voltage ranges from 1.5 V to 58 V and
currents up to 25 A. All outputs can be connected in parallel or in a series resulting in a voltage range of up to 232 V and a
maximum current of up to 100 A from a single chassis.
By selecting the correct output modules, a custom power solution can be configured in a few minutes. This instantly available
custom solution offers industry leading power density, total system efficiencies of up to 89% and suits all types of applications
including industrial, medical, aerospace, military and telecoms.
RCB600, MCB600
User Manual
RCB600
AND
MCB600
S
ERIES
O
VERVIEW