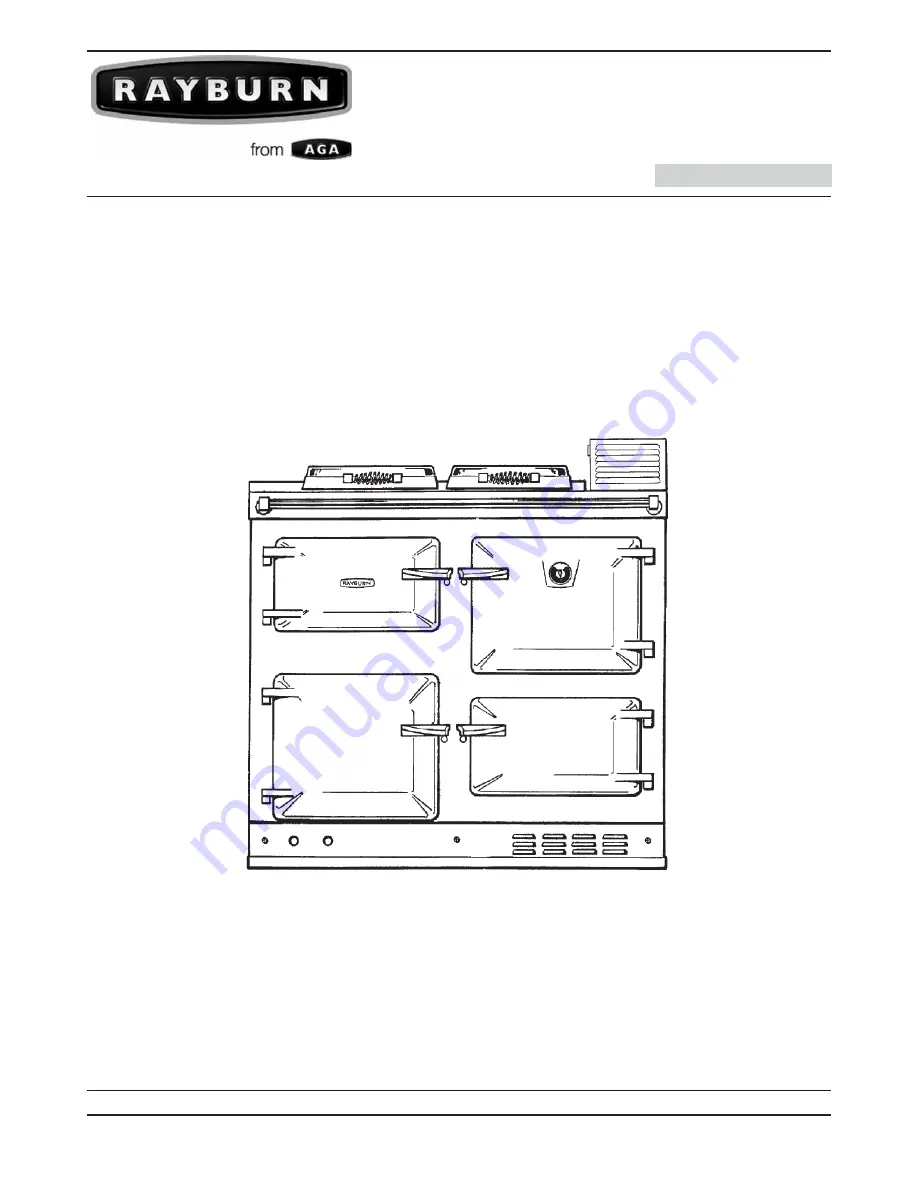
12/13 EINS 511641-E
For use in GB and IE
Installation
Instructions
Heatranger 440/460/480/499KB
DESN 511653 B
PLEASE READ THESE INSTRUCTIONS BEFORE INSTALLING THIS APPLIANCE
REMEMBER, when replacing a part on this appliance, use only spare parts that you can be assured conform to the safety
and performance specification that we require. Do not use reconditioned or copy parts that have not been clearly
authorised by AGA.
Summary of Contents for Heatranger 440
Page 14: ...Site requirements 440 460 480 499KB EXTERNAL CONTROLS 14 ...
Page 16: ...16 Site requirements Fig 7 WIRING DIAGRAM 440 460 480 499 KB ...
Page 19: ...Installation requirements Fig 12 19 ...
Page 25: ...Sealed System 25 Fig 21 ...
Page 41: ...41 ...
Page 42: ...42 ...
Page 43: ...43 ...