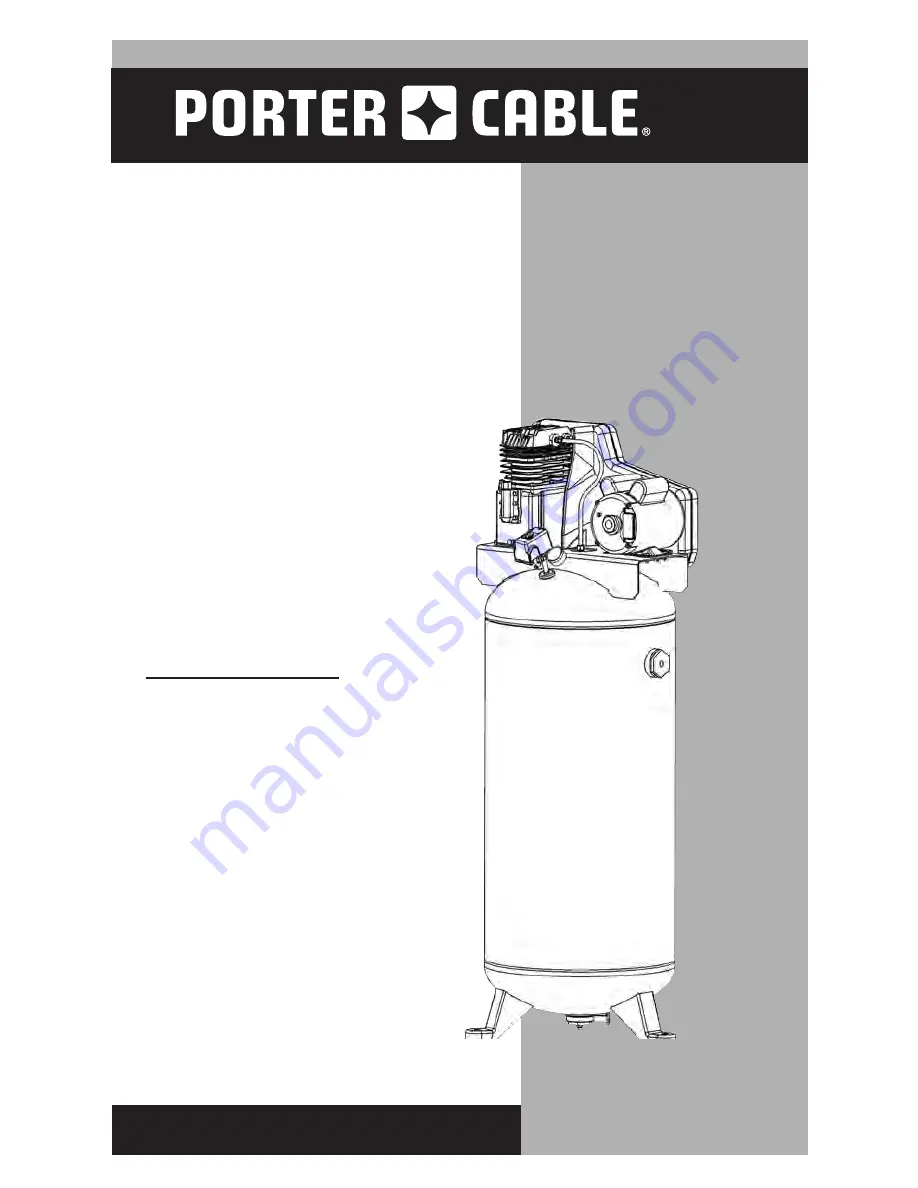
Compresores eléctricos de
aire, de una sola etapa y
accionamiento por correa
Single Stage, Belt Drive,
Electric Air Compressors
Compresseurs d’air
électriques à un étage à
entraînement par courroie
Français : Page 31
Español: Página 60
Instruction manual
Manuel d'instructions
Manual de instrucciones
PXCMLC3706056
200-2887_Rev. A_7-12
Summary of Contents for PXCMLC3706056
Page 13: ...13 ENG OPEN CLOSE F E Fig 6 ...