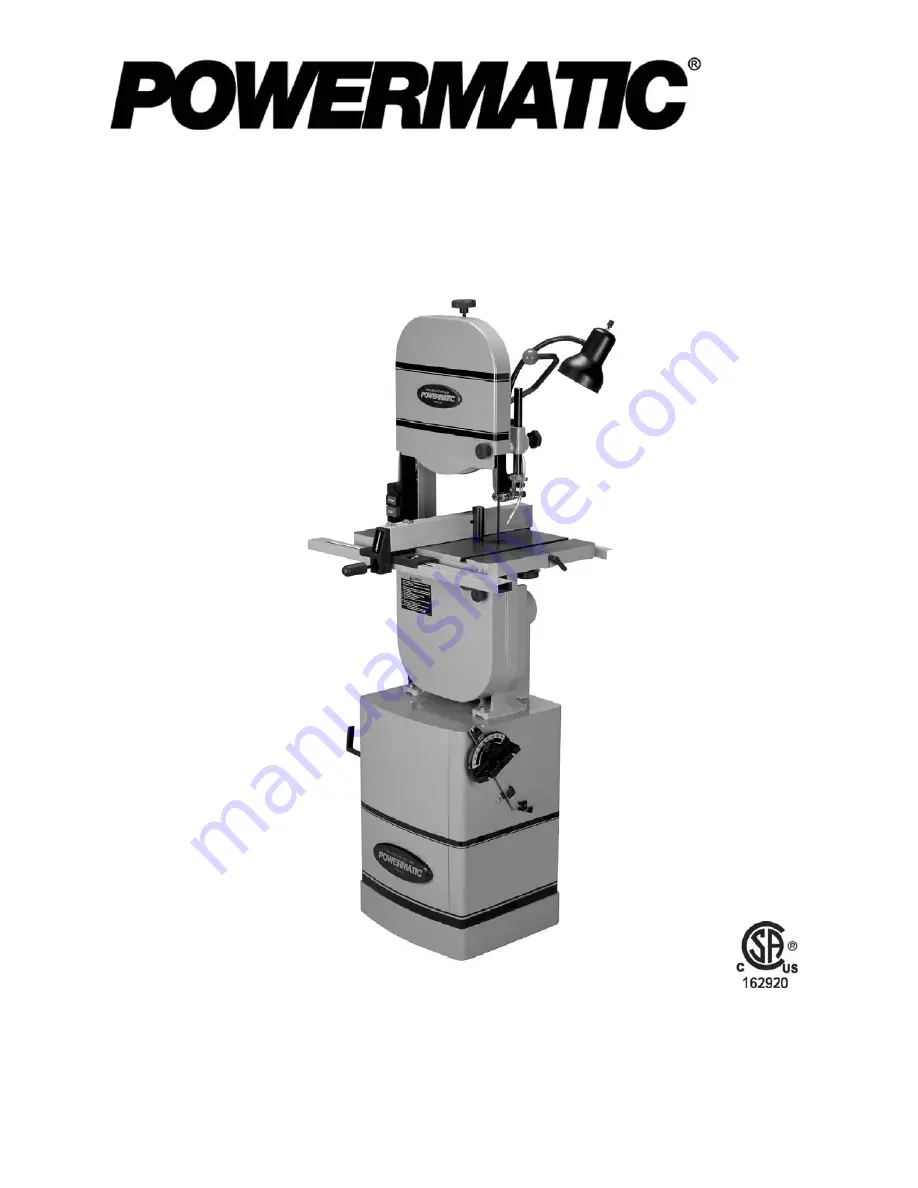
Operating Instructions and Parts Manual
14” Woodworking Band Saw
Model PWBS-14CS
WALTER MEIER (Manufacturing) Inc.
427 New Sanford Rd.
LaVergne, TN 37086
Part No. M-1791216
Ph.: 800-274-6848
Revision F
07/2013
www.powermatic.com
Copyright © 2013 Walter Meier (Manufacturing) Inc.
This .pdf document is bookmarked
Summary of Contents for 1791216K
Page 39: ...39 Body Assembly...
Page 41: ...41 Closed Stand Assembly...
Page 43: ...43 Fence and Rail Assembly...