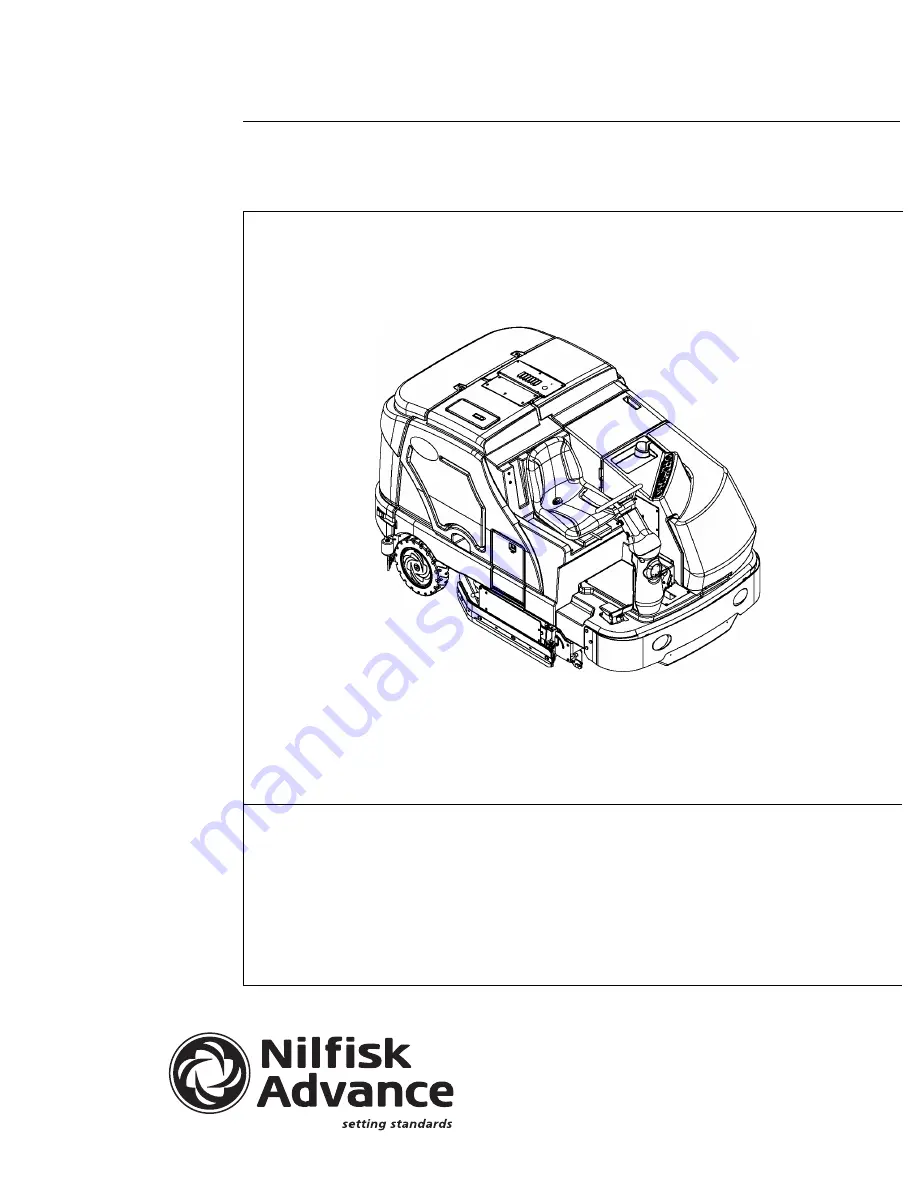
7/09 FORM NO. 56043124
Condor XL
™
Service Manual
Advance Models:
56110000(LPG/48”), 56110001(Petrol/48”), 56110002(Diesel/48”), 56110003(LPG/60”),
56110004(Petrol/60”), 56110005(Diesel/60”), 56110006(LPG/62”), 56110007(Petrol/62”),
56110008(Diesel/62”), 56110009(LPG/67”), 56110010(Petrol/67”), 56110015(Diesel/67”)
56111035(LPG-AXP/48”), 56111036(Petrol-AXP/48”), 56111037(Diesel-AXP/48”)
56111038(LPG-AXP/60”), 56111039(Petrol-AXP/60”), 56111040(Diesel-AXP/60”)
56111041(LPG-AXP/62”), 56111042(Petrol-AXP/62”), 56111043(Diesel-AXP/62”)
56111044(LPG-AXP/67”), 56111045(Petrol-AXP/67”), 56111046(Diesel-AXP/67”)
Summary of Contents for 56110000
Page 2: ......
Page 11: ...FORM NO 56043124 Condor XL 11 FIGURE 4 ...
Page 16: ...16 FORM NO 56043124 Condor XL FIGURE 6 LUBRICATION POINTS ...
Page 72: ...72 FORM NO 56043124 Condor XL ENGINE SYSTEM ...
Page 82: ...82 FORM NO 56043124 Condor XL HYDRAULIC SYSTEM ...
Page 83: ...FORM NO 56043124 Condor XL 83 HYDRAULIC SYSTEM ...
Page 93: ...FORM NO 56043124 Condor XL 93 APPENDIX HYDRAULIC SCHEMATIC ...
Page 102: ......