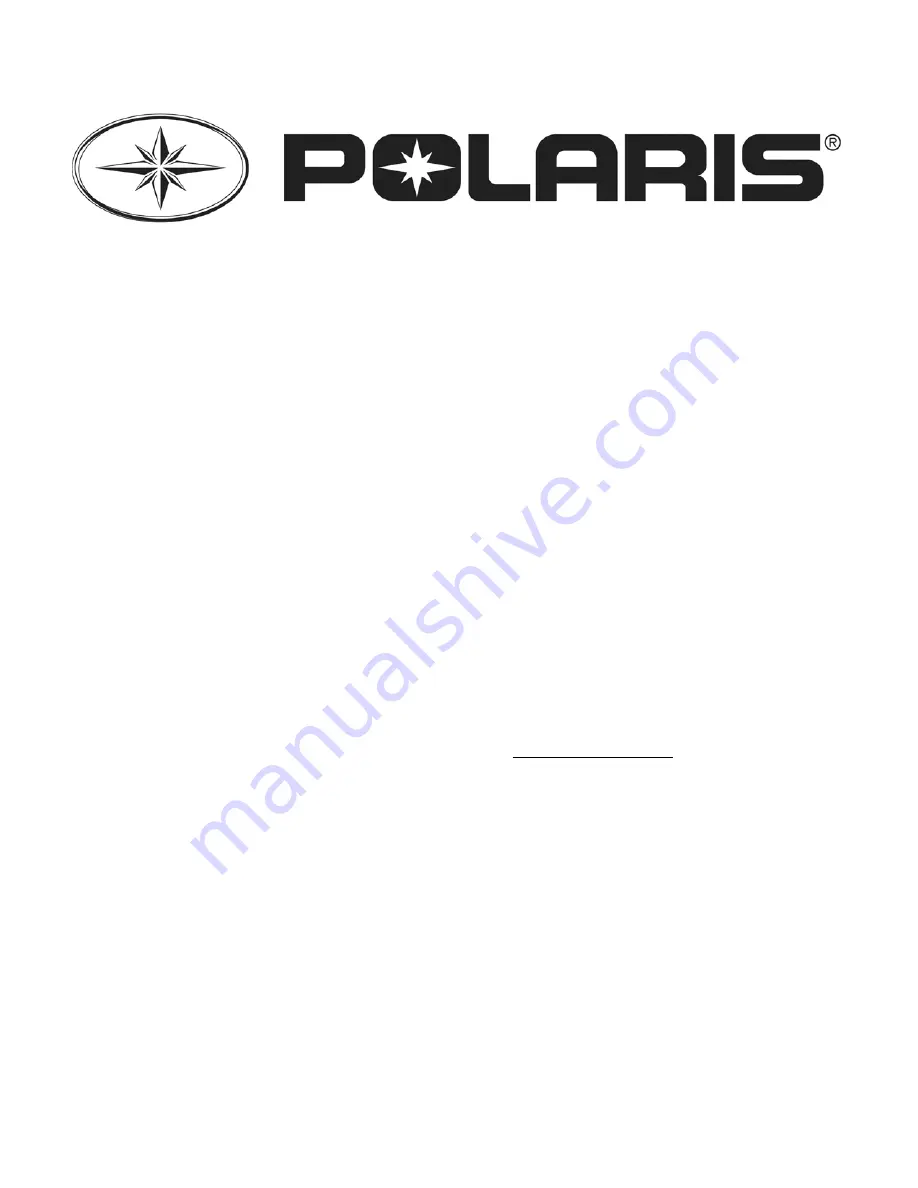
2012-2013 RANGER RZR® 170
SERVICE MANUAL
FOREWORD
The information printed within this publication includes the latest product information at time of print. The most recent
version of this Service Manual is available in electronic format at www.polarisdealers.com.
This Service Manual is designed primarily for use by certified Polaris Master Service Dealer
technicians in a properly
equipped shop and should be kept available for reference. All references to left and right side of the vehicle are from
the operator's perspective when seated in a normal riding position.
Some procedures outlined in this manual require a sound knowledge of mechanical theory, tool use, and shop
procedures in order to perform the work safely and correctly. Technicians should read the text and be familiar with the
service procedures before starting any repair. Certain procedures require the use of special tools. Use only the proper
tools as specified. If you have any doubt as to your ability to perform any of the procedures outlined in this Service
Manual, contact an authorized dealer for service.
We value your input and appreciate any assistance you can provide in helping make these publications more useful.
Please provide any feedback you may have regarding this manual. Authorized dealers can submit feedback using 'Ask
Polaris'. Click on 'Ask Polaris', and then click on 'Service Manual/Service Literature Question'.
Consumers, please provide your feedback in writing to: Polaris Industries Inc. ATTN: Service Publications Department,
2100 Hwy 55, Medina, MN 55340.
Publication Printed July 2012 (PN 9923983)
© Copyright 2012 Polaris Sales Inc. All information contained within this publication is based on the latest product information at the time of publication. Due to constant
improvements in the design and quality of production components, some minor discrepancies may result between the actual vehicle and the information presented in this
publication. Depictions and/or procedures in this publication are intended for reference use only. No liability can be accepted for omissions or inaccuracies. Any
reprinting or reuse of the depictions and/or procedures contained within, whether whole or in part, is expressly prohibited. Printed in U.S.A.