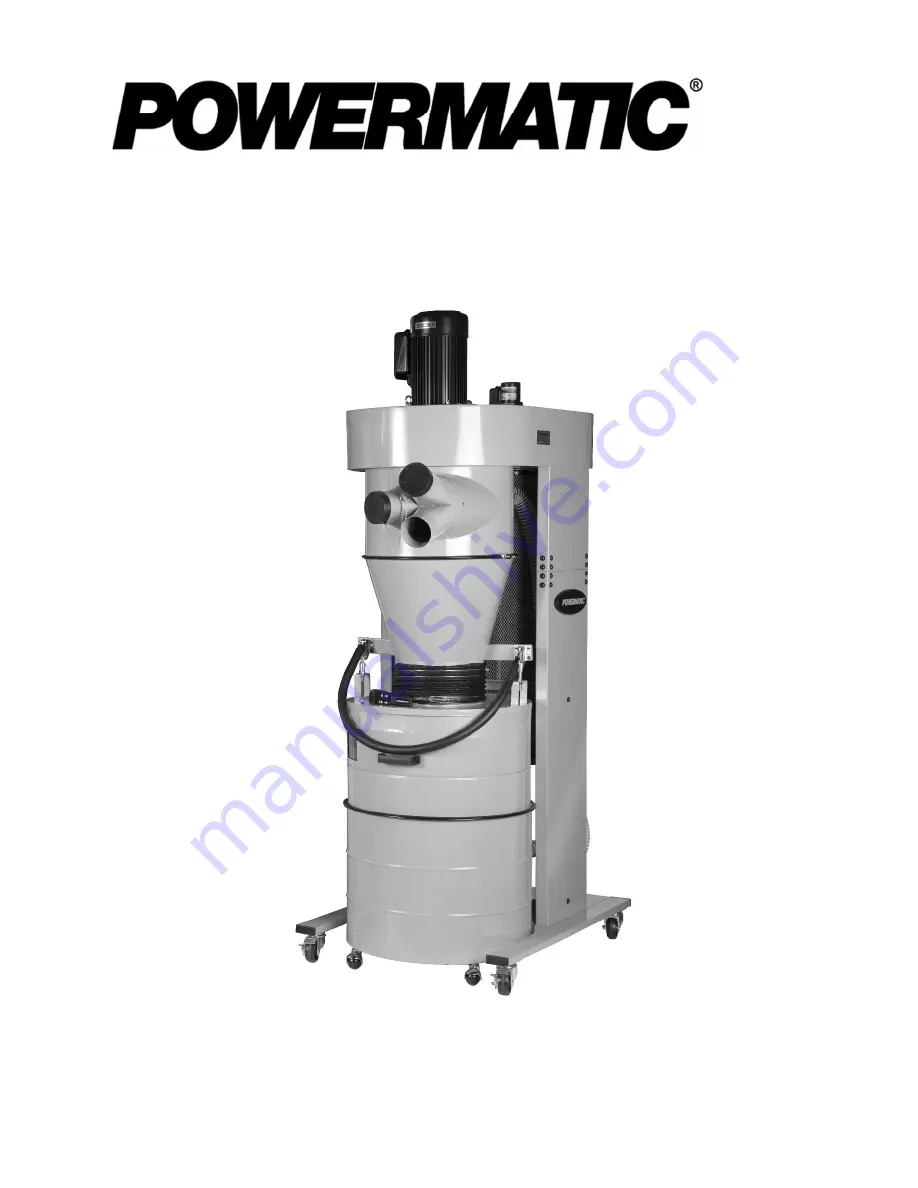
Operating Instructions and Parts Manual
Mobile Cyclone Dust Collector
Model PM2200HK
Powermatic
427 New Sanford Road
LaVergne, Tennessee 37086
Document No. M-1792200B
Ph.: 800-274-6848
Edition 6 06/2021
www.powermatic.com Copyright © 2017 Powermatic
for serial no. 2006001 and higher.
This .pdf document is bookmarked