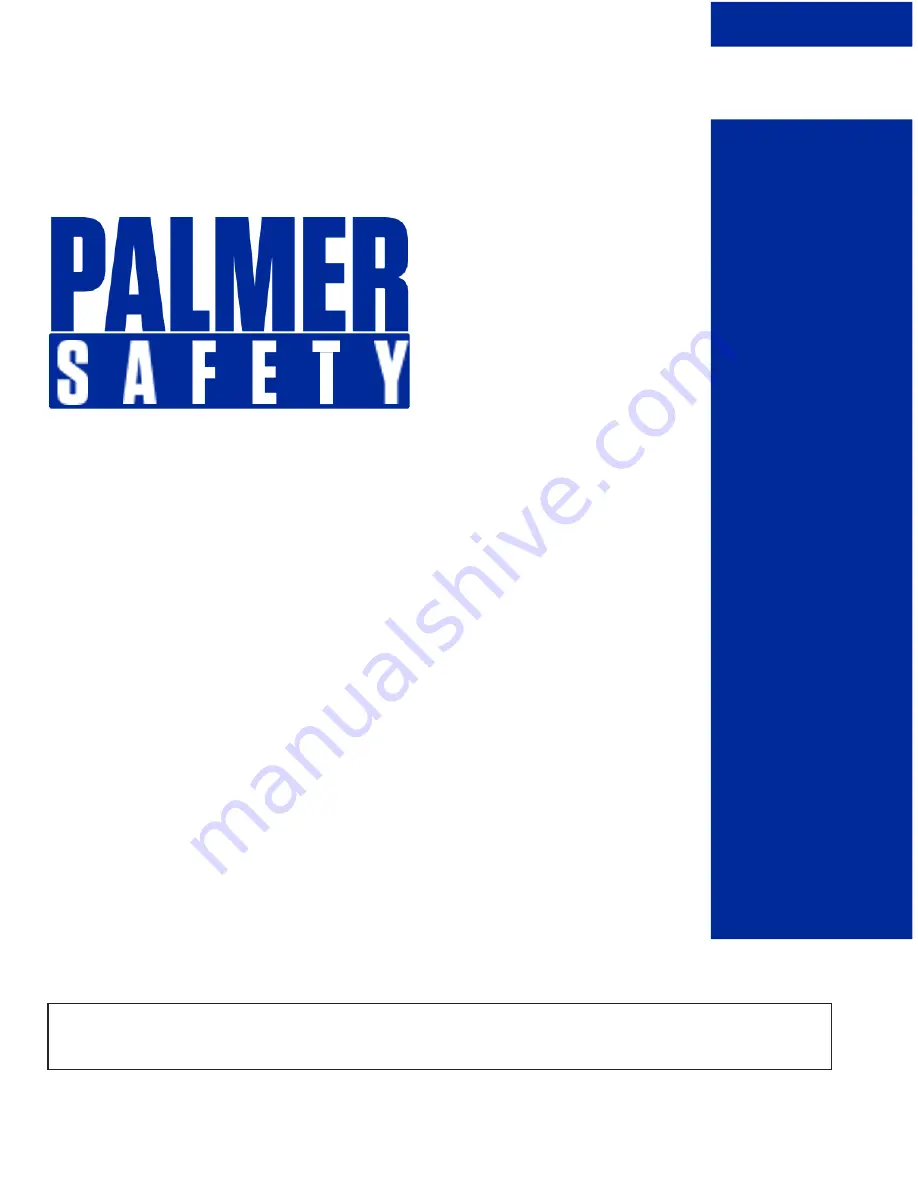
A300200 2-Person Temporary Horizontal Lifeline
User Instruction Manual
For the purposes of this manual, the PALMER SAFETY 2-Person Temporary Horizontal Lifeline may be referred to as the PALMER SAFETY 2-Person
Temporary HLL, the Horizontal Lifeline, HLL, the system, or the lifeline.
This manual is intended to meet the
Manufacturer’s
Instructions as required by the American National Standards
Institute (ANSI) Z359 and should be used as part of an employee training program as required by the Occupational
Safety and Health Administration (OSHA).