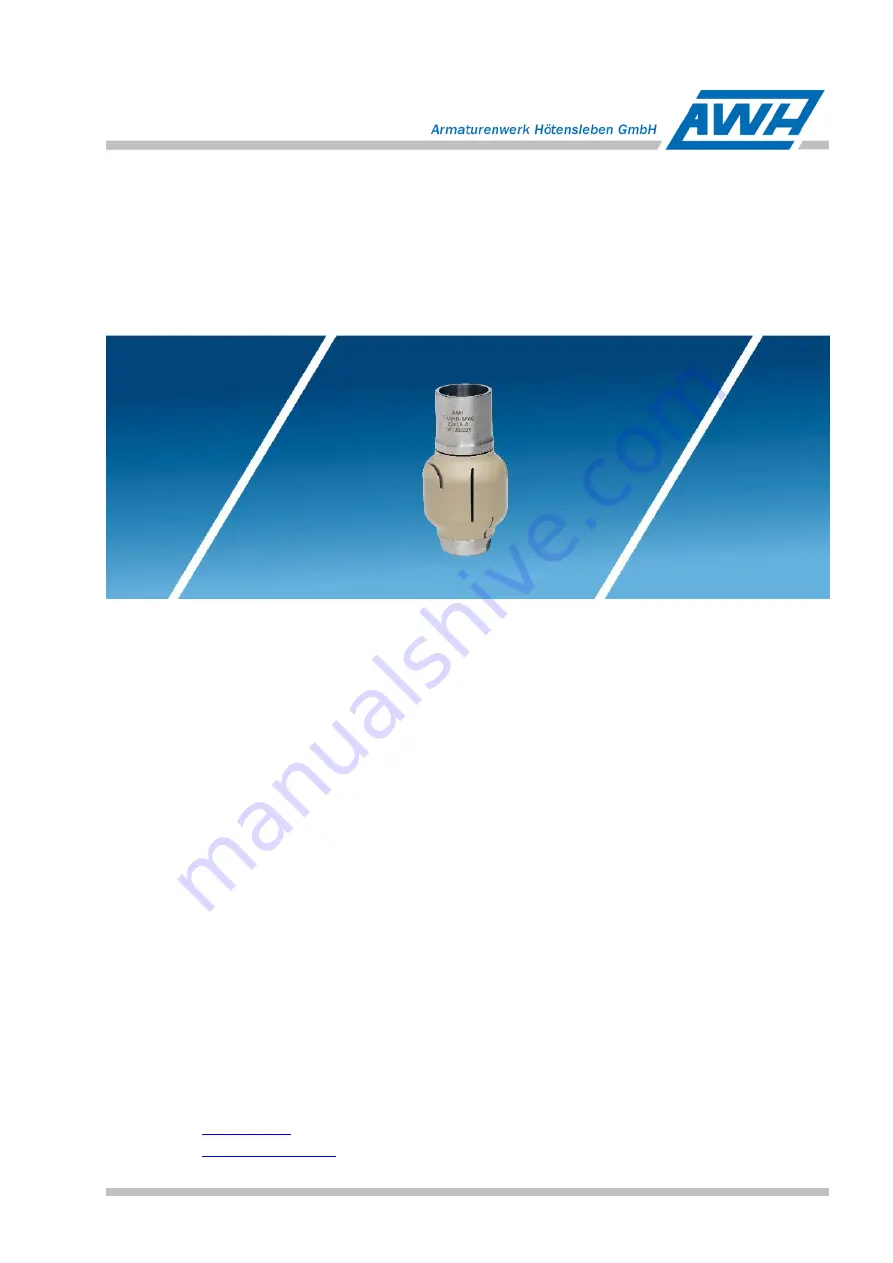
A member of Neumo Ehrenberg Group
OPERATING / INSTALLATION INSTRUCTIONS
(Translation)
Container cleaning device
Spate cleaner TANKO
®
SF40
Armaturenwerk Hötensleben GmbH
Schulstr. 5-6
39393 Hötensleben, Germany
Telephone: +49 39405 92-0
Fax:
+49 39405 92-111
E-mail:
Homepage:
ID no.: 664BASF0000EN - 2016/09 Rev. 1