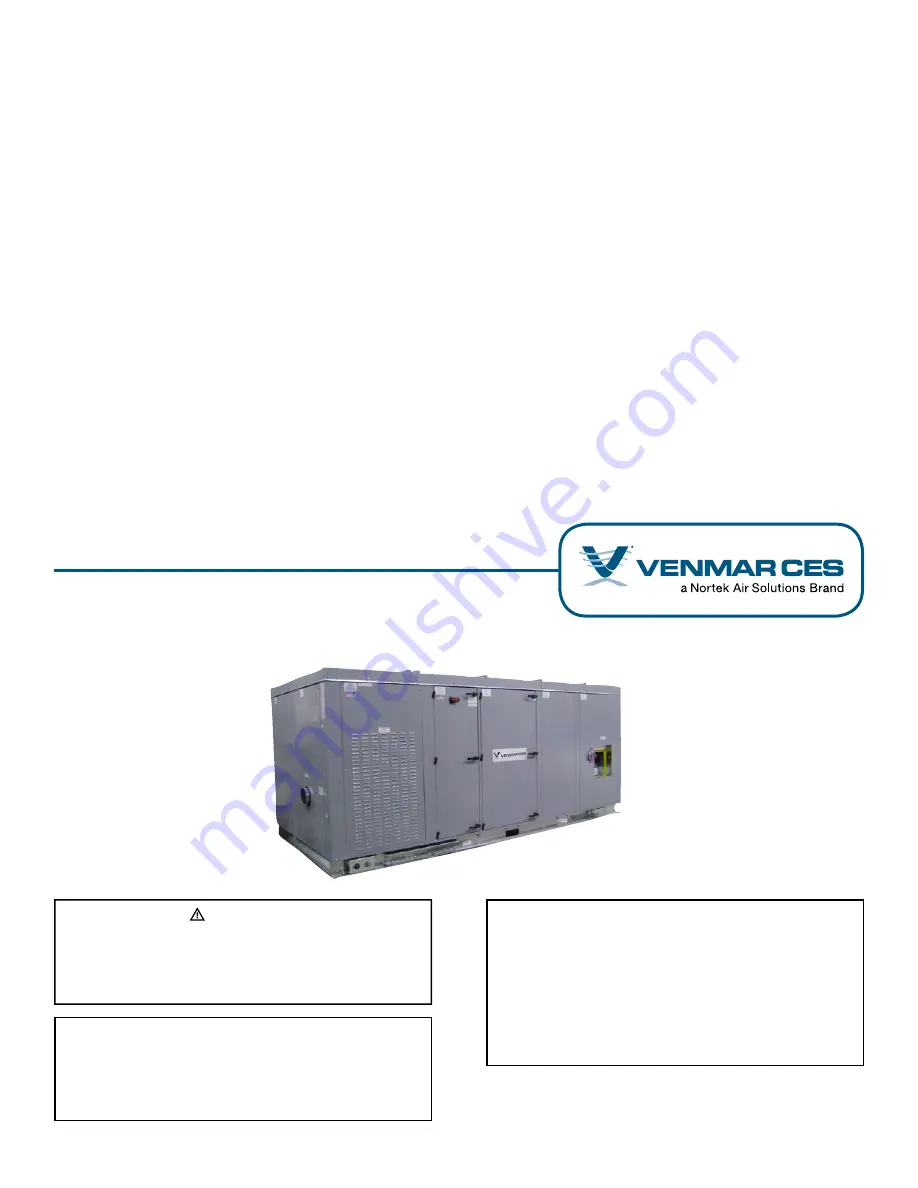
VHC
Energy Recovery Ventilators with Enthalpy Wheels and
Integrated Heating and Cooling
Installation, Operation and Maintenance Instructions Manual
Capacity: 800 to 5,500 cfm
Model: VHC-36, VHC-42, VHC-50
IMPORTANT
The use of this appendix is specifically intended for a
qualified installation and service agency. A qualified in-
stallation and service agency must perform all installation
and service of these appliances.
FOR YOUR SAFETY
What to do if you smell gas:
1. Open windows if appliance is indoors.
2. Do not touch electrical switches or use any phone
in the building.
3. Extinguish any open flame.
4. Leave the building immediately.
5. Immediately call Gas Supplier.
WARNING
Improper installation, adjustment, alteration, service or
maintenance can cause injury or death. Read the instal-
lation, operation and maintenance instructions thor-
oughly before installing or servicing this equipment.