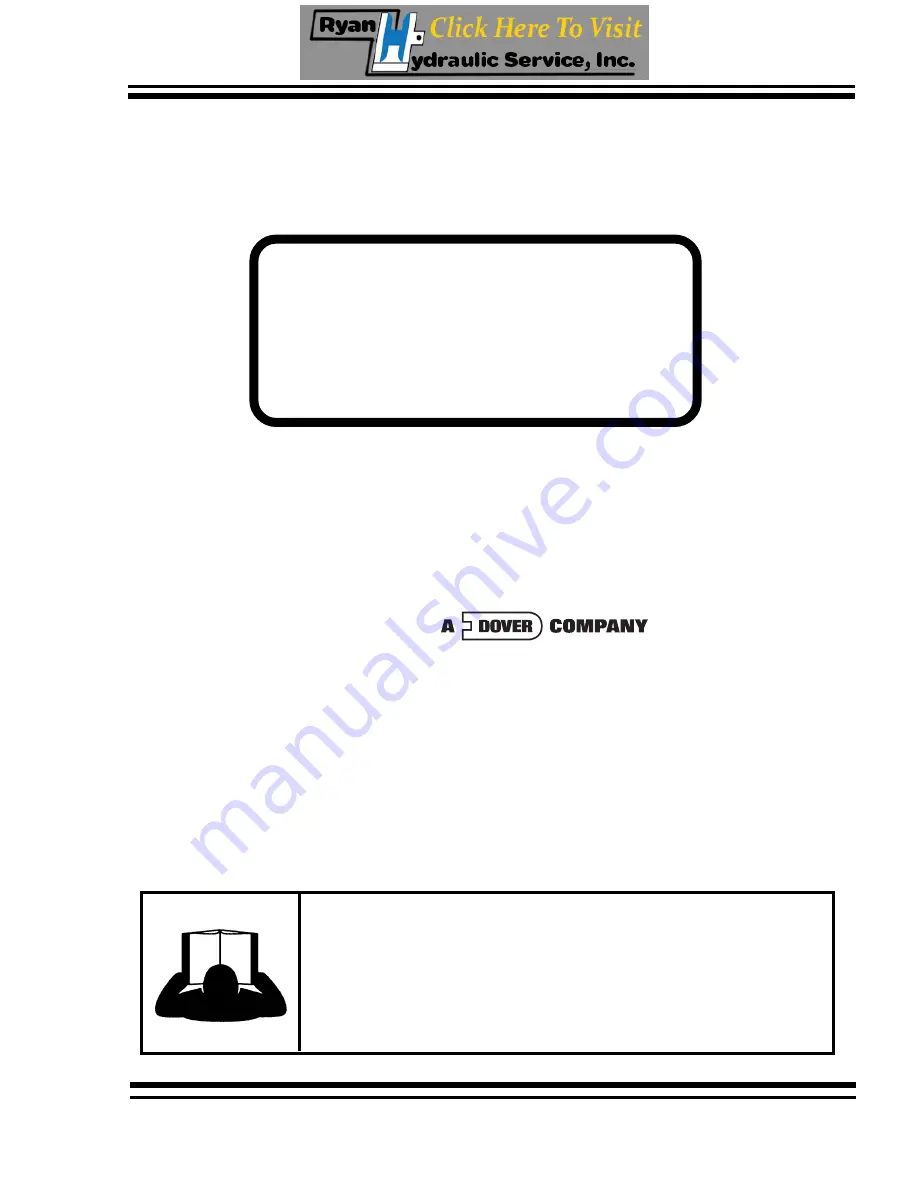
PMC 313
030619
INSTRUCTION AND PARTS MANUAL
MODEL HL25
PLANETARY HYDRAULIC WINCH
P
M
L
THE LOGICAL CHOICE
PULLMASTER WINCH CORPORATION
8247-130th Street, Surrey, B.C. V3W 7X4, Canada
Telephone: 604-594-4444 Fax: 604-591-7332
Website: www.pullmaster.com
E-mail: [email protected]
READ THIS MANUAL BEFORE INSTALLING, OPERATING OR
SERVICING THIS PRODUCT. THIS MANUAL CONTAINS IMPORTANT
INFORMATION. MAKE THIS MANUAL AVAILABLE TO ALL PERSONS
RESPONSIBLE FOR THE OPERATION, INSTALLATION, SERVICING
AND MAINTENANCE OF THIS PRODUCT.