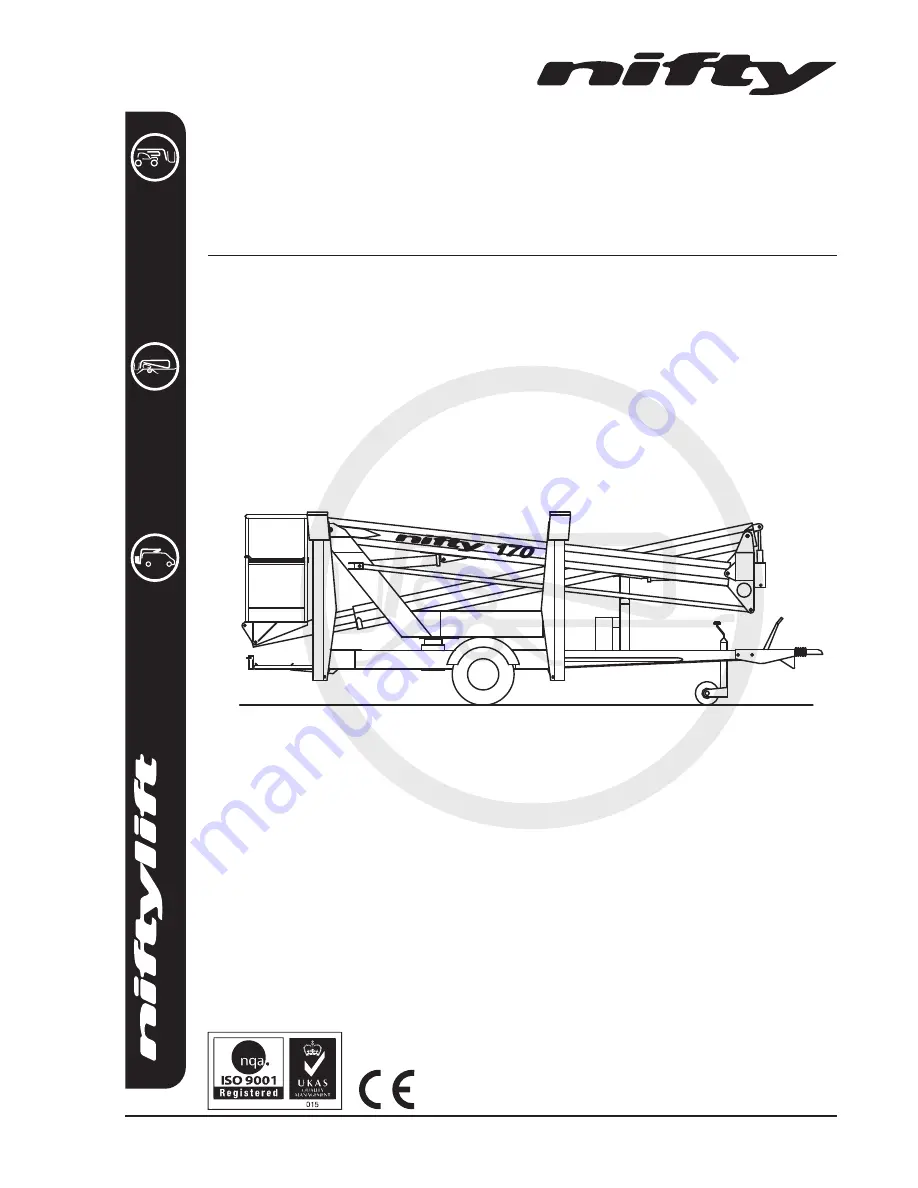
in
fo
@
n
if
ty
li
ft
.c
o
m
.com
170/TM50
Operating and Safety Instructions
MODEL 170 (TM50) SERIES
Manufactured by:
Niftylift Limited
Fingle Drive
Stonebridge
Milton Keynes
MK13 0ER
England
www.niftylift.com
e-mail: [email protected]
Tel: +44 (0)1908 223456
Fax: +44 (0)1908 312733
M50151/08
Summary of Contents for 170H Series
Page 2: ......