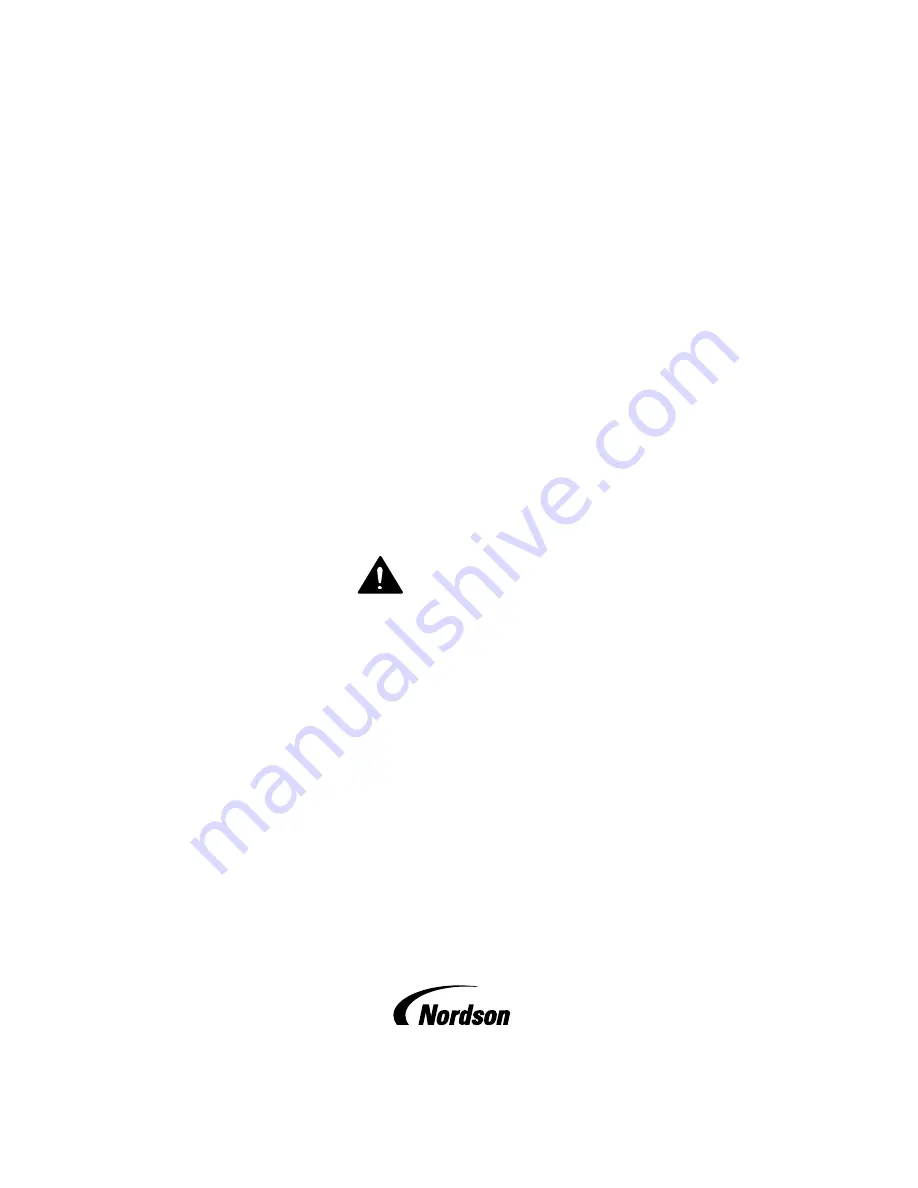
ProBlue Flex Adhesive Melter
Using the OLED User Interface
Customer Product Manual
Part 1128351_02
Issued 6/20
NORDSON CORPORATION
DULUTH, GEORGIA
USA
www.nordson.com
This document contains important safety information.
Be sure to read and follow all safety information in this
document and any other related documentation.
Summary of Contents for ProBlue Flex
Page 73: ...OLED User Interface 67 Part 1128351_02 E 2020 Nordson Corporation Figure 3 ATS PCA Board...
Page 129: ......
Page 130: ......