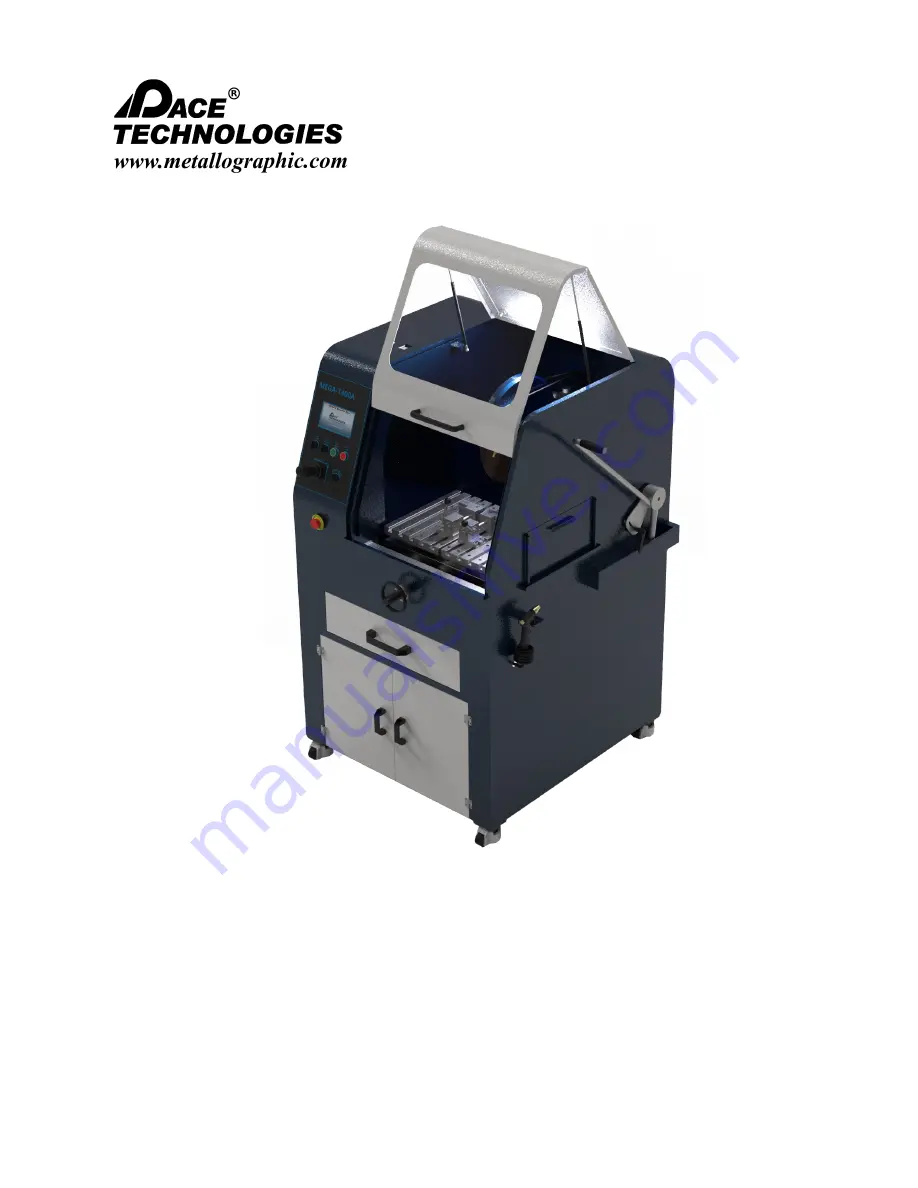
-
-
-
-
-
-
-
-
-
-
-
-
-
-
-
-
-
-
-
-
-
-
-
-
-
-
-
-
-
-
-
-
-
-
-
-
-
-
-
-
-
-
-
-
-
-
-
-
-
-
▲
I
NSTRUCTION
M
ANUAL
MEGA
-
T400A
Abrasive Cutter
3601 E. 34th St. Tucson, AZ 85713 USA Tel. +1
-
520
-
882
-
6598 Fax +1
-
520
-
882
-
6599 email: [email protected] Web: https://www.metallographic.com
Please read this instruction manual carefully and follow all installation, operating and safety guidelines.
Equipment Type:
400 mm (~16
-
inch)
Automated Abrasive Cut
-
off Machine
Model:
MEGA
-
T400A
Electrical
Requirements:
480 Volts (3
-
phase)
Frequency:
50/60 Hz
Motor Horsepower:
Variable speed Servo Motor:
12 KW (16 hp) @480V, 3
-
phase
Manual Revision Date:
December 23, 2023
This instruction manual is
provided with each piece of
delivered equipment.