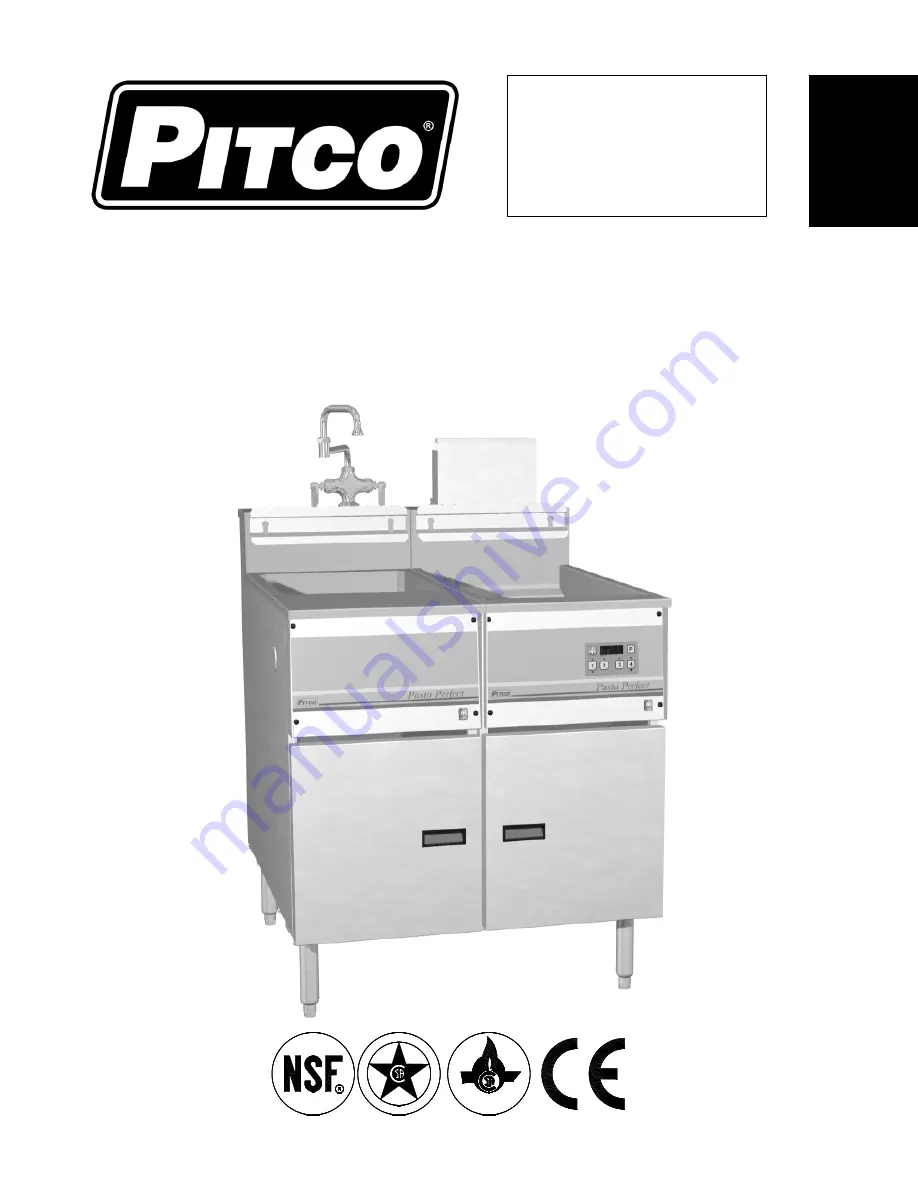
Installation & Operation Manual
L20-294, rev. 0 (1/06)
IMPORTANT FOR FUTURE REFERENCE
Please complete this information and retain this manual
for the life of the equipment:
Model #: ___________________________
Serial #: ___________________________
Date Purchased: ____________________
ENGLISH
PG14D: Floor Model Gas Pasta Cooker
RS14D: Floor Model Rinse Station
Built after 4/1995
D
E
I
F
I
T
R
E
C
D
E S I G N
C
I
R
E
T
I
F
E D