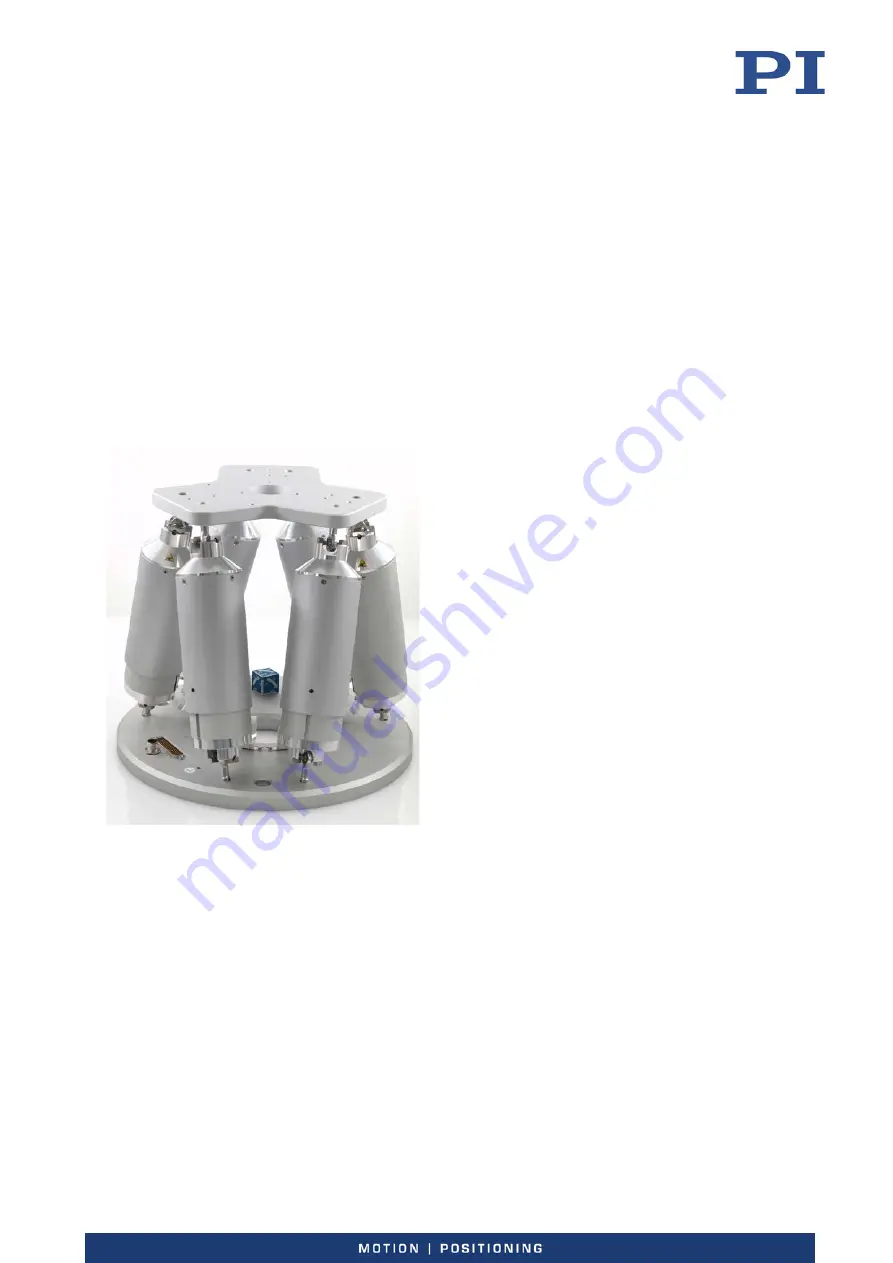
Physik Instrumente (PI) GmbH & Co. KG, Auf der Roemerstrasse 1, 76228 Karlsruhe, Germany
Phone +49 721 4846-0, Fax +49 721 4846-1019, Email [email protected], www.pi.ws
MS207E
H-820 Hexapod Microrobot
User Manual
Version: 2.3.0
Date: 04.12.2019
This document describes the following product:
H-820.D2
Hexapod microrobot, basis model, 20 mm/s,
20 kg load, Sub-D connector (m), cable set 3 m