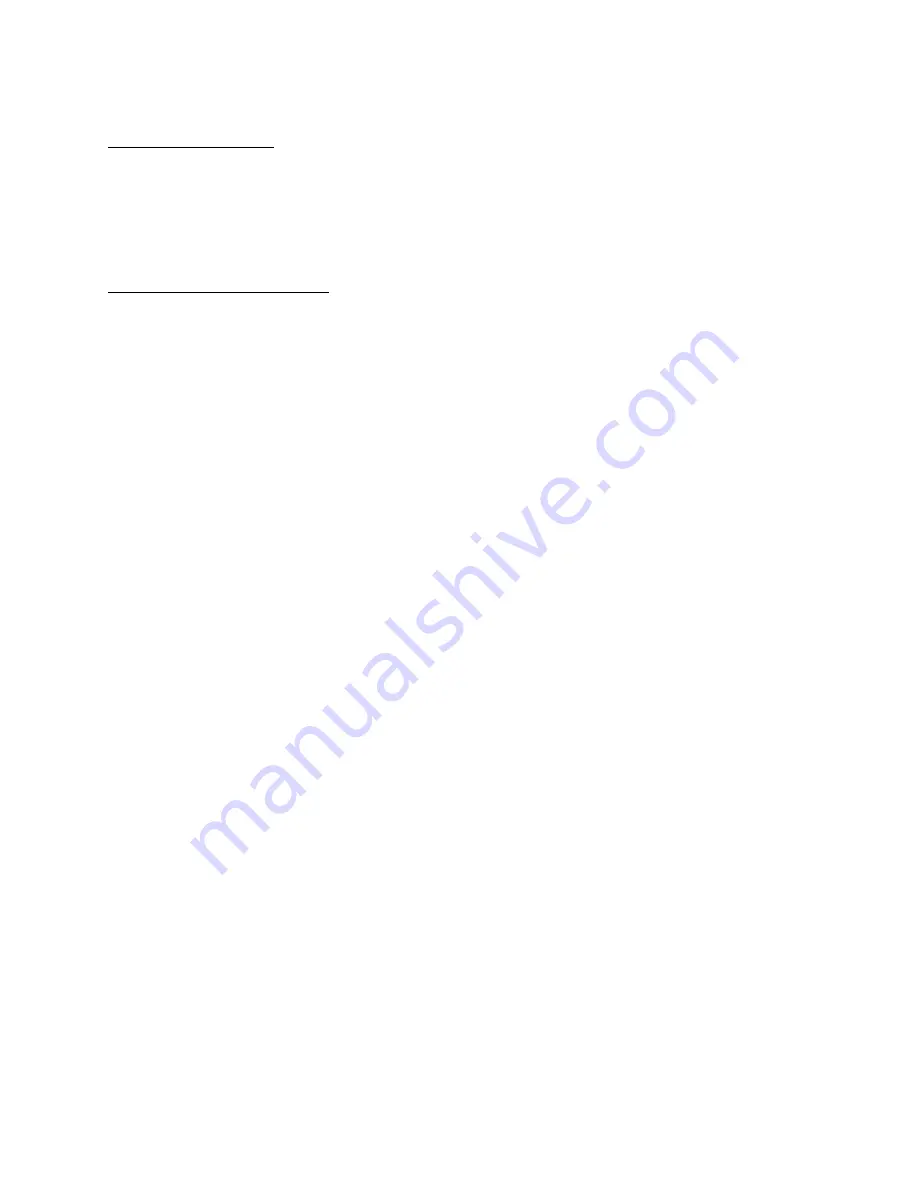
P/N: MG-511 (Printed Instruction Manual)
Note: This page is not to be included as part of printed hard copy.
Overall Specifications:
Material: white plain paper
Printed text: black
Binder: staple upper left corner
Individual page specifications:
Cover page: printed single-side up
Warranty page: printed single-side down (facing out as last page of manual)
The balance of instruction manual pages to be printed utilizing both front and back side of paper.