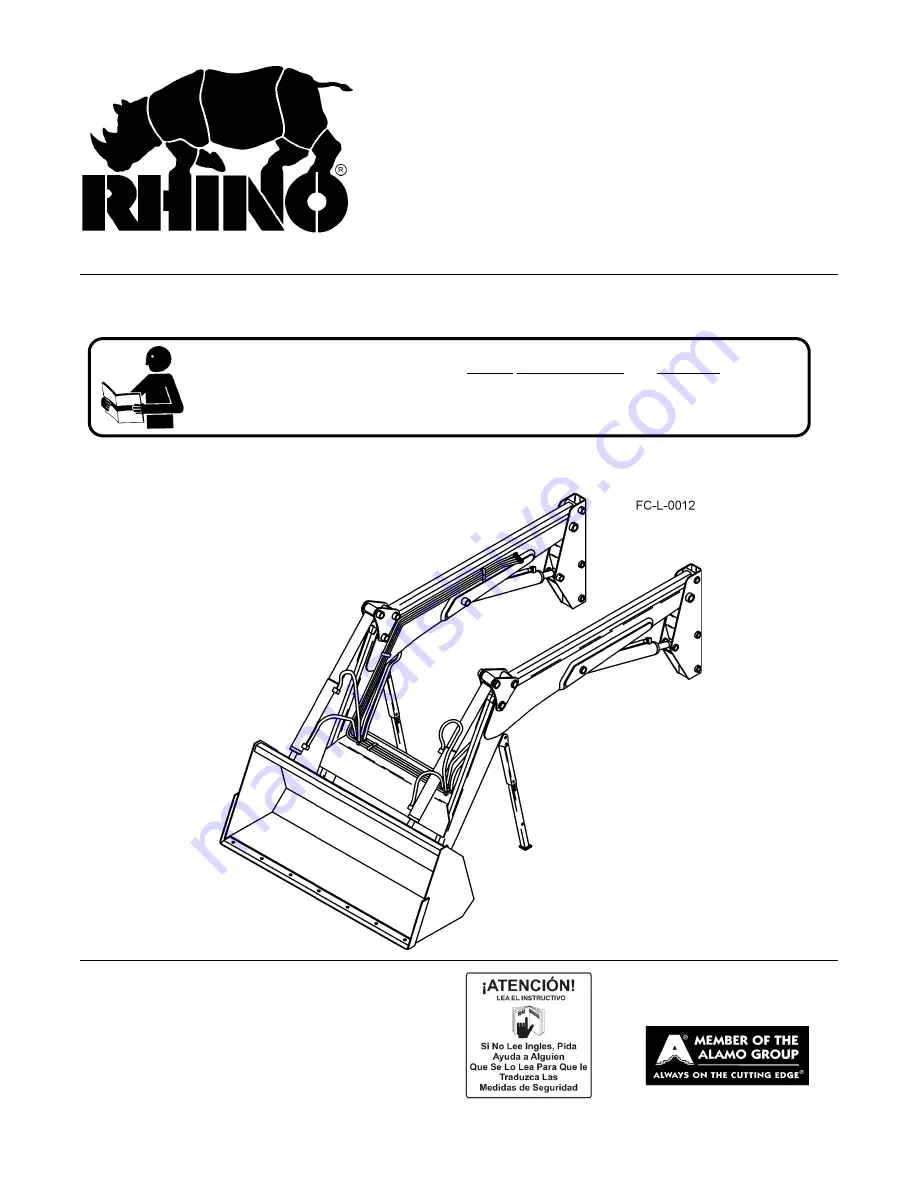
© 2011 Alamo Group Inc.
$0.00
4211 MSL
Published 01/11
Part No.
F-3735C
OPERATOR’S MANUAL
RHINO
®
1020 S. Sangamon Ave.
Gibson City, IL 60936
800-446-5158
Email: [email protected]
LOADER
This Operator's Manual is an integral part of the safe operation of this machine and must
be maintained with the unit at all times. READ, UNDERSTAND, and FOLLOW the Safety
and Operation Instructions contained in this manual before operating the equipment.
C01-
Cover
Summary of Contents for LOADER 4211 MSL
Page 5: ...Safety Section 1 1 SAFETY SECTION...
Page 28: ......
Page 29: ...Introduction Section 2 1 INTRODUCTION SECTION...
Page 34: ......
Page 35: ...Assembly Section 3 1 ASSEMBLY AND CONNECTING THE LOADER SECTION...
Page 46: ......
Page 47: ...Operation Section 4 1 OPERATION SECTION...
Page 90: ......
Page 91: ...Maintenance Section 5 1 MAINTENANCE SECTION...
Page 100: ...MAINTENANCE 4211 4211SS MSL 01 11 Maintenance Section 5 10 2011 Alamo Group Inc MAINTENANCE...
Page 101: ...MAINTENANCE 4211 4211SS MSL 01 11 Maintenance Section 5 11 2011 Alamo Group Inc MAINTENANCE...
Page 104: ...4211MSL 4211SS MSL SOM 01 11 P N F 3735C Printed U S A 4211 MSL 4211SS MSL LOADER...