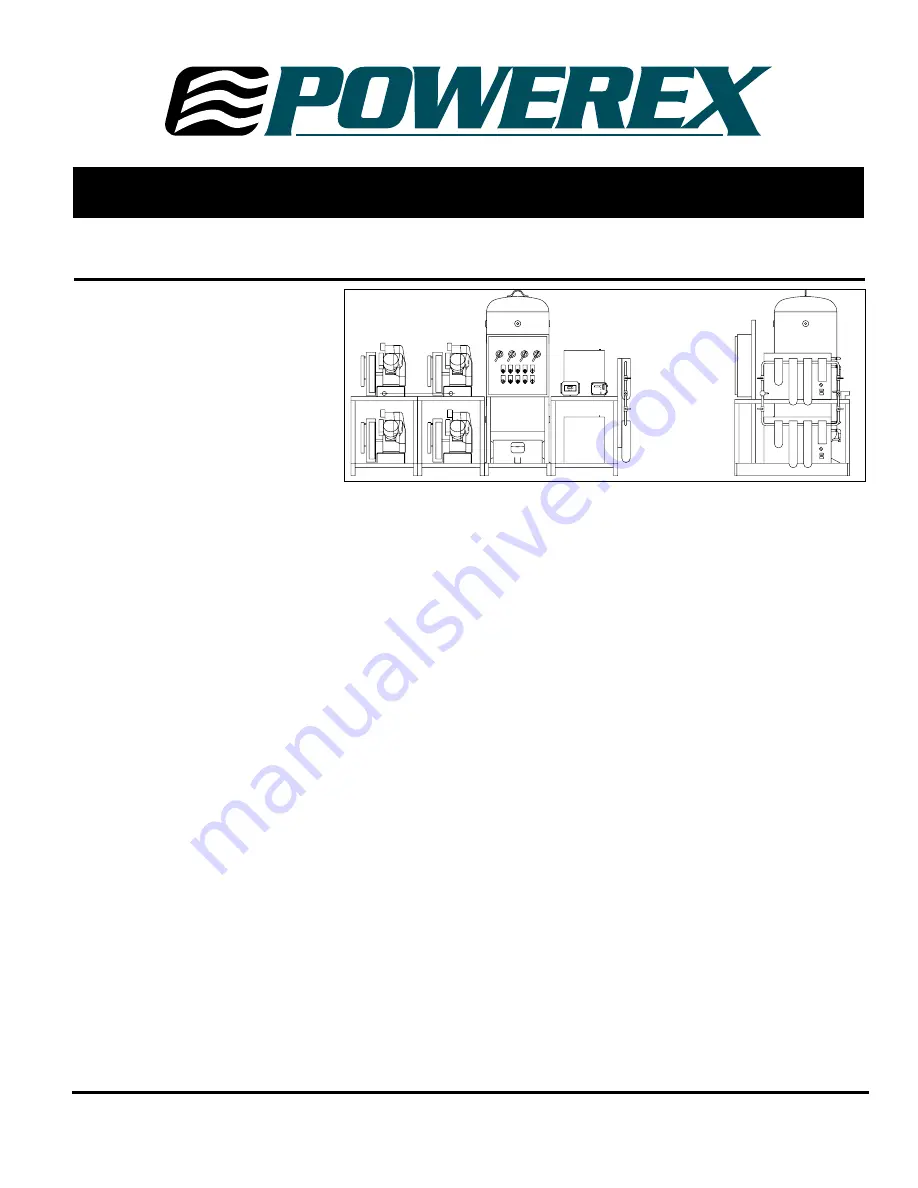
Please read and save these instructions. Read carefully before attempting to assemble, install, operate or maintain the product described.
Protect yourself and others by observing all safety information. Failure to comply with instructions could result in personal injury and/or
property damage! Retain instructions for future reference.
Powerex • 150 Production Drive • Harrison, OH 45030 • USA
Description
The Powerex medical system package is
designed to provide medical breathing
air for hospital and medical institutes.
This system meets NFPA 99
requirements for Level 1 breathing air.
OILLESS OPT/OPS COMPRESSOR
The Powerex oilless reciprocating air
compressor has advanced compressor
technology through the development
of a completely oilless compressor. The
Powerex reciprocating compressor is
provided in duplex, triplex or quadplex
configurations with head unloaders to
provide start, stop or continuous
operation. Composite piston
technology and continuously
lubricating bearings provide oil-free air
reliability for years to come.
