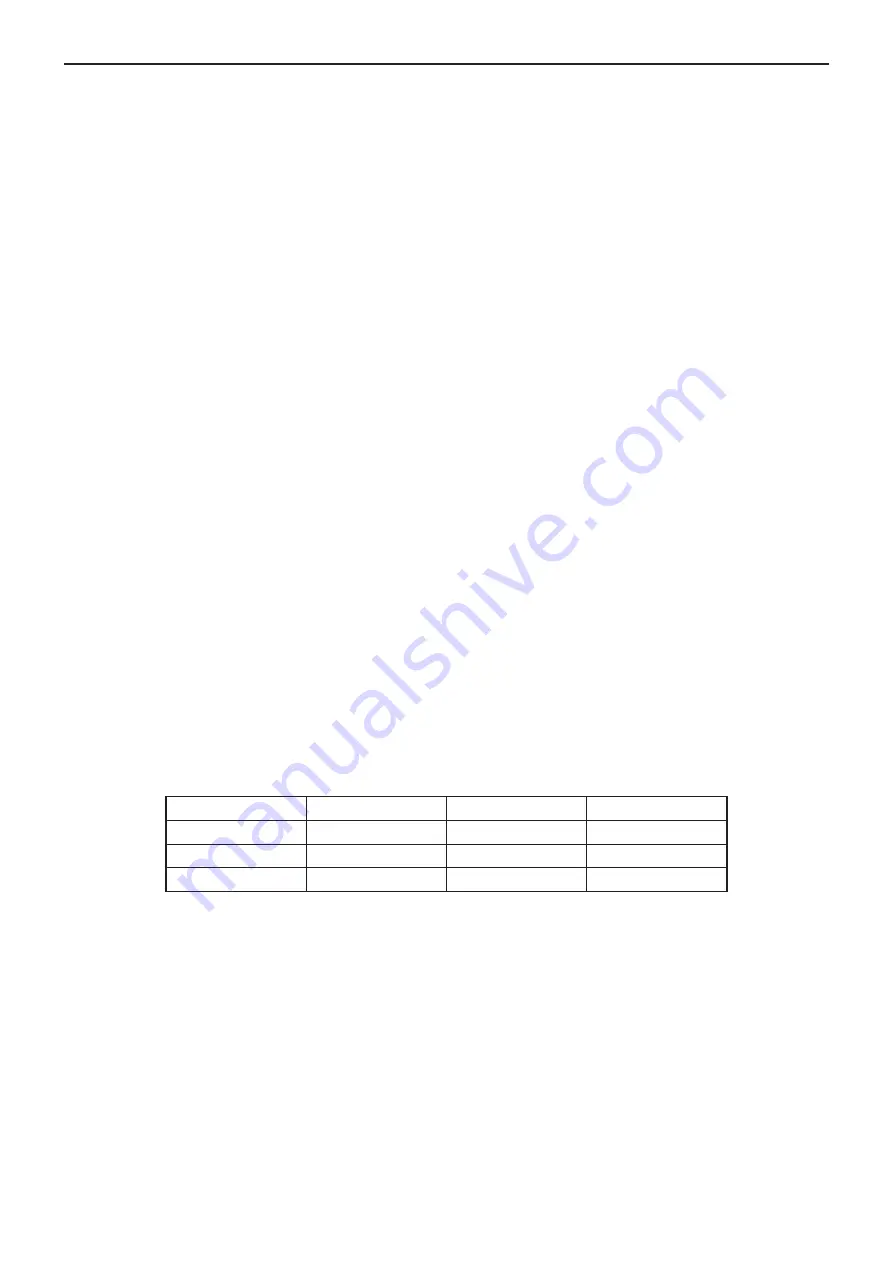
INTRODUCTION
4
Most accident happens due to the disregard of basic safety rules or
precautions. In order to prevent accidents from happening, the factors
responsible for accidents must be avoided beforehand.
For this reason, please read this manual and fully understand the
precautions for safety and the proper procedures and directions for
inspection and maintenance before starting operation.
Performing maintenance and repair without adequate knowledge may
cause inadvertent accidents.
4
It is not possible to cover all the possible cases of accidents in this
"WORKSHOP MANUAL". Therefore, attention should be given to
precautions other than the ones mentioned in this "WORKSHOP
MANUAL". Especially, when repair and maintenance work which are not
covered in this "WORKSHOP MANUAL" are carried out, always work
under the direction of an instructor who understands the matter.
[Control System Transition]
Model
IGBT Control
FET Control
CAN-BUS Control
FB10P~18P
~221AE1250
221AE1251~
221AE3656~
FB20P~28P
~241AC4968
241AC4969~
241AC6266~
FB30P
~251AC0880
-
251AC0881~
4
Please note that the contents of the explanation in this manual are
different according to each control system.
Please refer to the applicable explanations.
https://www.forkliftpdfmanuals.com/