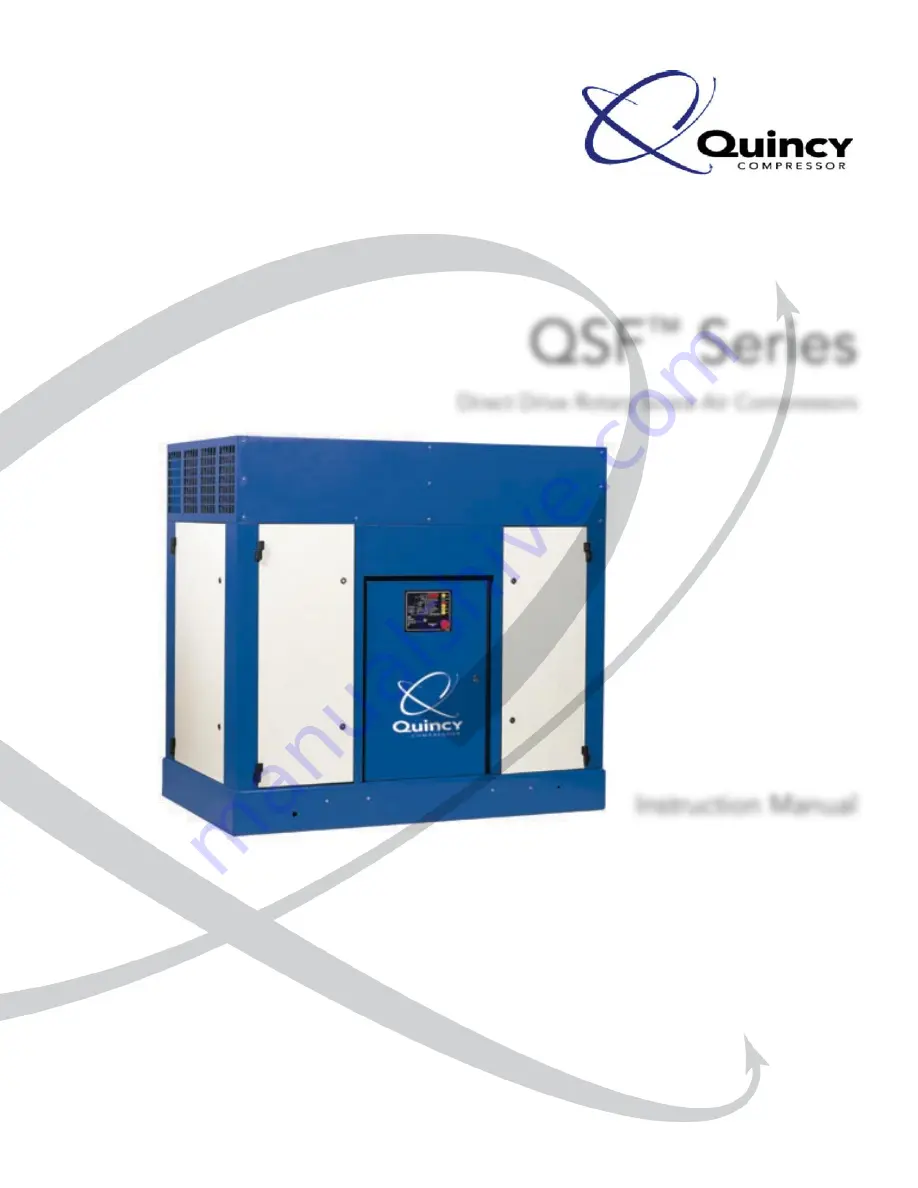
QSF
™
Series
Direct Drive Rotary Screw Air Compressors
Instruction Manual
This manual contains important safety information and should be made available to
all personnel who operate and/or maintain this product. Carefully read this manual
before attempting to operate or perform maintenance on this equipment.
Manual No. 55002-CB
October 1998 Editio
n
Updated: Septermber 2010
Summary of Contents for QSF Series
Page 2: ......
Page 26: ...Section I V Operating Procedures Quincy Compressor QSF Series 22...
Page 30: ...Section V Servicing Quincy Compressor QSF Series 26...
Page 55: ......