RECEIVER TANK
The ASME, National Board registered
air receiver is provided in sizes from
120 to 240 gallons. Each receiver is
rated at 200 PSIG working pressure.
Receivers are provided with sight glass
and moisture drain (manual or
automatic).
CONTROL PANEL
The NEMA 12 control panel is provided
in duplex, triplex or quadplex
configurations and meets NFPA 99
requirements for medical air. Primary
voltage is protected by fusing or circuit
breaker. Control transformer power is
110 volts and protected by secondary
fusing. Pressure control switches signal
the compressors on and off cycle and
signal lag compressor(s) to come on if
air demand increases. A lag, lag
pressure switch or transducer signals a
light and audible alarm warning of a
low pressure condition which is factory
set at 40 PSIG. An acknowledge button
is provided for start condition and
maintenance. The adjustable timer
alternator cycles each compressor so
equal run time is maintained. This
alternator is factory set to alternate
the compressors every 10 minutes. The
exterior of the control panel is
accessible through the door. The panel
disconnects on/off/auto switches run
lights, power on lights, run
hourmeters, lag pressure light, high
GENERAL PRODUCT MANUAL
temperature light and overload reset.
This control panel is UL listed.
DEW POINT MONITOR
The Powerex dew point monitor
provides indication of dew point and
temperature. It’s microprocessor
controlled with user programmable
output range, alarm and calibration.
The NEMA enclosure is protected by a
polymer viewing cover.
CARBON MONOXIDE
MONITOR/ALARM
The carbon monoxide monitor provides
warning to the user of air-supplied
respirators alarming and metering the
presence of carbon monoxide. The
monitor is provided in a NEMA 12
enclosure. In addition to audio/visual
alarm, the meter displays the
concentration of CO in the compressed
air. The meter operates from a 110
VAC supply. Alarm points are set a
10PPM (low) and 20 PPM (high).
AIR COOLED AFTERCOOLER
Four models of beltguard aftercoolers
sized to provide an approach of 20°F.
Constructed of copper tubing and
metal headers for a rugged
construction.
AIR DRYER (REFRIGERATED OR
DESICCANT)
The Powerex air drying system provides
air at 38°F at 100 PSIG for refrigerated
units and -40°F dew point for desiccant
dryer systems. Each system is connected
with bypass capability.
The refrigerated compressed air
dryer(s) are noncycling, direct
expansion type, using R-22 refrigerant,
IN259200AV 11/00
P
U
R
E
A
I
R
T
E
C
H
N
O
L
O
G
Y
CFC free. A hot gas bypass valve is
provided to maintain 38°F evaporator
temperature. The dryer is self-
regulating for large load swings. Heat
exchangers are made of copper tube
construction and insulated.
The regenerative desiccant consists of
two (dual) towers filled with desiccant.
Each tower is switched on and off
stream, alternating the air system
stream and then being regenerated.
Dry purge air pulls moisture from the
desiccant and carries the moisture out
of the air.
MEDICAL FILTER SYSTEM
The medical filter system consists of a
duplex series of filters and pressure
regulators. Air enters the system and is
directed to either bank of filets
controlled by ball valve. The first stage
filter removes solids and liquid
particles. The next stage of filters
remove submicronic particles and
aerosols. The third and final filter is
carbon activated to remove unpleasant
odors. Maximum operating temper-
ature is 125°F and maximum pressure is
150 PSIG.
CONDENSATE DRAIN VALVE
A condensate drain valve must be
installed on any tank. This valve
removes liquid that collects during
compressor operation.
Drain liquid from tank daily.
Safety Guidelines
This manual contains information that is
very important to know and understand.
This information is provided for SAFETY
and to PREVENT EQUIPMENT PROBLEMS.
Medical Package System
CAL. PORT
CAL. PORT
ZERO CAL.
ZERO CAL.
ALARM
ALARM
SET
SET
ADJ.
ADJ.
PANADRY
PANADRY
F
DEW/FROST POINT
DEW/FROST POINT
PPM
PPM
AUTO CAL
AUTO CAL
CAUTION
CAUTION
ALARM
ALARM
SAFE
SAFE
FLOW
FLOW