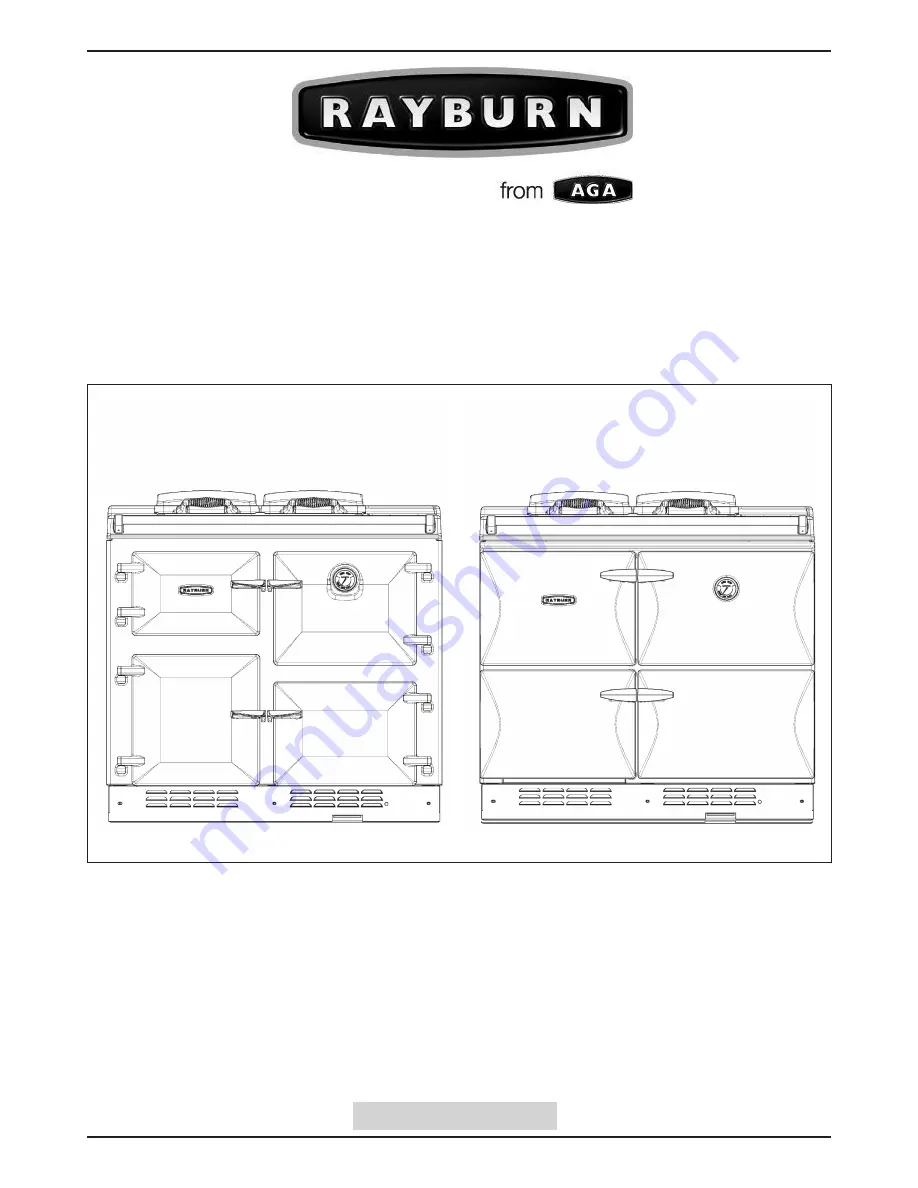
12/15 EINS 515872
PLEASE READ THESE INSTRUCTIONS BEFORE SERVICING THIS APPLIANCE
Servicing
Instructions
For use in GB & IE
REMEMBER, when replacing a part on this appliance, use only spare parts that you can be assured conform to the
safety and performance specification that we require. Do not use reconditioned or copy parts that have not been clearly
authorised by AGA.
680KCD
780KCD
DESN 515906
DESN 516830
Summary of Contents for 680KCD
Page 8: ...Cleaning 8 Fig 7 ALL BAFFLES MUST BE STACKED IN PLACE AS DIAGRAM ABOVE ...
Page 21: ...21 Fig 33 DESN 514774 Replacement of parts Electrical controls ...
Page 29: ...Fault Finding Fig 37A 29 DESN 516838 ...
Page 30: ...30 Fault Finding ...
Page 31: ...31 Fault Finding ...
Page 33: ...33 ...
Page 34: ...34 ...
Page 35: ...35 ...