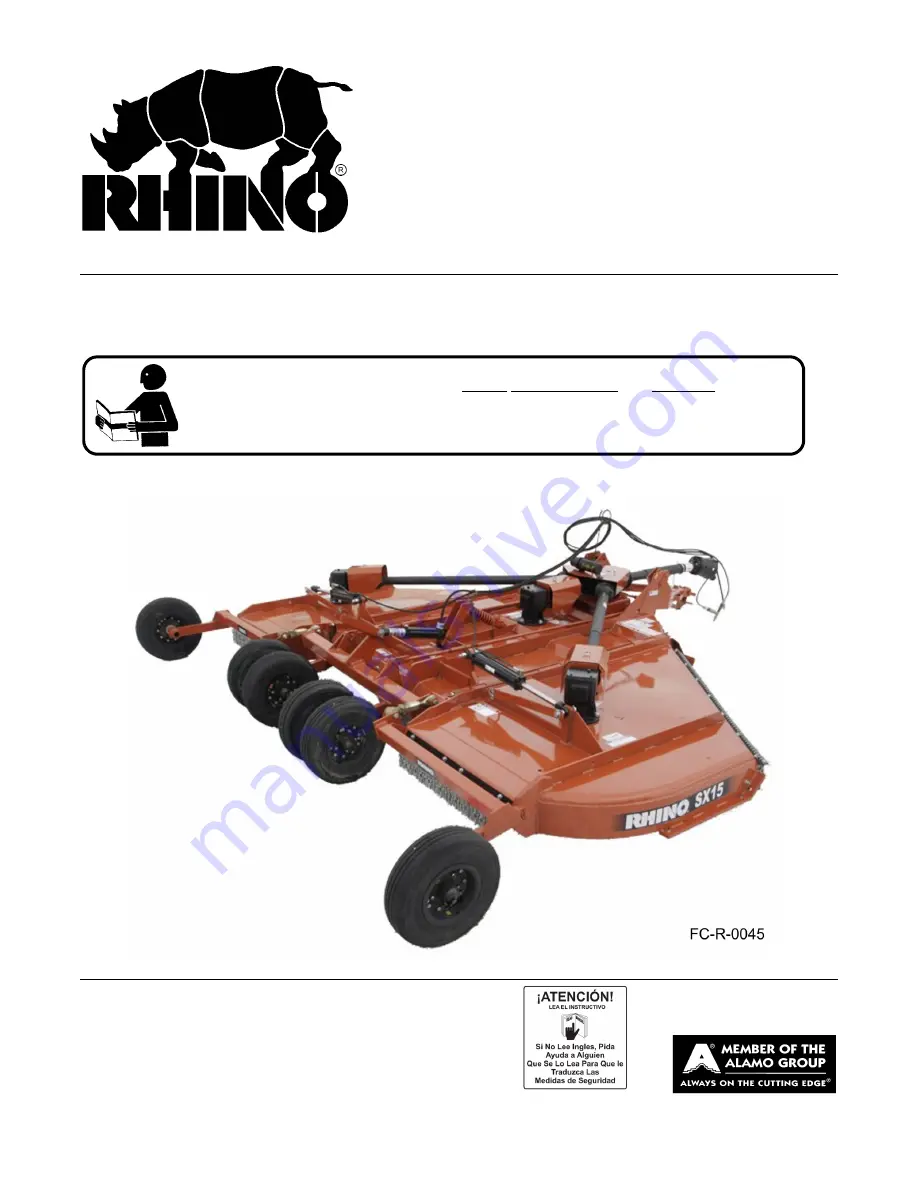
©2009 Alamo Group Inc.
SX15
Published 01/09
Part NO. 00786228C
OPERATOR’S MANUAL
RHINO
®
1020 S. Sangamon Ave.
Gibson City, IL 60936
800-446-5158
Email: [email protected]
FLEX-WING MECHANICAL LEVEL
LIFT ROTARY MOWER
This Operator's Manual is an integral part of the safe operation of this machine and must
be maintained with the unit at all times. READ, UNDERSTAND, and FOLLOW the Safety
and Operation Instructions contained in this manual before operating the equipment.
C01-
Cover
$0.00
Summary of Contents for SX15
Page 7: ...Safety Section 1 1 2009 Alamo Group Inc SAFETY SECTION ...
Page 35: ......
Page 36: ......
Page 37: ......
Page 38: ......
Page 39: ......
Page 40: ......
Page 41: ......
Page 42: ......
Page 43: ......
Page 44: ......
Page 45: ......
Page 46: ......
Page 47: ......
Page 48: ......
Page 49: ......
Page 50: ......
Page 51: ......
Page 52: ......
Page 53: ......
Page 54: ......
Page 55: ......
Page 56: ......
Page 57: ......
Page 58: ......
Page 59: ......
Page 60: ......
Page 61: ......
Page 62: ......
Page 63: ......
Page 64: ......
Page 65: ......
Page 66: ......
Page 67: ......
Page 68: ......
Page 69: ......
Page 70: ......
Page 71: ......
Page 72: ......
Page 73: ......
Page 74: ......
Page 75: ......
Page 76: ......
Page 77: ......
Page 78: ......
Page 79: ...Introduction Section 2 1 2009 Alamo Group Inc INTRODUCTION SECTION ...
Page 83: ...Assembly Section 3 1 2009 Alamo Group Inc ASSEMBLY SECTION ...
Page 92: ......
Page 93: ...Operation Section 4 1 2009 Alamo Group Inc OPERATION SECTION ...
Page 140: ......
Page 141: ...Maintenance Section 5 1 2009 Alamo Group Inc MAINTENANCE SECTION ...
Page 157: ......
Page 160: ...SX15 SOM 01 09 P N 00786228C Printed U S A SX15 FLEX WING MECHANICAL LEVEL LIFT ROTARY MOWER ...