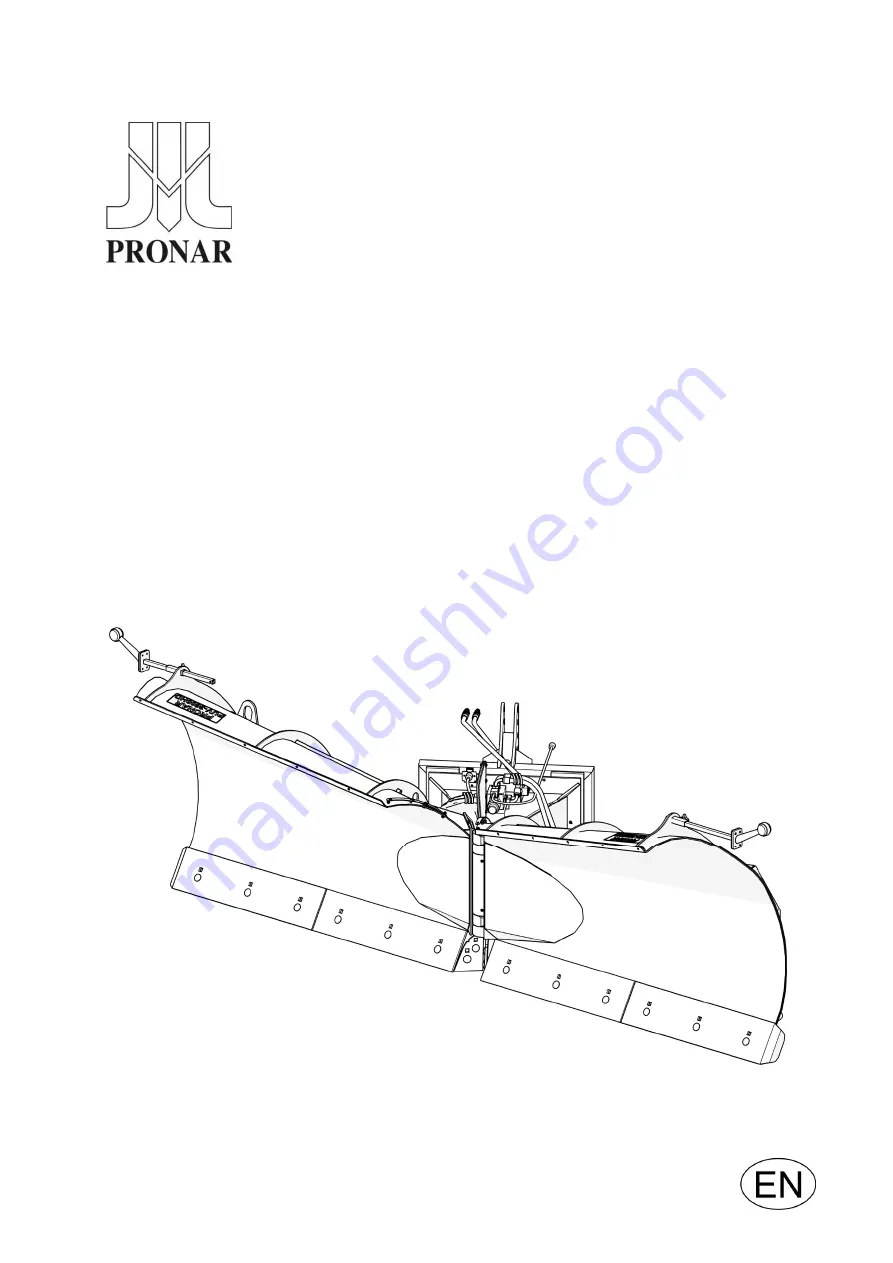
PRONAR Sp. z o.o.
17-210 NAREW, UL. MICKIEWICZA 101A, PODLASKIE PROVINCE
phone:
+48 085 681 63 29
+48 085 681 64 29
+48 085 681 63 81
+48 085 681 63 82
fax:
+48 085 681 63 83
+48 085 682 71 10
www.pronar.pl
OPERATOR`S MANUAL
SNOW PLOUGH
PRONAR PUV-3600HD
PRONAR PUV-4000HD
TRANSLATION OF THE ORIGINAL COPY OF THE MANUAL
EDITION 2A-09-2017
PUBLICATION NO 517N-00000000-UM
Summary of Contents for PUV-3600HD
Page 2: ......
Page 3: ...SNOW PLOUGH PRONAR PUV 3600HD PRONAR PUV 4000HD MACHINE IDENTIFICATION TYPE SERIAL NUMBER ...
Page 6: ......
Page 9: ...SECTION 1 BASIC INFORMATION ...
Page 19: ...SECTION 2 SAFETY ADVICE ...
Page 29: ...SECTION 3 DESIGN AND OPERATION ...
Page 38: ...PUV 3600HD PUV 4000HD SECTION 3 3 10 ...
Page 39: ...SECTION 4 CORRECT USE ...
Page 58: ...PUV 3600HD PUV 4000HD SECTION 4 4 20 ...
Page 59: ...SECTION 5 MAINTENANCE ...
Page 82: ...PUV 3600HD PUV 4000HD SECTION 5 5 24 ...
Page 83: ...NOTES ...