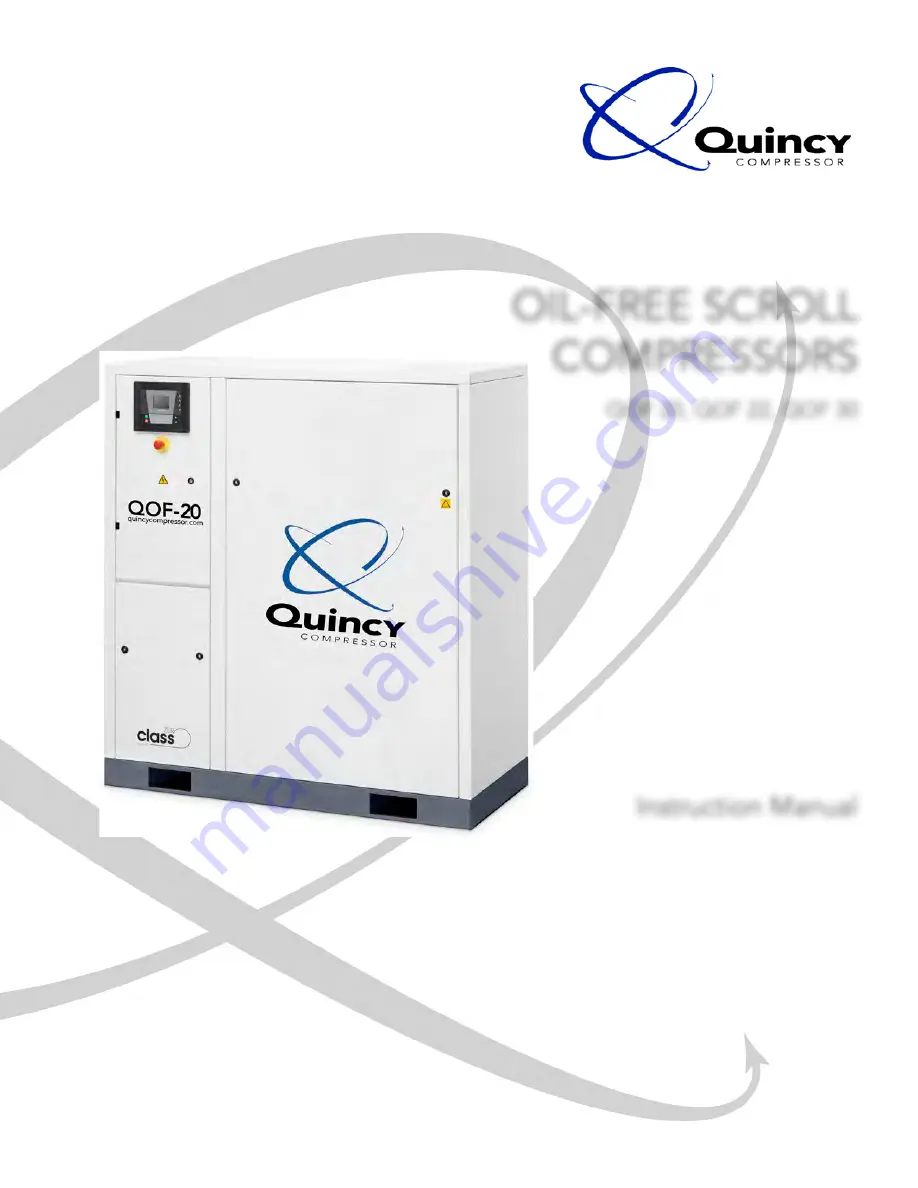
OIL-FREE SCROLL
COMPRESSORS
QOF 20, QOF 22, QOF 30
Instruction Manual
This manual contains important safety information and should be made available to
all personnel who operate and/or maintain this product. Carefully read this manual
before attempting to operate or perform maintenance on this equipment.
Manual No.
2930 7140 30
November 2014 Edition