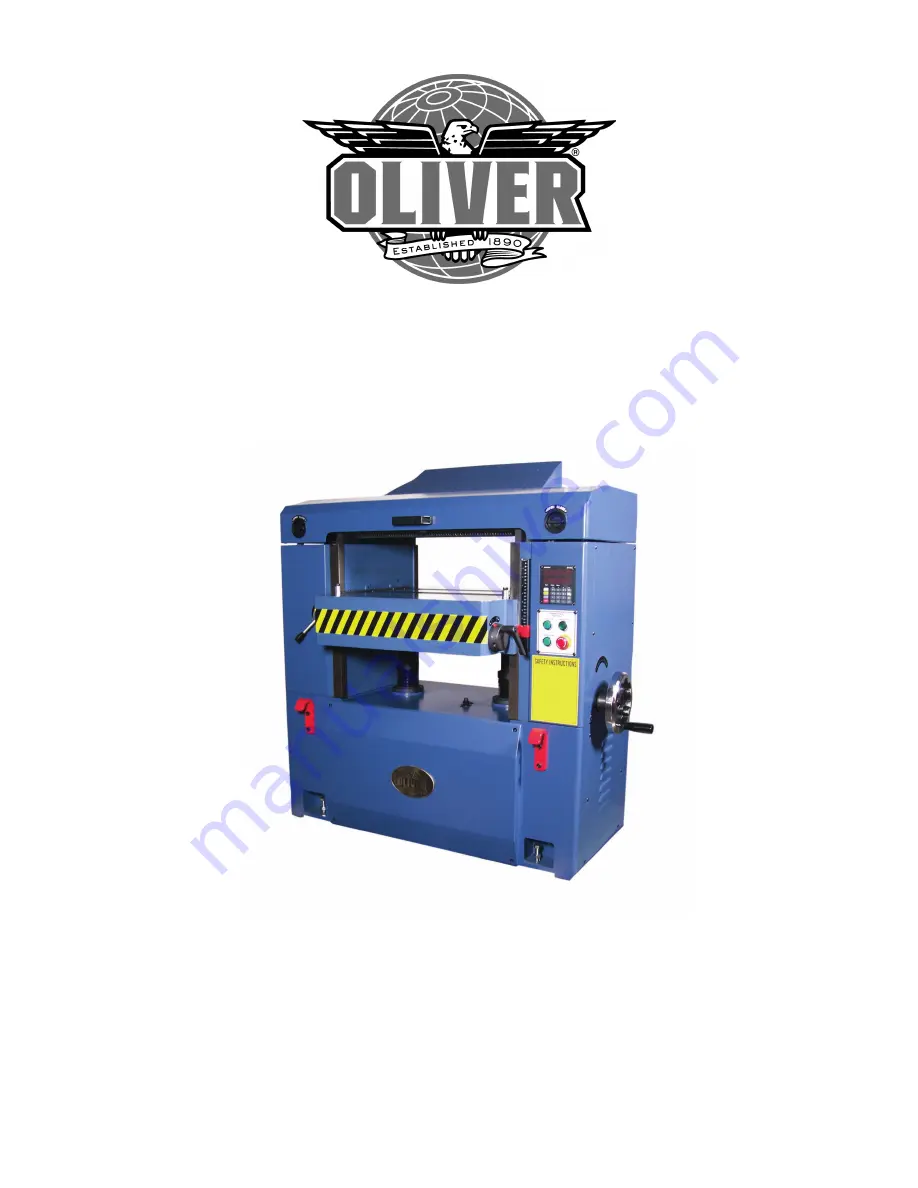
4470 Industrial Planer 2
5
”
Owner’s Manual
Oliver Machinery
M-4470 9/20
17
Kent, WA 98032
[email protected]
Copyright 2003
www.olivermachinery.net
4470 Industrial Planer 2
5
”
Owner’s Manual
Oliver Machinery
M-4470 9/20
17
Kent, WA 98032
[email protected]
Copyright 2003
www.olivermachinery.net