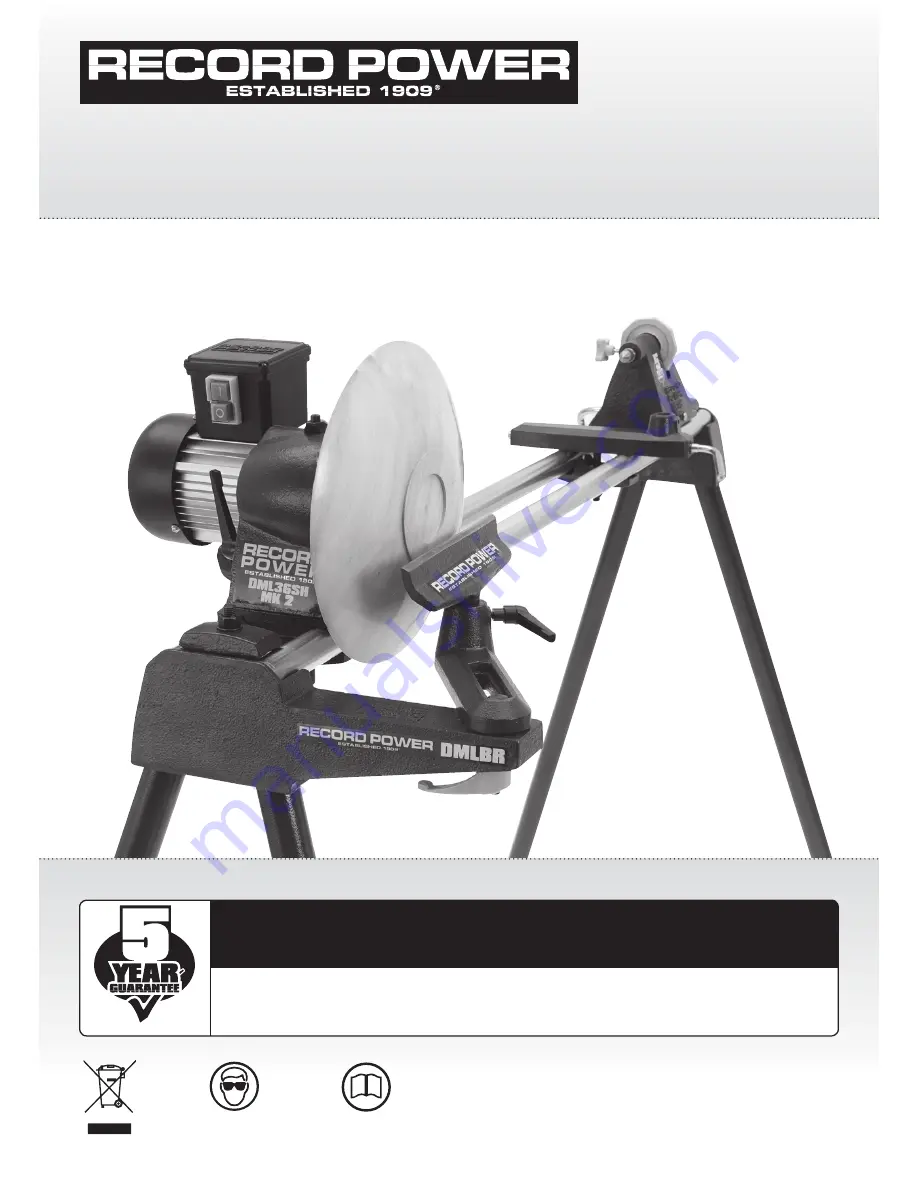
1
Original Instruction Manual
DML36SH-CAM
Swivel Head 4 Speed Intermediate Lathe
Important
For your safety read instructions carefully before
assembling or using this product.
Save this manual for future reference.
Always wear safety glasses when
using woodworking equipment.
Always read the instructions
provided before using
woodworking equipment.
i
Kg
Version 2.0
October 2012
To register this product please visit
www.recordpower.info
It is important to register your product as soon as possible in order to receive efficient after sales
support and be entitled to the full
5 year guarantee
. Your statutory rights are not affected.
Please see back cover for contact details.