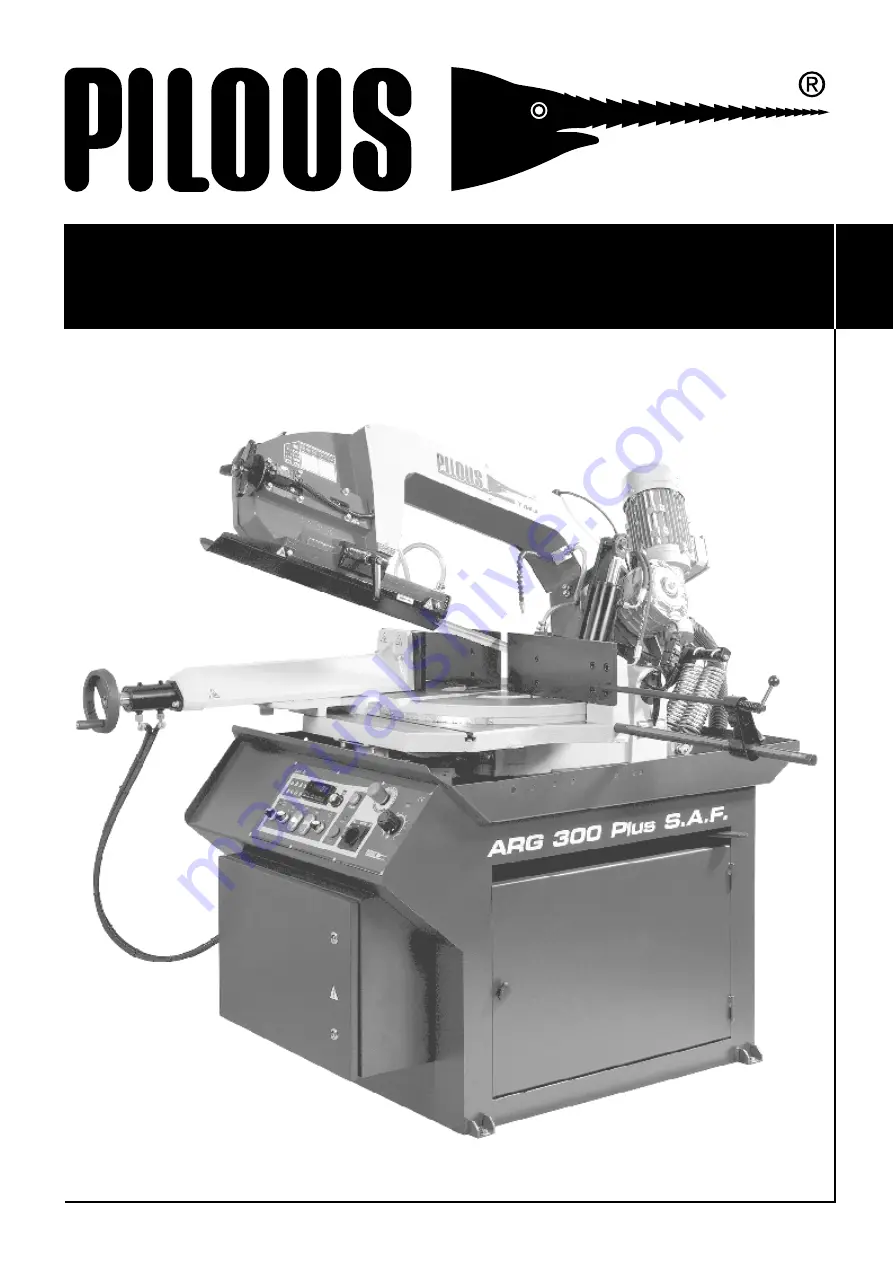
INSTRUCTION MANUAL
Pilous - pasove pily, spol. s r.o., Zelezna 9
tel.: 00 420 543 25 20 10, fax: 00 420 543 25 20 11, e-mail:[email protected]
, 619 00 Brno, Czech Republic
ARG 250 S.A.F. • ARG 250 plus S.A.F. ARG 300 S.A.F.
ARG 300 plus S.A.F. ARG 330 S.A.F. ARG 330 plus S.A.F.
•
•
•
Summary of Contents for ARG 250 plus S.A.F.
Page 34: ...11 3 2 Table turning table pivot and vice assembly ARG 250 plus S A F ARG 300 plus S A F...
Page 44: ......
Page 45: ......
Page 47: ......