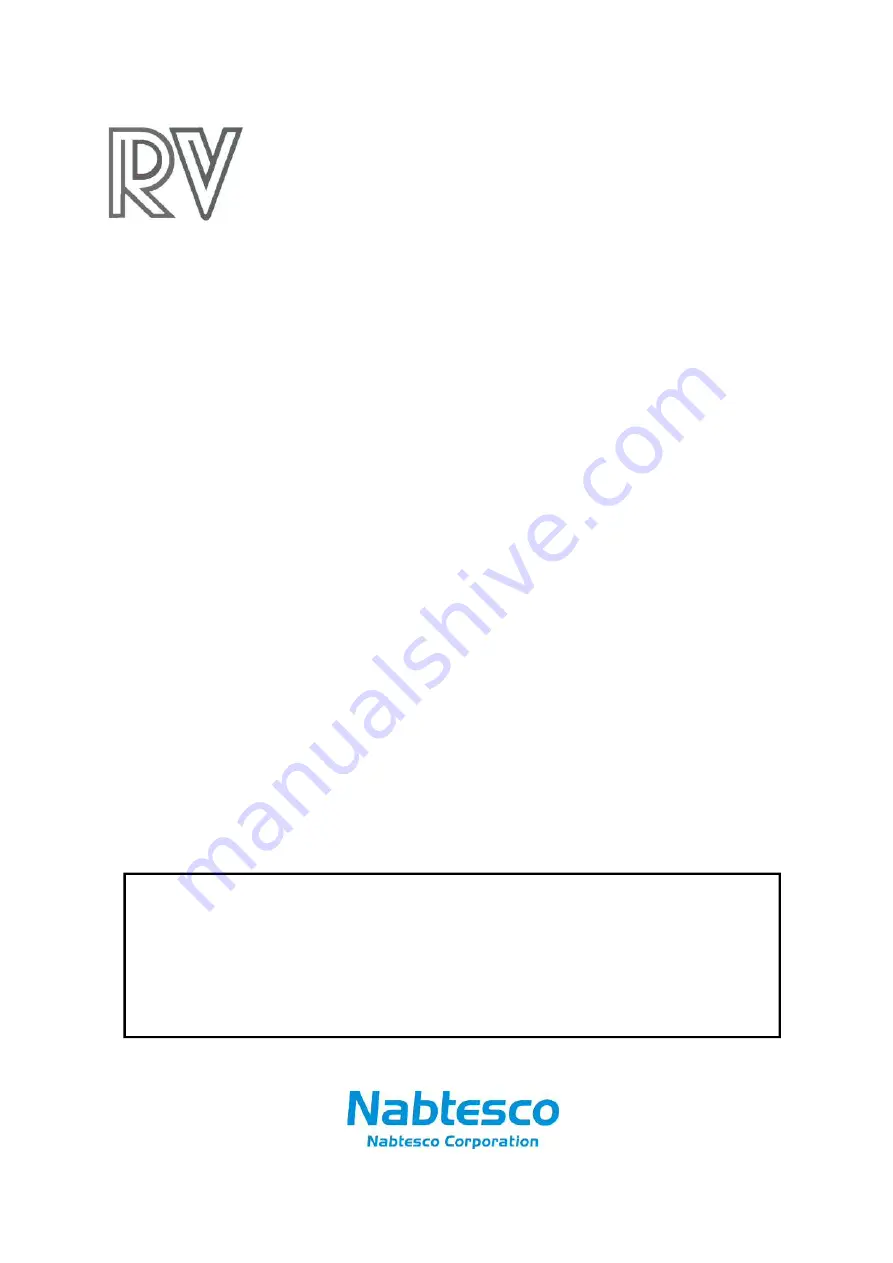
ERD15018A
2016/10/01
Precision Reduction Gear
RV
TM
High Precision Gearhead
RH
Series
Operation Manual
<Applicable model>
RH-
E
RH-
C
RH-
N
above indicates the torque code (number).
For the applicable models, refer to “Model” indicated on the shipping label of the product.
This manual must be thoroughly read and understood before using the product.
Be sure to deliver this operation manual to the system manager and the person in
charge of the operation.
Keep this manual in the specified location so that it can be immediately referred to
whenever necessary.
®